GEBERIT - Customer Story
Sanitary product manufacturer Geberit leverages the 3DEXPERIENCE platform for handling mechanical engineering and design management, thereby transforming the company’s entire approach to product development and collaboration.
Design meets function in the bathroom
Winner of the iF Design Award, the Geberit Olona floor-even shower tray is as stunning as it is functional. Made from matt white resin stone, the shower tray’s refined and elegant design features soft shapes and a subtle drain surrounded by a thin chrome ring, which appears to float. It’s the epitome of the Swiss sanitary company’s motto “design meets function,” and one of many innovative ceramic products it has developed using the 3DEXPERIENCE® platform.
“We designed the flowing shower surface using the CATIA Imagine and Shape surface design app on the 3DEXPERIENCE platform,” said Ian Randle, designer at Geberit. “The topography of the surface is very sympathetic to the way that the water moves. It also has very good drainage qualities, allowing us to achieve the desired hydrodynamics with minimal depth. Without CATIA and apps like Generative Shape Design for quickly modelling generative shapes, it would have been far more difficult to achieve that seamless flow. And it would also have taken 10 times longer.”
Geberit implemented the 3DEXPERIENCE platform to bring innovative new designs like the Olona shower tray to life and support its growth in the sanitary ceramics segment. Long known for its “behind the wall” products, including cisterns and drainage systems, the company has expanded its ceramic fixtures offering through a series of acquisitions to deliver a complete end-to-end bathroom solution.
With new companies, manufacturing plants, people and expertise to manage, Geberit needed a solution to bring everyone together and standardize its ceramics product development approach. The manufacturer turned to long-term technology partner Helbling to help make the right decision. As a long-term user of CATIA software for product design, it was a natural choice for Geberit to adopt the 3DEXPERIENCE platform and consolidate its technology landscape. A single platform – supporting all processes from ideation to production – would help the company to launch new products faster, master the increasing complexity in its products and move away from siloed thinking towards a data-based approach across all disciplines.
“Since the integration of the ceramics business, we have been able to optimally combine systems in front of and behind the wall,” said Martin Ziegler, head of Group Division Products & Operations at Geberit. “The decision to bring the ceramics business to the 3DEXPERIENCE platform was to further harmonize our infrastructure. We wanted to bring our business onboard to a modern platform that set a new standard for how we work. The driving force was to achieve global, company-wide cooperation between our departments.”
Today, Geberit is rolling out the 3DEXPERIENCE platform in a phased manner, covering the design, development and engineering departments. It’s also using the tooling, equipment and plant layout disciplines up to prefabrication, where the 3DEXPERIENCE platform is used on the shop floor.
“We wanted to be able to exchange data across the company easily,” said Thilo Cramer, head of CAX Applications at Geberit. “Before, we had several different systems to manage and support. Moving to one system made much more sense.”
The decision to bring the ceramics business to the 3DEXPERIENCE platform was to further harmonize our infrastructure. We wanted to bring our business onboard to a modern platform that set a new standard for how we work.
New design capabilities drive innovation
The Industrial Design department was one of the first to take advantage of the 3DEXPERIENCE platform. It’s already having a significant impact on the way ceramic products are being developed.
“We have new capabilities that we didn’t have before,” Randle said. “We have more design freedom, can do things faster and in all respects, we have integration, whereas before we had none.”
Using roles within CATIA, Randle and the rest of the Industrial Design team can experiment with more complex designs and surfaces.
“The whole design process is easier and more efficient, and we can determine the feasibility of new designs a lot quicker,” he said. “It’s allowing us to create designs with flowing shapes that we couldn’t attain before.”
The design team also benefits from closer interaction with the engineering department to test form and function, critical as the company applies eco-design criterion to all products in development to align them with its sustainability goals.
“For example, I’m working on creating design surfaces that reduce water consumption,” Randle said. “Using the 3DEXPERIENCE platform, we can quite quickly design a functional surface and then send it to the simulation team to see how it will perform. We then integrate those findings back into the next iteration to come up with the best, most sustainable design. From my experience, it is the first time we’ve had this organic way of working where design and simulation feed into each other. It means that within a given timeframe, we can examine more design possibilities and improve what we bring to market.”
From the 3D model, we can identify potential problems early on and avoid production reruns that can increase waste and drive up costs.

Collaboration and knowledge boost efficiency
Having access to an entire back catalog of product designs is also bringing significant efficiencies to Geberit’s product development processes.
“The shared knowledge pool has been a huge advantage,” said Jürg Huber, head of Research and Development Applications, Corporate Information Services at Geberit. “Previously, we held all our expertise in lots of different systems, but that knowledge was of no use to a colleague on a different system. Now, we have this pool of knowledge within the company, this vast database on the 3DEXPERIENCE platform that we can tap into. It’s so valuable and something we can really nurture.”
Designers now have the option to start a design from scratch or consult previous designs to see what’s already available to work with. Then, using apps like CATIA Imagine and Shape, they can create and explore organic shapes and play around with materials and colors and test product feasibility early on. They can also see how the flushing and installation systems will work with the ceramic design, checking installation and assembly viability virtually.
“The 3DEXPERIENCE platform supports us to collaborate more closely with engineers to come up with the best design without compromising on functionality,” Randle said. “I was working on a shower enclosure project recently and it made such a difference being able to work closely with an engineer on the platform and consider all the assemblies and motion within assemblies. Typically, we designed single items, but with this shower enclosure I was able to see all the working parts, the rollers, handles and latches, and could determine if there was going to be any interference. Being able to collaborate with the engineers has made my job so much easier.”
We have more design freedom, can do things faster and in all respects, we have integration.
Tackling ceramics mold-making complexity
One of the key challenges of working with ceramic products is that they’re highly susceptible to deformations in the production process. The fine fire clay washbasin in the Geberit ONE range, for example, is very thin and has a large surface of up to 120cm in width. Producing it on an industrial scale was challenging, especially when it came to developing the right mold and production process. But thanks to the close collaboration between its product developers and ceramic experts across Europe, Geberit created the right 3D models for producing the molds.
“Ceramic is a natural product and a very complex material to deal with due to its tendency to shrink and distort during the drying and firing stages,” Cramer said. “While it’s in the kiln, the geometry can change significantly, and this is something we must take into account.”
Geberit worked closely with Dassault Systèmes experts to develop the most effective mold-making design approach on the 3DEXPERIENCE platform.
“We had already extensive internal knowhow, but it was very helpful to bring in the specialists who supported us to find the right methodology in new areas like ceramics,” Huber said.
Now, using the 3DEXPERIENCE platform, Geberit’s mold designers can generate a specific distortion geometry and explore a variety of ideas with the 3D data model to come up with the best result. All of this happens early in the product development phase to avoid the need for producing many costly and labor-intensive physical prototypes.
“We’ve implemented a method to create reference models, where we can see how a product will look when it comes out of the kiln and which we can use for collaboration,” Cramer said. “From this, we can create the molds, considering distortion and shrinkage. And if, for example, something changes, it will automatically update the whole structure, including the mold and all related parts.”
Geberit also uses the 3DEXPERIENCE platform for producing the ceramic molds, computing, and simulating the required toolpaths, and automatically generating the machine code for its NC machines.
“From the 3D model, we can identify potential problems early on and avoid production reruns that can increase waste and drive up costs,” Huber said.
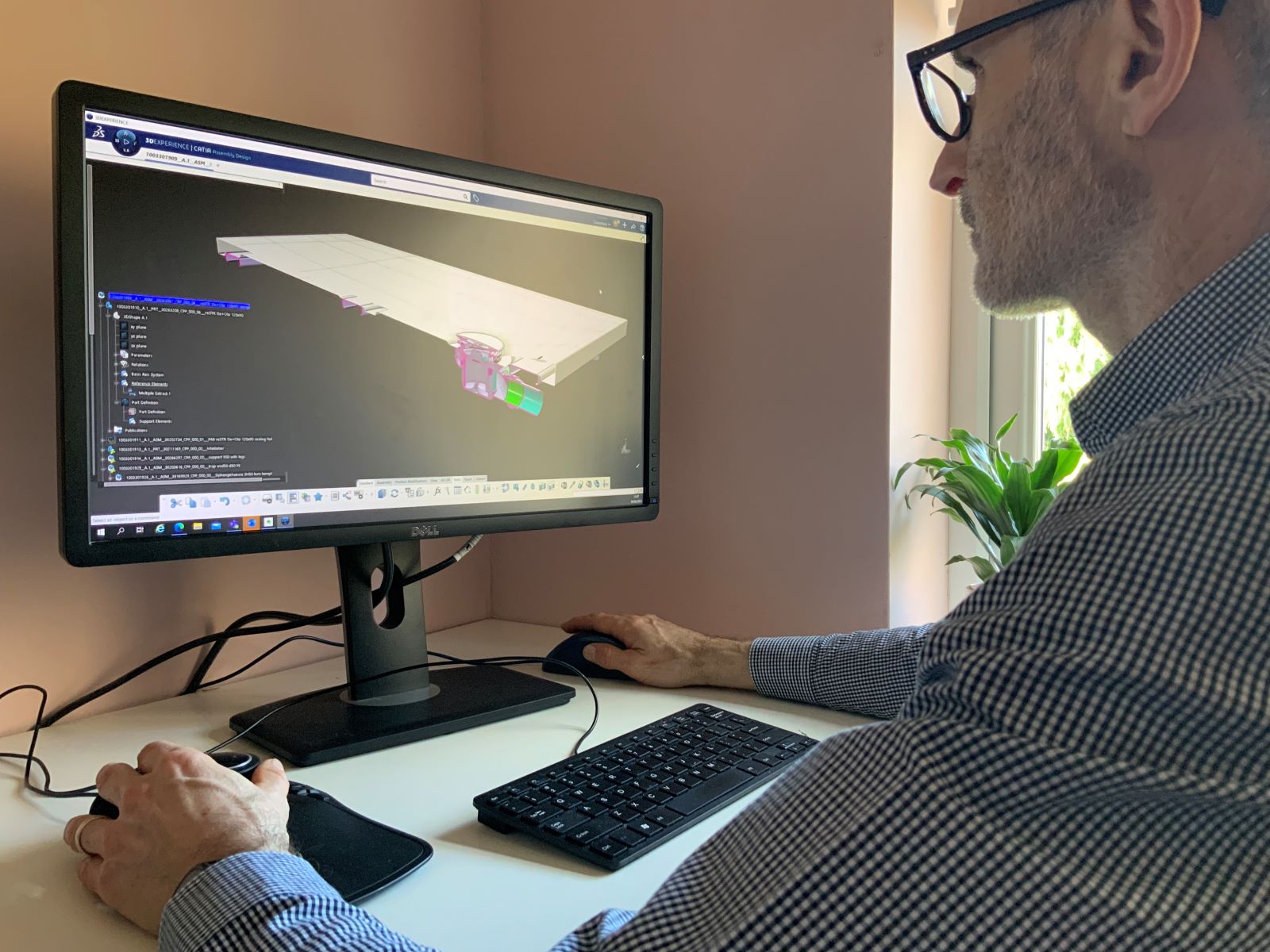
Standardizing manufacturing plants
Geberit’s 3D approach follows through into its manufacturing plants too, where it has standardized its processes as part of its vision to operate as one unified company.
“Our aim was to do everything in 3D and switch to a 3D plant layout,” Cramer said. “That was another of the driving forces for choosing the 3DEXPERIENCE platform. We needed a system that would allow us to establish the same practices for each one of our 29 production plants.”
Now, when Geberit needs to modify a process flow and adapt the factory layout, it can do so virtually before committing to the physical change.
“We have standardized several production plants on the 3DEXPERIENCE platform and created a virtual twin of our equipment and buildings so that we can simulate the trajectories of the machines when installing and moving them around to make sure they work,” Cramer said. “In some areas we’ve also simulated our machinery, including robot pathways to avoid any errors in the production process.”
Looking ahead, Geberit plans to visualize and define processes, such as material flow and ergonomics at work, and create the work instructions for production automatically based on the data in the platform using DELMIA.
“Our one-system approach means we can use existing setups in other locations,” Cramer said. “That’s the main goal: to operate everywhere in the same way, using the same internal support. It will allow us to flex our engineering and manufacturing resources.”
We have standardized several production plants on the 3DEXPERIENCE platform and created a virtual twin of our equipment and buildings.
Strong commitment and partnership
Geberit’s strong relationship with Helbling and the Dassault Systèmes industry team has been key to managing an IT implementation of this scope and scale.
“Helbling has made life much easier for us,” Huber said. “The team contacts Dassault Systèmes with our requirements and brings the right people to the table. We’ve also benefited from Dassault Systèmes’ premium support, which allows us to get the information we need first-hand. We communicate and collaborate via the 3DEXPERIENCE platform in the so-called IFWE loop to manage queries and have bi-weekly planning calls to track progress. Rather than exchanging information via email, we do everything through this IFWE community portal.”
Before committing to such a large project, Cramer recommends considering the impact it will have on all aspects of the business and ensuring the required resources are in place.
“Think in the beginning what the platform will mean for the company,” Cramer said. “If you really think you can handle it internally, you need the right people and strong commitment from all key stakeholders. You must be prepared to change your processes and adopt new ways of working. We will end up with around 500 to 600 users on the 3DEXPERIENCE platform and it can take a while to get everyone onboard and convince them it’s worth the effort.
“Geberit is working constantly to enhance the system both in cooperation with Dassault Systèmes and with our own features and functions based on CAA programming. We decided to work on premise and have put considerable resource into managing the complex infrastructure with distributed collaboration servers. Together with Dassault Systèmes we’re committed to overcoming the big challenge of meeting users’ expectations in terms of functionality and performance," Huber said.
“We’re certainly in a better place now than we were before and we’re really benefiting from all this shared knowledge,” Randle concluded. “It has completely changed the way we innovate.”

Focus on Geberit
Headquartered in Rapperswil-Jona, Switzerland, Geberit Group is a European leader in the field of sanitary products. With 29 production facilities worldwide, the company operates with a strong local presence in most European countries, providing unique added value when it comes to sanitary technology and bathroom ceramics.
For more information: www.international.geberit.com

Focus on Helbling
Founded in 1963, Helbling Group positions itself as an interdisciplinary nexus of engineering and consulting expertise. The independent group is run by 34 managing partners and employs 540 professionals at locations in Switzerland, Germany, the US, and China. Helbling’s main focus is on providing selected services in the fields of technological innovation and business consulting. Its unique combination of expert skills in both ensures it is capable of dealing with tasks not only by taking a specialist, project-oriented approach but also from the perspective of the entire company.