Etteplan
Finnish technology service provider Etteplan provides software and embedded engineering and technical communication solutions to the world's leading industrial companies. The company has chosen the 3DEXPERIENCE platform to access all tools from a single platform. Using the Digital Equipment Continuity industry solution allows the team to improve collaboration with customers while achieving significant time savings and greater accuracy.
Isometric drawings make the difference in piping engineering
Over the last 40 years, Etteplan has grown from a small Finnish engineering firm to a global technology service company with around 4,000 employees and a turnover of €360 million.
Jari-Pekka Mielonen, regional manager at Etteplan, attributes this success to the company’s commitment to exceeding customer expectations. “Our customers choose us because we create solutions for smarter businesses,” he said. “We are not just a supplier; we are a partner. Our customers are our priority.”
Delivering on these promises requires constant innovation. “We are always looking for new ways to do things,” said Joni Saarenpää, Etteplan’s team manager. “Organizations come to us with specific requirements or problems that they don’t necessarily know how to solve, or they may have an idea that isn’t optimal. We must be able to respond quickly with an effective approach.”
To validate an approach, Etteplan relies on the generation of isometric drawings – 2D drawings representing 3D objects – for its piping works. The drawings detail the length, width and depth of piping in a single view.
The accuracy of these drawings is critical because they inform the piping fabrication and installation work. However, until recently, generating isometric drawings was a manual, cumbersome process.
“In the past, we were relying on multiple tools to design the pipework,” Mielonen said. “It was a slow process with a lot of manual stages. This meant it was error prone. We were never truly confident that the piping would work as we hoped until the actual installation. Now, we get the information we need for the isometric drawings directly from the 3DEXPERIENCE platform, which has significantly reduced the lead time for isometric drawing generation, improved accuracy and increased quality at the same time.”
Our customers come to us with a problem, but they don’t necessarily know how to solve it. Or they may have an idea that isn’t optimal. We have to be able to respond quickly with an effective approach. That means we need a way to test new ideas – and fast.
The challenge of operating with disparate solutions
Before implementing the 3DEXPERIENCE platform, Etteplan used a variety of disparate software solutions for generating isometric drawings for piping works. “Collaboration with our customers was challenging because we were uploading design files to shared servers, which were only updated once a day – generally overnight,” Saarenpää said. “That meant it was very difficult to manage changes. We didn’t know if we were working on the latest version of a design, so there wound up being a lot of inconsistencies and errors.”
Engineering effective solutions was also proving difficult. “One of our biggest clients is Valmet, a leading global developer and supplier of process technologies, automation and services for the pulp, paper and energy industries,” Mielonen said. “Together with Valmet, we design and deliver the various parts that make up paper and pulp machines in the process plant and assist with the electrics and automation. These are complex projects comprising many components – such as the drive machine, the piping works and the mill technology. Completing all stages of development – from engineering through to 3D design, simulation and validation – for these components using disparate solutions was inefficient and time consuming.”
To be sure its solutions were effective and well-planned, a pre-assembly would be carried out in a Valmet workshop before delivery of the final machine to the customer’s site. “This added weeks, sometimes months, to the process,” Mielonen said.
The process would be far more effective if all the tools Etteplan needed were available on a single platform. Also, it could improve collaboration by working in the same environment as key customers. Since Valmet was already a user of Dassault Systèmes’ 3DEXPERIENCE platform, and Etteplan was already using CATIA for design, it made sense for Etteplan to adopt the 3DEXPERIENCE platform too.
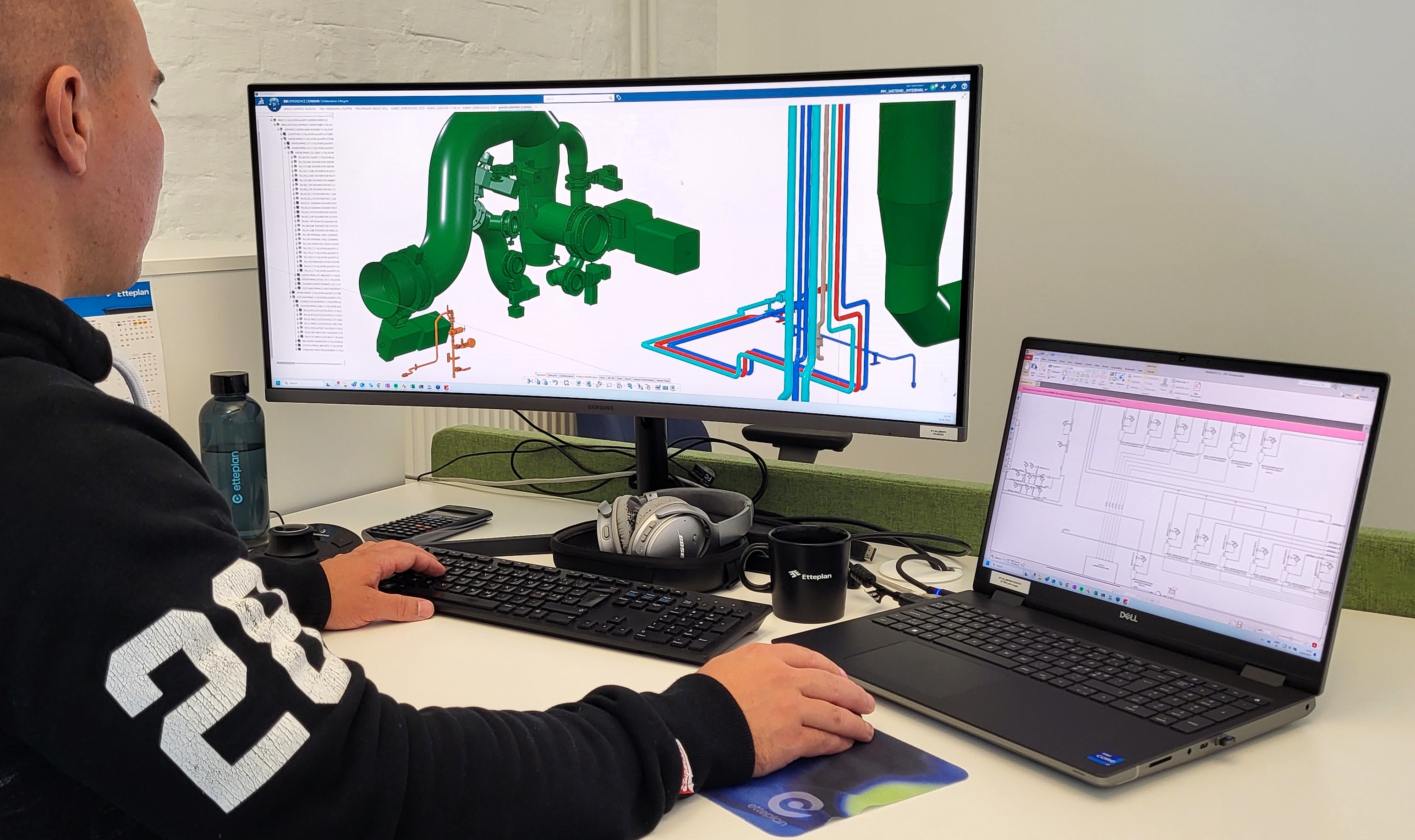
An integrated solution
Dassault Systèmes partner TECHNIA assisted with the implementation. “We have a long-standing relationship with TECHNIA,” Mielonen said. “They listened to our needs and provided all the help and support we required. As a result, the implementation went very smoothly.”
Etteplan was quickly up and running on the 3DEXPERIENCE platform, with little need for training. “Because we were already confident users of CATIA, we had no problem learning how to use the 3DEXPERIENCE platform,” Mielonen said. “It is incredibly intuitive – much easier than if we were starting out with a completely new solution.”
Today, Etteplan’s employees including its pipe engineers can work together with colleagues at Valmet in real time within the platform. “The biggest advantage of the 3DEXPERIENCE platform is undoubtedly the fact that we can work together with our customers in the same environment,” Saarenpää said. “There are thousands of us working together in the solution. The platform is very stable. Everything works smoothly and collaboration is seamless.”
With design changes updated in real time, versioning errors are a thing of the past. “Always having access to the latest files is a massive improvement on how we used to work,” Saarenpää said. “No matter whether we are working from Sweden, elsewhere across Europe, or in Asia, we can immediately see any changes that have been made.”
We are hiring a lot of new talent. Having the modern tools provided by the 3DEXPERIENCE platform, where we can work smarter together in real time with multiple parties, makes us more attractive to a new generation of employees.
Faster product development for piping systems
Etteplan can now complete all stages of product development right within the platform. “After the initial briefing from customers, we can use the platform to try out various ideas,” Saarenpää said. “We can use CATIA to create a 3D model that we can preview to the customer. We then iterate it until we get to a solution that works for everyone.”
“We can do far more development work than we have ever done in the past,” Mielonen said. “More importantly, we can do it quickly and cost-effectively.”
It’s also easy to modify existing designs. “If we have a rebuild project, for example, we can easily incorporate new parts into an existing model,” Mielonen said. “We tend to modernize a paper making line every ten years. With the 3DEXPERIENCE platform, we don’t have to start from scratch.”
“Often, what may seem like a small job at the outset ends up bigger than we anticipated,” Saarenpää said. “There might be a clearance issue, for example. In the past, we wouldn’t know this until we began the installation. Now we can see the impact right away.”
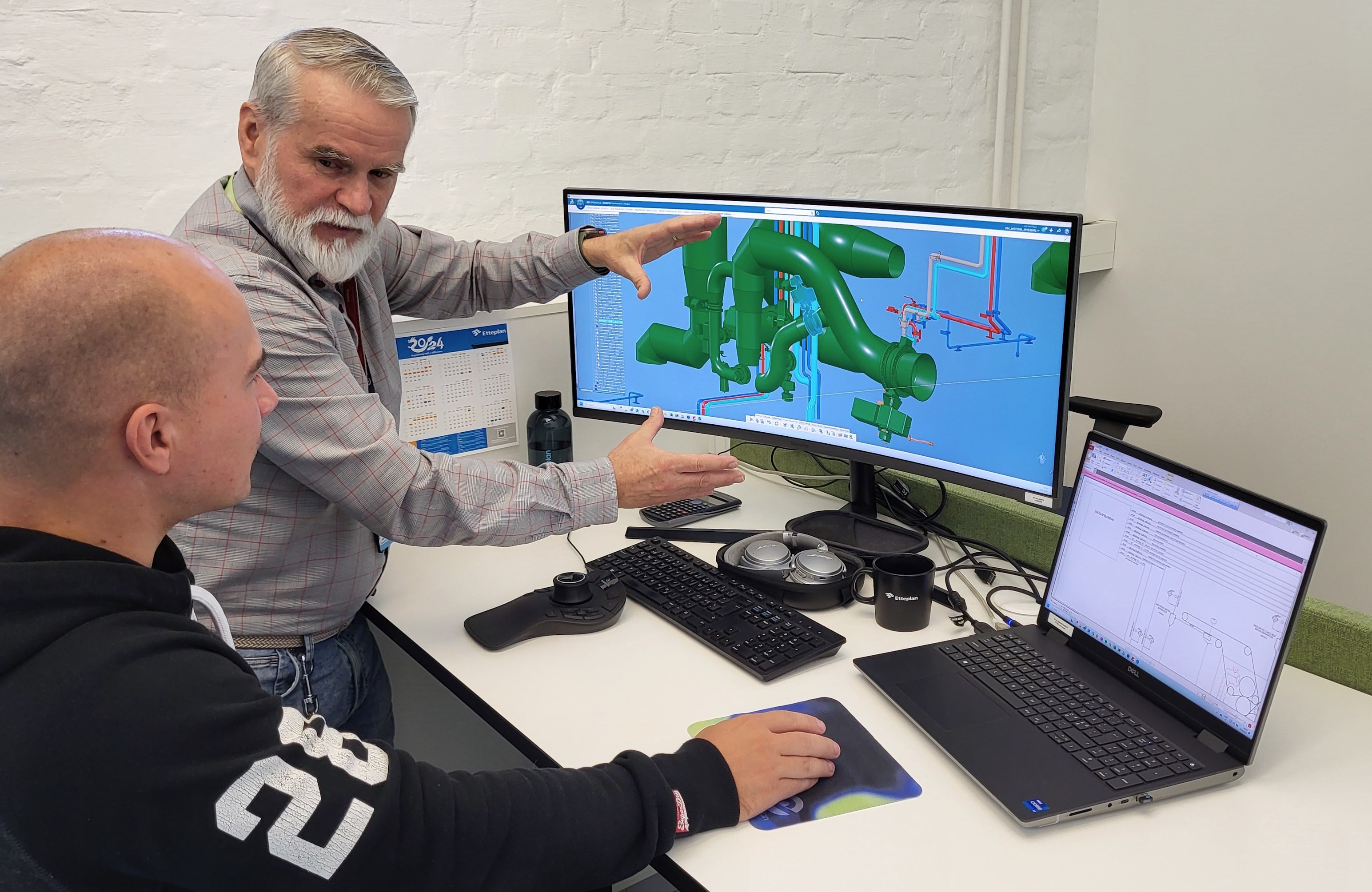
Increasing the level of automation of isometric drawings
With the product lifecycle information that is required to create isometric drawings coming directly from the 3DEXPERIENCE platform, Etteplan has been able to eliminate many manual processes. As a result, isometric drawings are created faster, and are more accurate.
“We can design piping to exact requirements, and even include all of the fittings and fixtures,” Saarenpää said.
Because the isometric drawings verify the design, the pre-assembly process is now redundant. This makes for far more efficient project schedules. “As a result, we have taken weeks off the development time,” Saarenpää said.
Once parts are ready for manufacture, assembly drawings can be sent directly from the 3DEXPERIENCE platform to the workshop. “This includes cutting drawings for plates,” Mielonen said.
“In the past, we’d send assembly drawings to the workshop, but a screw hole might have been missed, or a measurement might be slightly out. Now, we have the confidence that everything will be correct. It saves a lot of time and a lot of money. We don’t have to do everything twice.”
The biggest advantage of the 3DEXPERIENCE platform is undoubtedly the fact that we can work together with our customers in the same environment. There are thousands of us working together on the solution. The platform is very stable. Everything works smoothly and collaboration is seamless.
Preparing for an unknown future
Etteplan is now exploring how it can benefit from what the 3DEXPERIENCE platform has to offer – for example, how it might be able to automate assembly drawings in the same way that it can now automate the production of isometric drawings for piping. “We are also hoping to use the 3D models to generate a bill of materials,” Saarenpää said. “I think that will be very beneficial – it will further minimize the chance of human error.”
Mielonen believes that the platform will help Etteplan grow. “If we work faster, create better solutions and make fewer mistakes, then it will be much easier to get new customers,” he said. “But the benefits go beyond that. We have a forward focus and are constantly on the lookout for new talent. Having the modern tools provided by the 3DEXPERIENCE platform, where we can work smarter together in real time with multiple parties, makes us more attractive to a new generation of employees. This is a huge competitive differentiator and a shining example of our bold thinking mindset. It enables us to continue to move forward, even in an unknown future. That’s a big deal for us.”
Frequently asked questions
Process piping engineering is the production of the system of pipes that transport fluids including fuels, chemicals or industrial gases around an industrial facility involved in product manufacturing or power generation.
Discover more about the Digital Equipment Continuity industry solution experience.
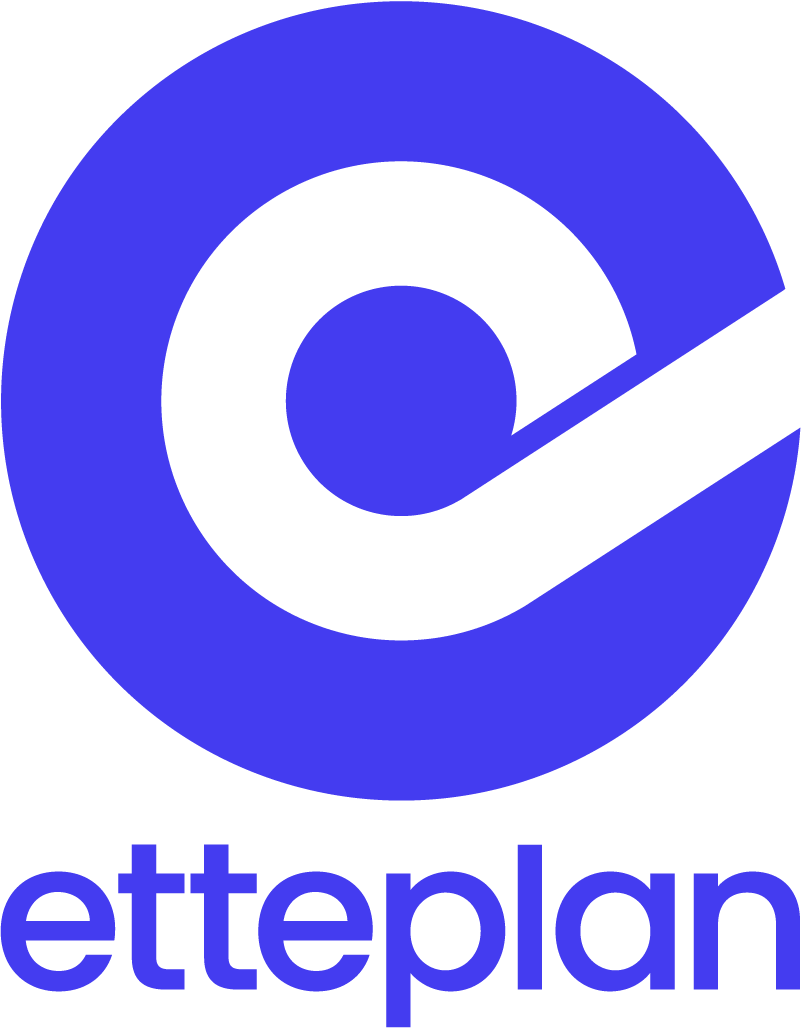
Focus on Etteplan
Etteplan is a growing technology service company with the purpose of bringing people and technologies together to change things for the better. Together with its customers, it is building a world where every system, process, and product can be made smarter, more efficient, and more sustainable. Etteplan’s customers include the world’s leading companies in the manufacturing industry. In 2023, it had a turnover of EUR 360.0 million and around 4,000 professionals in Finland, Sweden, the Netherlands, Germany, Poland, Denmark and China. Etteplan's shares are listed on Nasdaq Helsinki Ltd under the ETTE ticker.
For more information: https://etteplan.com
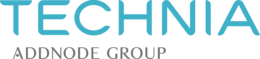
Focus on TECHNIA
By combining its customers’ strengths with its experience in product lifecycle management, TECHNIA helps turn vision into value. Its solutions are used worldwide in industries such as life sciences, automotive, travel, retail, offshore, telecom, fashion and food and beverage. It serves over 4,000 customers worldwide, including 43 that are listed on the Fortune 500.