F.MED
Japanese medical device manufacturer F.MED is taking advantage of the Device Mechanical Engineering and Collaborative Engineering Management solutions to develop a microsurgery assistance robot system, and bring it to market.
Saving more lives through microsurgery assistance robot systems
There are certain surgical procedures that must be done with specialized microscopes and instrumentation because they’re difficult to see with the naked eye. Called microsurgery, this discipline typically involves repairing or reconstructing tiny structures in the body such as blood vessels and nerves that are less than a few millimeters in diameter. It’s used in everything from post-cancer breast, head and neck reconstruction surgery to treating lymphedema and reattaching amputated fingers and thumbs.
As microsurgical techniques become more advanced, the field may continue to gain traction across all sorts of medical specialties because it improves patient survival rates and quality of life. Yet because microsurgery is technically so demanding, only a few surgeons are trained to perform it, meaning it’s not something that’s readily available at every hospital. Microsurgery assistance robot systems show great potential for overcoming this issue, helping to keep pace with demand and overcome the human limitations of performing such delicate microsurgical procedures, particularly in terms of stabilizing hand tremors.
Among the companies working to bring this new generation of robots to market is medical device manufacturer F.MED in Japan. The startup is in the process of developing an advanced robotic manipulating arm that surgeons will be able to operate remotely from a large monitor, where they can view every detail up close. Rather than holding the fine instruments themselves, the surgeons guide the movement of the robot manipulating arm with separate controls for enhanced precision and dexterity.
“By creating an environment where microsurgery can be done in many hospitals using robots, we can help to improve the quality of life of patients and help them return to society,” said Keita Shimomura, CEO of F.MED.
Our design work, which used to take about four months in total, is now completed in about three months.
From research project to commercial robot
F.MED’s microsurgery support robot began life as a research project led by Susumu Oguri, a former researcher at Kyushu University’s Advanced Medical Open Innovation Center, and now CTO of F.MED. Together with Shimomura, he decided to progress his work beyond the concept stage and commercialize it. Both recognized how advances in robotics are helping to transform the way that people work and saw an opportunity in the medical market to develop systems that shorten the time it takes for surgeons to acquire new skills.
“The two of us talked about whether it would be a waste to simply turn our research into a paper and call it a day, so we decided to start our own company and continue development for commercialization,” Shimomura said.
At first, F.MED used the SOLIDWORKS CAD application to develop elements of the robotic manipulating arm. The system quickly grew in complexity and involved more moving parts as well as electrical wiring and piping. With almost 10,000 objects to manage – and growing – it became apparent that the company would need a robust product lifecycle management solution.
“As the assemblies became larger and the number of parts to be handled increased, we needed something more agile and scalable to manage our product development,” Oguri said.
Dassault Systèmes recommended that F.MED switch to the 3DEXPERIENCE platform on the cloud for its PLM capabilities. Selecting the cloud solution meant that F.MED could scale up its usage any time to meet its growing needs.
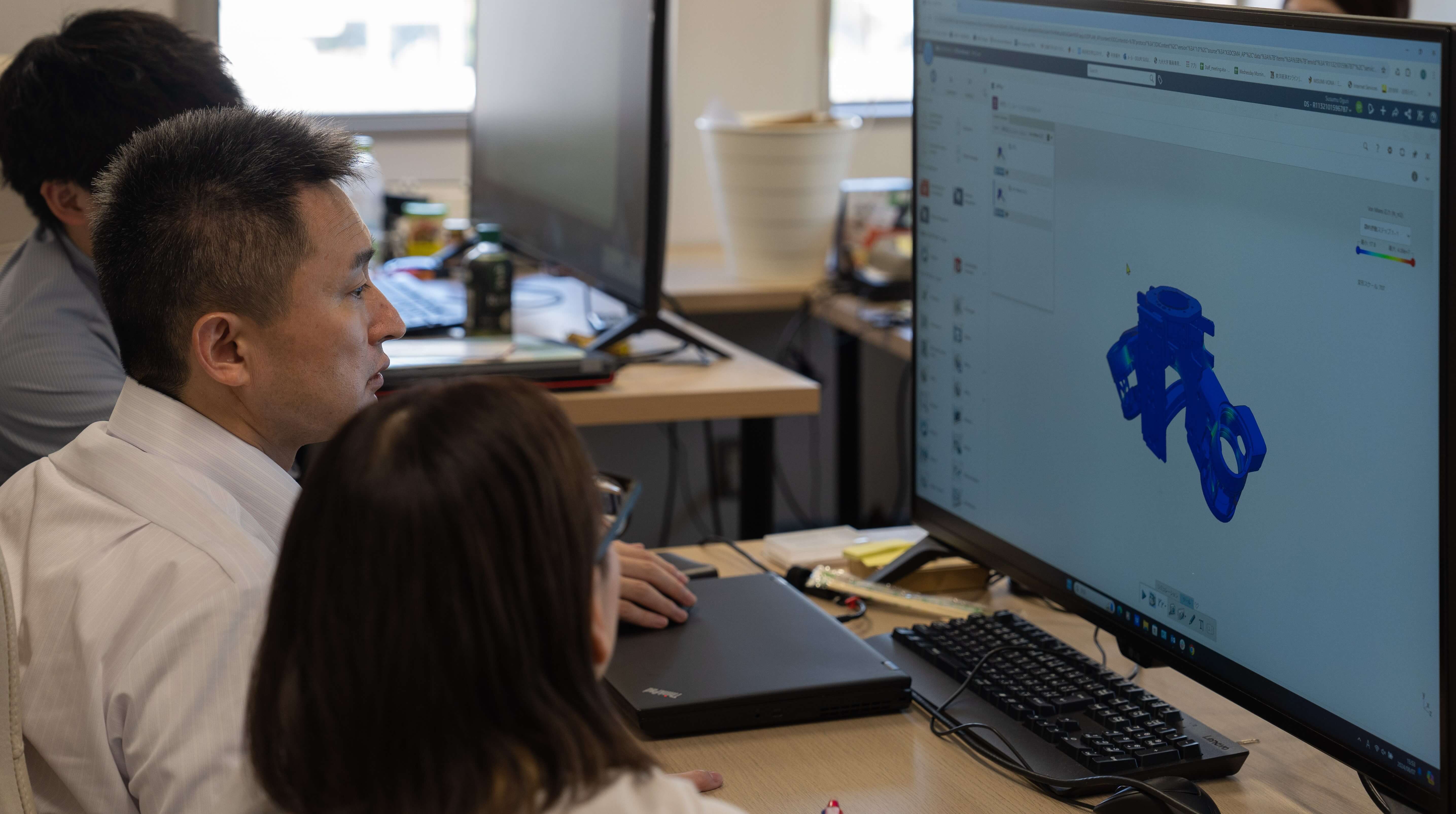
Scaling up with the cloud
Today, F.MED uses the 3DEXPERIENCE platform on the cloud to manage all aspects of the product development lifecycle of its microsurgery robot. Investing in enterprise-level technology that’s well regarded across the industry and beyond gives F.MED confidence that the platform will keep pace with its business ventures well into the future.
“We know that companies much larger than us rely on the 3DEXPERIENCE platform, so we have no concerns about its ability to support us, even as our robot development becomes more complex,” Shimomura said.
Already, CATIA allows F.MED to effectively handle large assemblies while SIMULIA delivers the capabilities to support MODSIM – combined modelling and simulation. The company also values the ability to access the platform remotely and support effective collaboration.
“There are times when we have people in separate locations working on the same design,” Oguri said. “The 3DEXPERIENCE platform makes it easy to do that and share work data – something that used to take a lot of time.”
The company also appreciates the opportunity to take advantage of the 3DEXPERIENCE for Startups program, which offers affordable access to the platform as well as e-learning modules and technical support. If Oguri or the team have a question, they can post it in the dedicated community and get a fast response. And because F.MED only pays for the technology it uses, it can keep costs under control.
“It’s a very cost-friendly plan and a great option for venture companies starting small,” Oguri said. “To begin with, you can sign up for the minimum number of accounts you need and then add more as new employees join the company. This flexibility has really helped as we grow.”
The 3DEXPERIENCE platform keeps a record of all our development which we can use for certification, saving us a huge amount of time.
Integrated design speeds up development
Feedback from the F.MED team about the 3DEXPERIENCE platform has been very positive so far, and they’ve noticed they’re speeding up engineering time thanks to the ability to work concurrently on designs and integrate their 3D models earlier. Before, each designer worked independently on their own CAD model for up to three months before looping back to the rest of the team to determine how parts were joined together and fitted into the wider assembly.
"It took us about a month to resolve all the design issues associated with integrating our different 3D models and determine how to join the components,” Oguri said. “Now, we can take all these issues into account in the early design stages, overcome any challenges more flexibly and make sure we’re meeting all specifications. It means that our design work, which used to take about four months in total, is now completed in about three months.”
This transparency is critical for keeping track of all parts and ensuring consistency in the design and construction of the final product. The team also appreciates being able to carry out all design and structural analysis processes in one place without having to switch between different applications. Now, thanks to MODSIM, they can design a component, test its functionality in the platform and quickly develop the next iteration based on the simulated results.
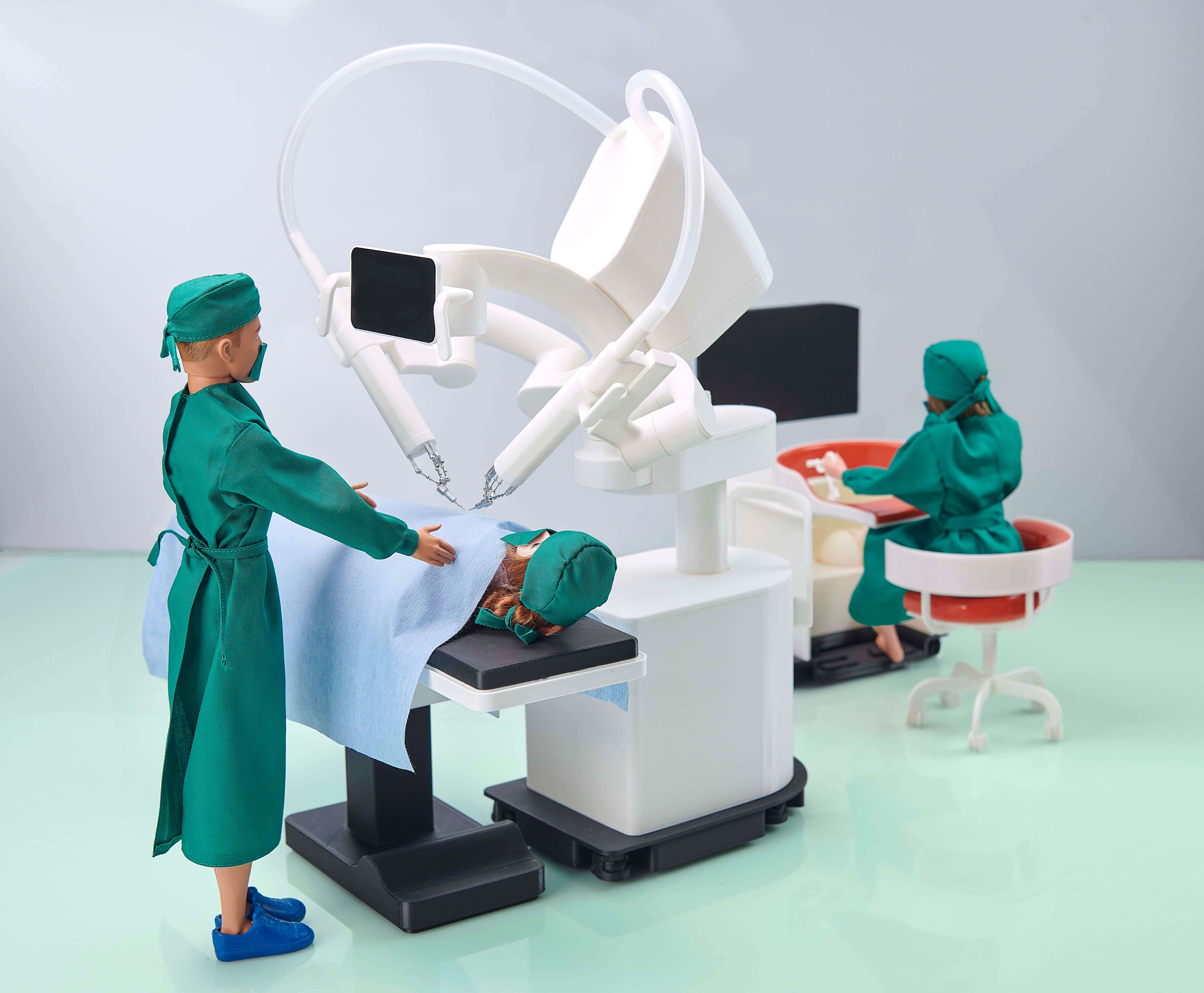
Securing industry certification
Having all product data managed centrally is crucial for maintaining full traceability of the change history of the 3D model, handling the approval process and getting the robot certified in Japan and, eventually, the global market.
“We are preparing to obtain approval as a medical device in Japan in 2025,” Shimomura said. “The 3DEXPERIENCE platform keeps a record of all our development which we can use for certification, saving us a huge amount of time.”
So far, F.MED’s microsurgery assistance robot system has been demonstrated in collaboration with specialists at Kyushu University and other plastic surgeons. The company is now working on a third-generation prototype before it launches the robot to market. In future, F.MED hopes to develop a support system on the 3DEXPERIENCE platform which would allow doctors to receive assistance during surgery from remote experts.
“I believe that the 3DEXPERIENCE platform is capable of doing this, so I am looking forward to exploring how we can deliver it alongside our medical robots,” Oguri said.
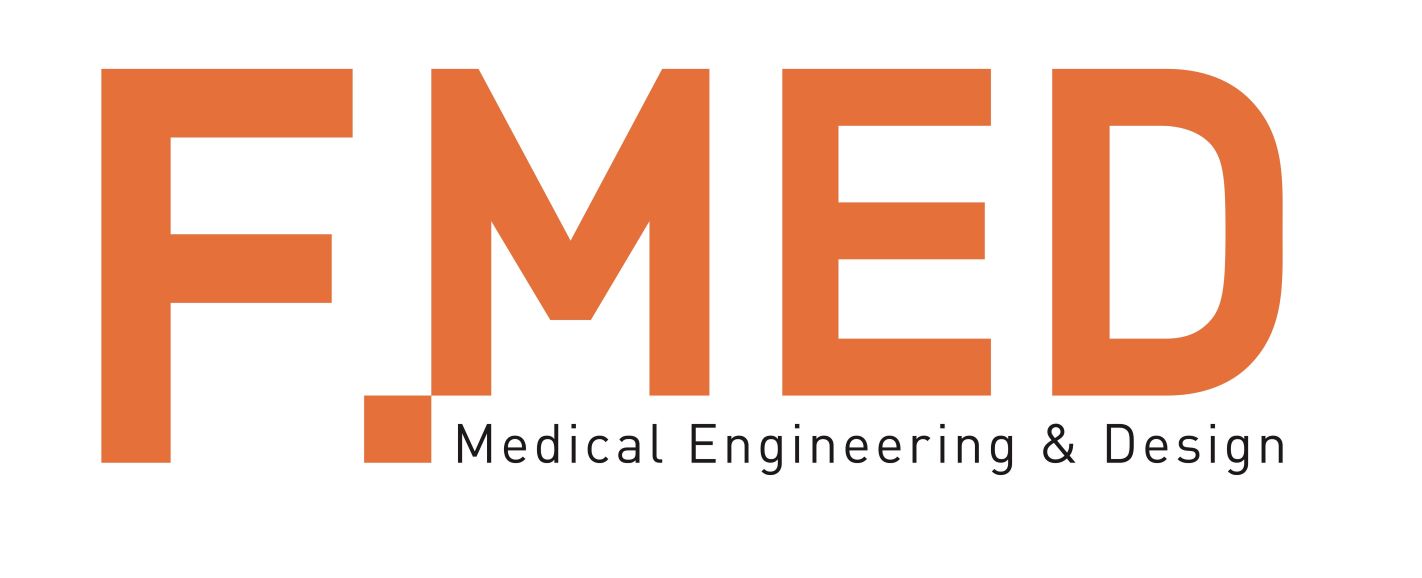
Focus on F.MED
Based in Japan, F.MED combines academia and business knowledge, exploration and passion to commercialize its microsurgery assistance robot.
For more information: https://f-med.co.jp