GEMS Engineering
GEMS Engineering is a Hungary-based research and development company working on the International Thermonuclear Experimental Reactor (ITER) project and has now implemented the 3DEXPERIENCE platform on the cloud. The company uses the platform, including the Digital Equipment Continuity industry solution experience, to unify all data and stakeholders in a single environment.
Engineering a fusion-powered future
In a small Provence town in southern France, experts from 35 countries have come together on one of the most ambitious energy experiments in the world: the International Thermonuclear Experimental Reactor (ITER) project.
ITER will be the world’s largest tokamak – a magnetic confinement device designed to prove the feasibility of fusion as a large-scale and carbon-free energy source, based on the same principle that powers our Sun and stars.
Hungary-based research and development company GEMS Engineering is fully devoted to the success of the ITER project. In fact, most of GEMS’ main projects relate to ITER’s diagnostic systems. For example, it has developed an erosion deposition monitor – a mission-critical device that keeps track of the level of erosion inside the ITER tokamak. Fusion reactions occur in a state of matter called plasma – a hot, charged gas made of positive ions and free-moving electrons. When this plasma interacts with the wall of the fusion device, it can cause material erosion, dust formation and tritium retention – which can significantly impact its operation. GEMS’ erosion deposition monitor allows ITER engineers to observe the tokamak’s erosion or deposition status remotely.
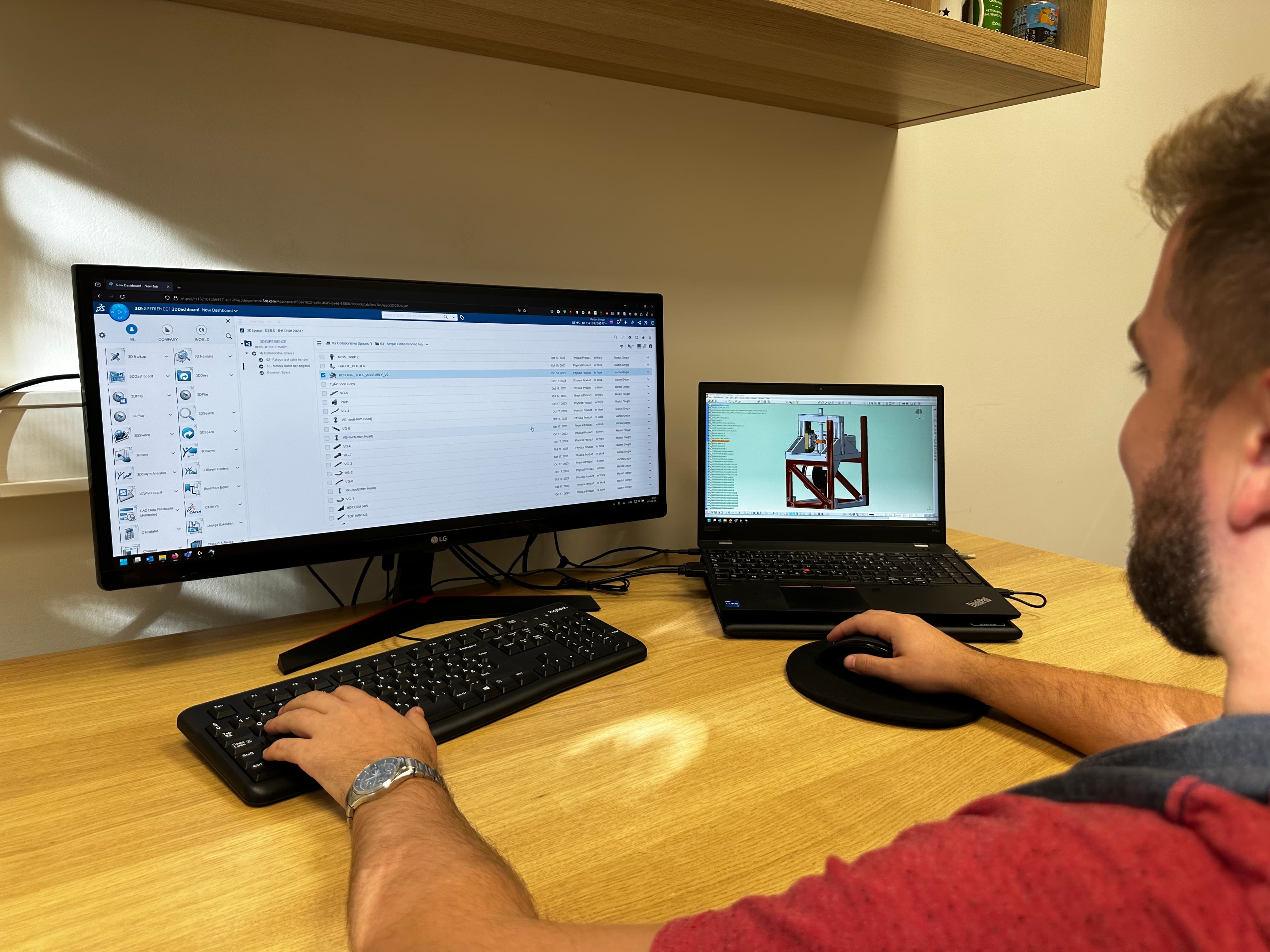
Challenge
To create complex products like this for ITER, GEMS collaborates closely with the Fusion Technology Department at the Hungarian Research Network’s Centre for Energy Research (EK).
Engineers from the two organizations need to work together on the initial concepts for the various diagnostic systems – a process which involves extensive research and development. They then need to complete multiple design iterations using mechanical engineering and analysis before moving through the prototyping, manufacturing, testing, final review and installation stages.
But there was a fundamental challenge for GEMS’ engineers. EK had adopted Dassault Systèmes’ 3DEXPERIENCE platform. However, since GEMS was using a different system, they found collaborating difficult. Communication was ineffective, and they could not work in parallel on the same projects. All of this was costing precious time and money.
Solution
Since both EK and other players working on the new Paks II power station use Dassault Systèmes technologies, and GEMS itself was using Dassault Systèmes’ CATIA V5 application for computer-aided design and engineering, GEMS saw the adoption of the 3DEXPERIENCE platform on the cloud as the logical next step to take its business forward.
GEMS enlisted the help of local partner Cadterv, who demonstrated how the 3DEXPERIENCE platform could unite users from GEMS, EK and other key stakeholders in a single environment through which they could not only access the same data, but also work in parallel on the same projects. Cadterv also showcased how using POWER’BY could enable GEMS to import its existing CATIA V5 files into the 3DEXPERIENCE platform, preserving its legacy investment and avoiding significant rework.
Since the platform is cloud-based, GEMS avoided a lengthy implementation and was able to give its engineers immediate access to the 3DEXPERIENCE tools. Ongoing training and consultancy services from Cadterv have ensured that GEMS gets the most from its investment.
Thanks to the 3DEXPERIENCE platform, we have strengthened our position in a competitive market. Not only can we collaborate more effectively with our key partners, but we can compete with bigger actors in the energy sector.
Benefits
Using the 3DEXPERIENCE platform to better organize, manage and collaborate on its concept designs is changing the game for GEMS, facilitating systematic product data management and more effective project management, leading to a 15% increase in efficiency.
Now, GEMS’ engineers can work in the same environment as their colleagues at EK, exchanging information directly within the platform instead of communicating via e-mail and other channels. And, thanks to the platform’s ability to enable concurrent design, experts from the two companies can work in parallel on innovative diagnostic systems for the ITER project from the early ideation stages through to mechanical engineering and analysis, prototyping, manufacturing, testing, final review and installation.
Moreover, because the platform is on the cloud, engineers can work on a project from anywhere in the world, on any device, at any time – whether working from home or traveling on business.
There’s more to come. GEMS believes adopting the 3DEXPERIENCE platform will strengthen its position in the race to construct the new Paks II power station, enabling it to easily exchange information with other partners in the region’s energy ecosystem. It also plans to expand its use of the 3DEXPERIENCE platform to leverage simulation capabilities from SIMULIA. This would allow it to better evaluate its products’ performance in the virtual world before committing to physical prototypes – enabling it to innovate even faster and, ultimately, help it advance the move to fusion energy and clean energy.
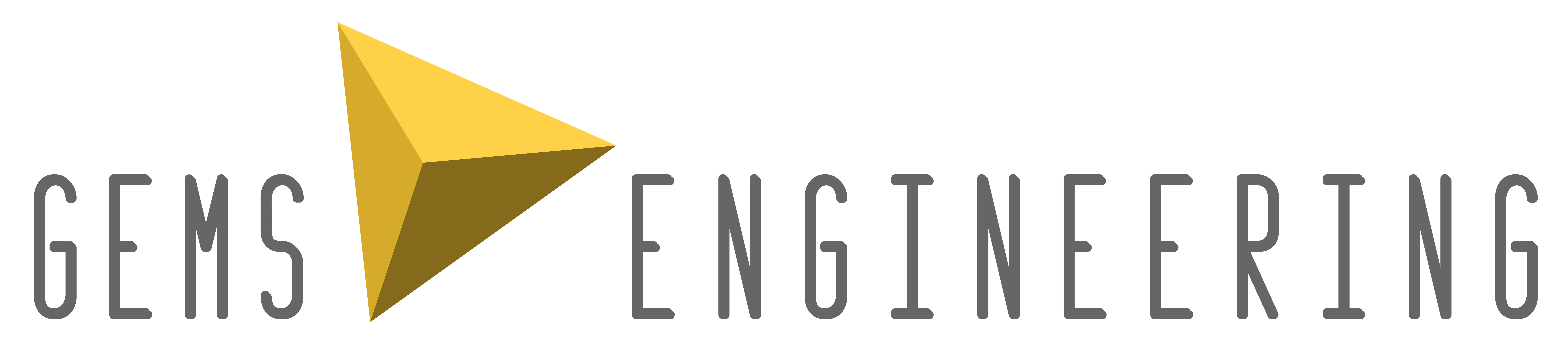
Focus on GEMS Engineering
GEMS Engineering serves the research and development market by offering innovative engineering and managerial solutions for projects involving substantial amounts of human expertise. The company supplies solutions covering the whole development process: from initial concepts through prototype manufacturing, testing and installation of the final product. Its main area of focus is fusion technology.
For more information: https://gems-engineering.com/
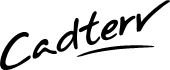
Focus on CAD-Terv
CAD-Terv Engineering Ltd. has been offering professional services for the implementation of Dassault Systèmes 3DEXPERIENCE solutions since 1997. The company assists its clients in choosing the ideal program suite and hardware by solving company-specific issues and organizing product demonstrations. It also offers consultations to help users with their everyday work, as well as tailor-made training courses.
For more information: www.cadterv.hu/en/