Ferrit
Czech mining equipment specialist Ferrit needed full visibility in its entire product lifecycle to boost its competitive edge and operate more nimbly as it wants to create a new generation of efficient, low energy mining logistics solutions. The company decided to follow Dassault Systèmes’ Value Engagement methodology to proof the value of the 3DEXPERIENCE platform, set shared, measurable objectives, define the overall digital roadmap and follow an implementation plan.
Shifting the focus to sustainable mining
Mining is one of the most energy intensive industries in the world. It accounts for 10% of world energy consumption and faces growing calls to mitigate its environmental impact. For suppliers like Ferrit, a Czech manufacturer of mining transport systems, meaningful change requires a radical rethink of what they do and who they supply their equipment to. Traditionally, the majority of Ferrit’s business has come from manufacturing suspended monorail transport systems, largely used in coal mining. But now, the company is looking to more sustainable revenue streams.
“With the rising focus on environmental, social and governance (ESG) policies, Ferrit has put a five-year plan in action that will reduce our reliance on companies that emit greenhouse gases,” said Petr Mohelnik, CEO of Ferrit. “Thermal coal customers accounted for 50% of revenues in 2019, down to 24% in 2020, 23% in 2021, and we are targeting this sector to be much lower within five years. We are also increasing our investment in designing equipment like electrical vehicles that helps client sites to reduce their carbon footprint and improve worker safety.”
Today, the company mainly produces traction vehicles with internal combustion engines. But eventually, it hopes to convince the market that electric drives with rechargeable batteries are a viable long-term solution, protecting both the environment and mine workers by cutting down on air pollution and noise.
At the same time, Ferrit has embarked on a company-wide digital transformation journey to boost its competitive edge and operate more nimbly.
“Digital transformation is not about if we go for it but when we go for it,” Mohelnik said. “If we want to keep up with the outside world, we must be on top of the digital transformation. Digitalized research and development will help us to react faster to customers’ requirements and new market challenges such as creating more environmentally friendly mining vehicles. The ability to fully leverage the virtual twin will make the prototype and testing phase much shorter.”
Following a comprehensive audit, Ferrit chose the 3DEXPERIENCE platform to power its future business.
“We decided to digitalize our product lifecycle management (PLM) solution,” said Martin Kopecek, IT manager at Ferrit. “There are few digital platforms on the global scale we required, so the 3DEXPERIENCE platform was the clear choice. Our vision is to be on all continents, and we will dedicate the time saved with this digital platform to further expansion.”
Digital transformation is not about if we go for it but when we go for it. Both, DYTRON and Dassault Systèmes asked us the right questions about our vision to identify which are the most added value processes to transform first.
A value-driven journey
Ferrit already used Dassault Systèmes solutions, including SOLIDWORKS and 3DVIA Composer, in its design department.
“The current usage of this software was one of the main reasons for our decision to implement the 3DEXPERIENCE platform,” Kopecek said. “Maintaining these applications is a very important part of the project.”
“Another element is to connect all processes and departments such as purchase and production, as we want to ensure we are all working from the same data model,” added David Grendysa, marketing manager at Ferrit. “This will not only enhance collaboration but streamline product development. Previously, our system was fragmented, with data stored in numerous spreadsheets and communication done via e-mail. We needed to consolidate everything and work in a more project-oriented manner.”
Ferrit teamed up with Dassault Systèmes business partner DYTRON to help define the right set up and manage the implementation.
“DYTRON is one of the most customer-oriented providers of the 3DEXPERIENCE platform,” Mohelnik said. “They helped us choose which areas of the business to focus on digitalizing first and how the 3DEXPERIENCE platform would bring value.”
Ferrit decided to follow Dassault Systèmes’ value engagement methodology. This approach helps to validate the business value of the 3DEXPERIENCE platform, set shared, measurable objectives, define the overall digital roadmap and follow an implementation plan, centered on four key areas:
Assessment: This element identifies transformation needs and develops a business justification for the project. “We followed the methodology to understand our business drivers and link them to company objectives and expected benefits,” Mohelnik said. “Both, DYTRON and Dassault Systèmes asked us the right questions about our vision to identify which are the most added value processes to transform first.”
Definition: Here, all three companies worked together to understand Ferrit’s current processes and challenges, which they then used to design the transformation roadmap and shape the required solutions. “We’re focusing on the heavy machinery specific processes in the platform to achieve our transformation,” Kopecek said. “The demonstration using a sample of our product data and project processes really helped to make that decision. We defined the solution framework and divided it into three major phases, and have designed the architecture with roles and products that support our processes along with associated best practices.”
Commitment: By developing a secure roadmap, Ferrit is able to prepare for change as a company and embrace new ways of working, while mitigating risks. “We specified the need for out of the box functionality and covered all parts of the project cost, including total cost of ownership and return on investment (ROI),” Mohelnik said. “The ROI calculations were a very important part of our decision-making process and helped us commit to the rollout.”
Delivery: Ferrit established a team with representatives from every department to ensure all facets of the company are kept informed of progress. It is also following an agile methodology to break the project down into phases, each with measurable outcomes. “The agile methodology allows us to detect wrong directions sooner and not waste time,” Grendysa said. “Each phase is linked to ROI calculations, which guide our decisions throughout the implementation.”
Defined Performance Indicators
- 3%
reduction in material costs
- 10%
increase in efficiency in engineering
- 15%
increase in productivity due to standardization
Measured return on investment
To ensure the success of its digital transformation, Ferrit has set clear key performance indicators (KPIs) and firm targets for measuring the impact of the 3DEXPERIENCE platform.
“Our KPIs may be monitored as percentages of expected savings,” Mohelnik said. “This includes increasing the productivity of PLM users by 10% by easing access to data, reducing manual data entry and increasing the accuracy of BOMs. We also hope to reduce material costs by 3% by lowering scrap and repair costs and reusing parts. And finally, we have a KPI for increasing efficiency by 15% with standardization, such as by reducing the number of parts proposed and reducing the administrative costs of changes.”
In the Purchasing department, for example, Ferrit hopes that standardization will help to reduce the number of parts in stock and lower storage costs.

Project management is one of the core processes being implemented. It will help us to organize and classify project structures and effectively manage project flows.
Consistent project management
In the first phase of its digital transformation journey, Ferrit is rolling out the project and product portfolio management capabilities in ENOVIA on the 3DEXPERIENCE platform.
“Project management is one of the core processes being implemented,” Kopecek said. “It will help us to organize and classify project structures and effectively manage project flows. Using the management dashboard, we can track all project statuses and KPIs in real time to support quick and effective decision-making.
Ferrit hopes that this visibility will also lead to enhanced company-wide collaboration and information sharing.
“In the future, we believe that this system will allow us to streamline production and ensure everyone in the company works with the same data – from purchasing to production to service and maintenance,” Grendysa said.
The agile methodology allows us to detect wrong directions sooner and not waste time.
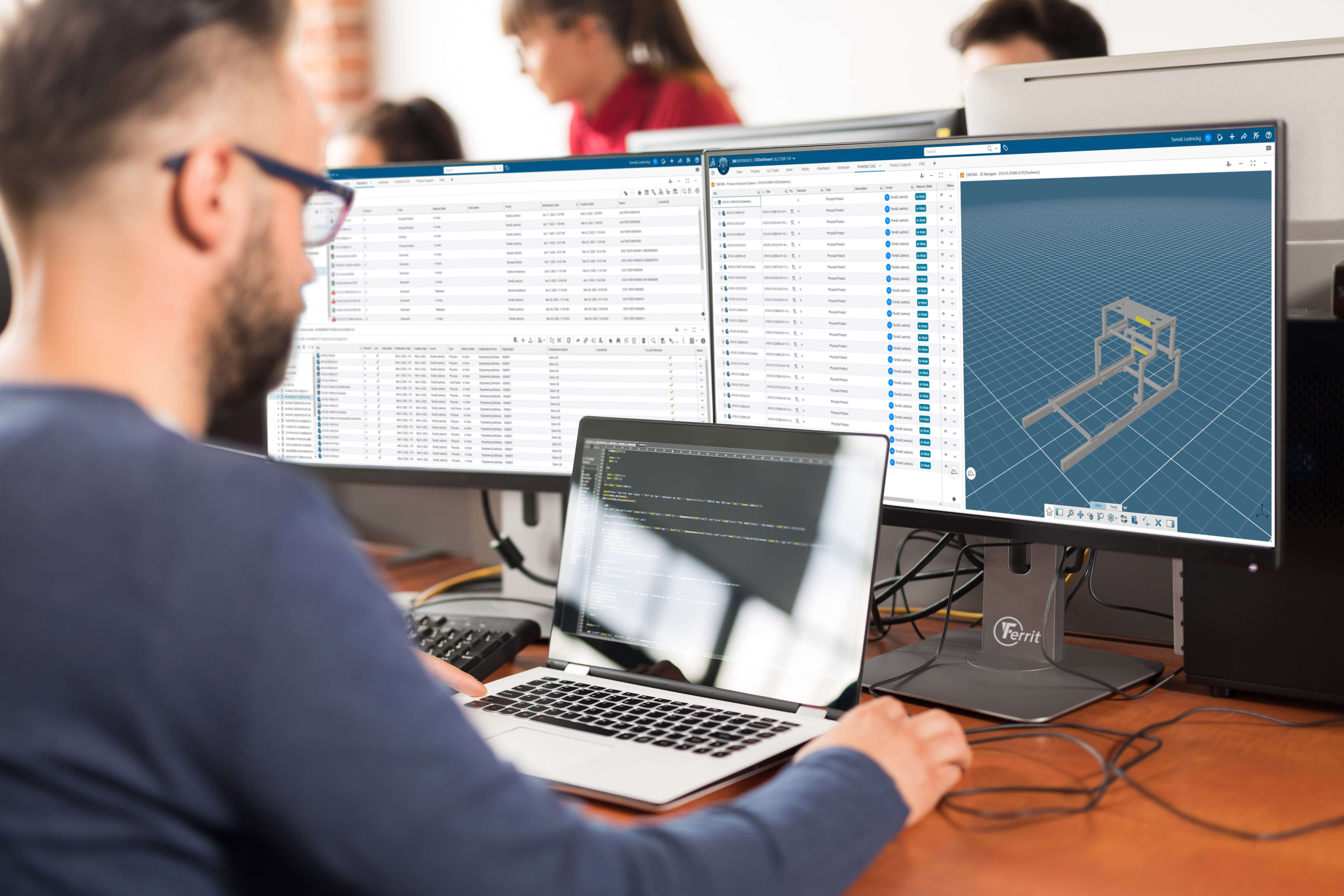
Towards virtual manufacturing
Ferrit has big plans for its digital transformation. Subsequent phases involve moving its research and development processes and product structure definition to the 3DEXPERIENCE platform. Eventually, the company will transform its manufacturing processes and product service support by embracing the virtual twin experience capabilities in DELMIA and taking advantage of the advanced simulation features in SIMULIA to test designs and verify the behavior of equipment in the virtual world. The result: Ferrit can still manage its design processes within SOLIDWORKS yet benefit from streamlined workflows across the product lifecycle on the 3DEXPERIENCE platform, enabling it to achieve full end-to-end engineering capabilities.
“DELMIA will support our production and service phases of the product lifecycle,” Kopecek said. “We will use it to plan and prepare our manufacturing processes and create work and service instructions. We will use a full 3D product definition to connect the dots between all departments.”
The company believes by taking advantage of virtual twins it will be able to develop innovative, new, sustainable products, including electric transportation systems.
“Our development is focused on reducing noise levels and carbon emissions in the mining environment,” Mohelnik said. “We can significantly influence the density of mining transport by solving the entire logistics system. By coordinating and controlling transport operations, our customers will need fewer locomotives and can actively reduce air pollution in the mine.”
The 3DEXPERIENCE platform is one of the key pillars in Ferrit’s mission to decarbonize and diversify its product portfolio while bringing new innovations to market faster.
“It’s very important to us that we will be able to reduce the number of physical prototypes we need to build and verify the behavior of our equipment in the virtual world,” Mohelnik said. “We will use advanced simulation and virtual twin capabilities in our design processes all the way through to manufacturing to speed up new product development and carry out more testing and verification tasks virtually – all in one single system. We strongly believe that we have entered into a strategic partnership with Dassault Systèmes and DYTRON to support our digital transformation and ensure our future success.”
Discover more about the Integrated Heavy Machinery industry solution experience.
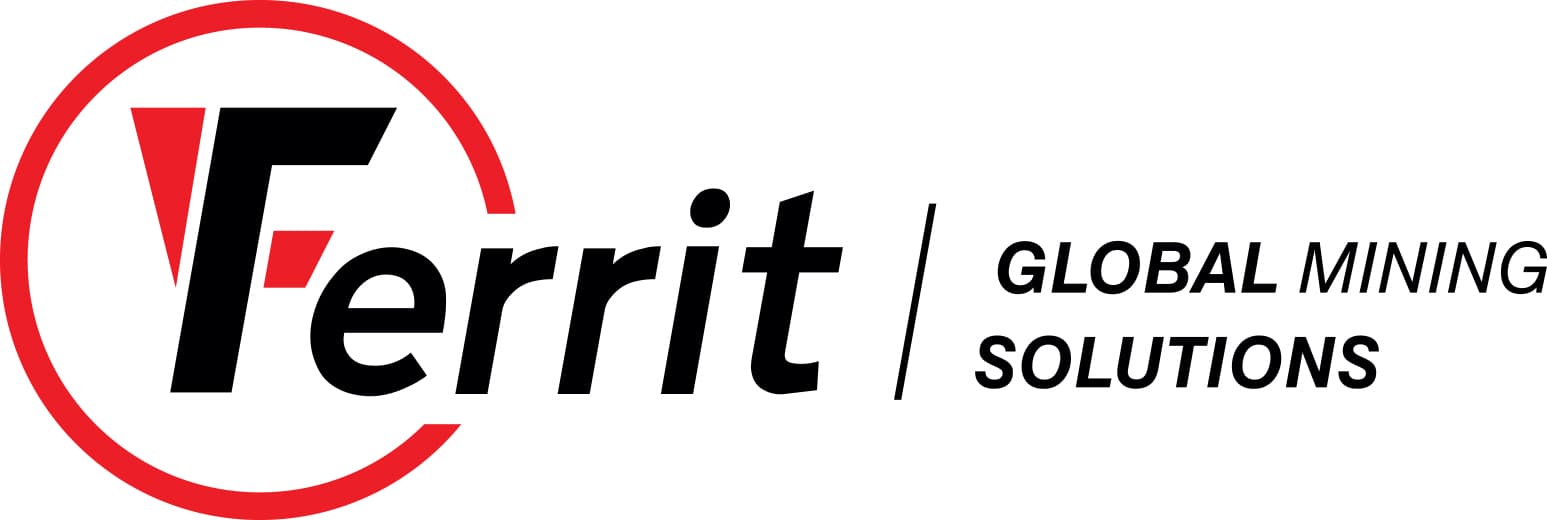
Focus on Ferrit
Ferrit is a privately owned Czech company that was founded in 1993 and carries out operations around the world. Initially established as a trading company, it has transformed into a manufacturing company with its own research and development department. The manufacture of suspended monorail transport systems makes up the largest share of its production activities, which has positioned Ferrit as a worldwide market leader.
For more information: www.ferrit.cz
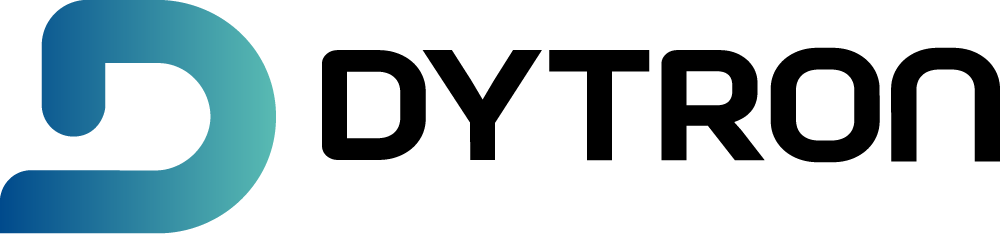
Focus on Dytron
DYTRON has more than 30 years of experience delivering CAD/PLM/APS systems from Dassault Systèmes. A reliable and long-term partner, the company provides its customers through digital transformation with support and advice, training and knowledge development, consultation and implementation services. DYTRON has unique know-how in development, design and manufacturing activities and the optimization of business processes in different industries, backed by a team of highly qualified and experienced professionals.
For more information: