Elidose
Planning production with DELMIA Ortems Solutions.
The interface is very easy to use. Compared to other scheduling solutions, it is easy and fast to reposition a Work Order or a group of Work Orders from one machine to another.
Elidose Overview
Elidose is specialized in contract packaging in flexible packaging. A major player in this activity for 40 years, the company relies on 2 sites and 35 production lines to serve its customers in the cosmetics (70%), food (20%) and hygiene and health (10%) sectors.
Today, it produces several hundred million sample bags per year for leading references such as L’Oréal, LVMH, Pierre Fabre, Filorga, Naos, Lactalis, Laiterie Triballat (Rians brand) ... Except for 7 or 8 product lines - mainly food - Elidose works to order.
The market in which the company is evolving is subject to a rather particular competition because of the plurality of sectors.
Jérémie Crémière, Supply Chain Director, and Cécile Boyer, Planner in the Bourgogne site in France and user of the DELMIA Ortems solution for 5 years, agreed to answer our questions.
What are the main challenges you face in your industry and your company?
“We operate in markets where responsiveness is essential. We have little visibility on customer needs. We have to deal with great instability in the arrival of components supplied by these customers, since we often receive them at the last minute. Without their raw material, we cannot fulfill the order. One of our main challenges is to be able to cope with these uncertainties and to be able to make important planning changes in the very near future."
Can you explain the manufacturing process?
“The company has two production sites, located in Nice and Bourgogne. The manufacturing process is relatively simple. The components (coils and finished product) are placed at the entrance of a machine. Once unwound, the coils will form a pouch by means of sealing systems; each of these pouches will then be filled by a dosing pump.
One of Elidose’s strengths lies in its know-how in the dosing area. The complexity lies in the ability to dose a wide variety of products (liquids, pastes, powders, etc.) which often have a very short shelf life. Production lines must be flexible.
The notion of machine adjustment is therefore very important: each request is highly personalized (whether in terms of shape, composition, or the size of the bags required to the millimeter).“
Why did you have to conduct a planning project? Was it in parallel or after the ERP?
“At the time, we wanted to have a 4 to 8 week planning solution that could easily interface with our ERP, that could be accessed by multiple people in consultation and in operation, and that could easily recalculate and update itself according to contingencies.
The solution also needed to:
• Establish a load plan for our machines as well as the need for personnel over the coming weeks
• Plan and smooth the load according to the number of people present
• Transfer a WO group from one machine to another
• Quickly visualize the stick break point corresponding to a production
• Optimize our format changes."
What are the strong points of the DELMIA Ortems solution for you?
“The interface is very easy to use. Compared to other scheduling solutions, it is easy and fast to reposition a Work Order or a group of WO’s from one machine to another.
With Elidose, the scheduling horizon is defined one month in advance but the schedule is readjusted/optimized every day. DELMIA Ortems lends itself really well to the exercise of daily updating without it being painful; you can easily shift the schedule or swap two WO. Everything is fluid and transparent.
Elidose’s production sites generally operate on a 2×8 basis. During peaks of activity which appear in a somewhat erratic way, it can happen that a night shift is set up in the space of a week. We work with an infinite number of employees (in partnership with temporary employment agencies). This increase in production capacity is managed on DELMIA Ortems.
We appreciate the management of user rights that accompanies the rapid updating of the schedule it’s easy to add someone on the planning.
Finally, the visual aspect of the solution is also very important, especially for people from outside the department who come to consult the schedules (Sales for example).”
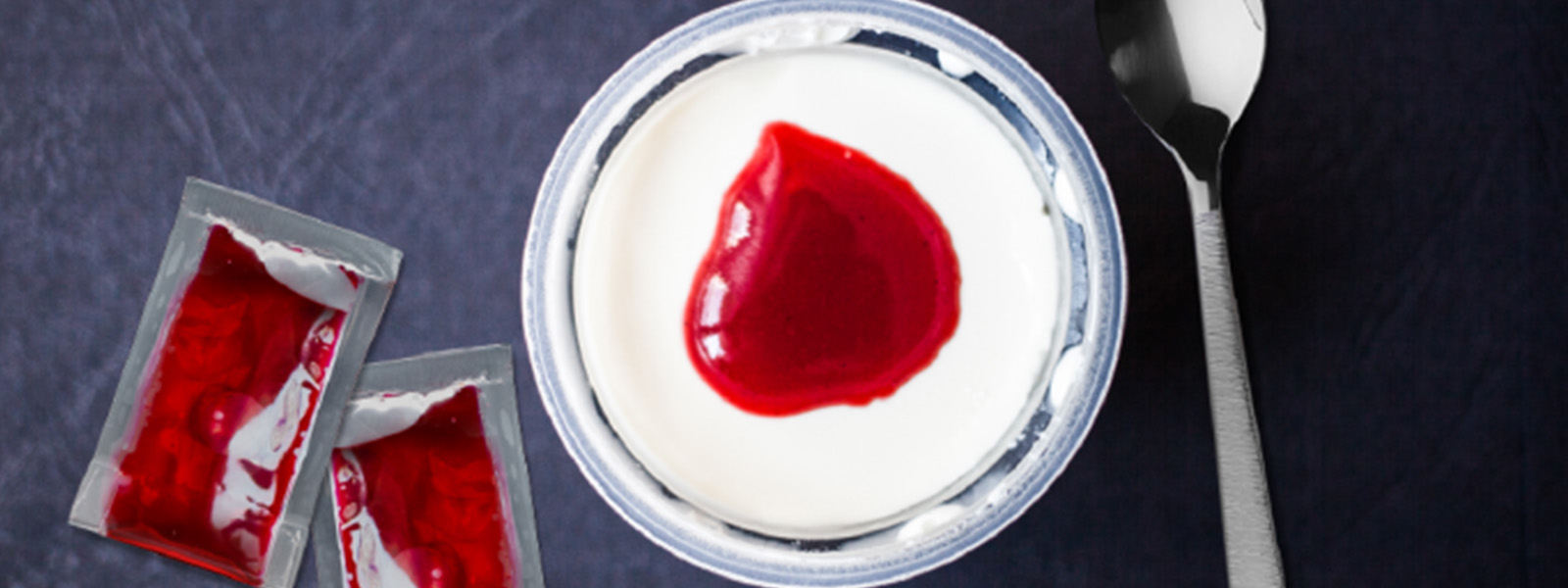
What benefits have you seen with the solution?
“We have a real interest in working with DELMIA Ortems since our planning is extremely fluid and at very short notice. As we mentioned earlier, our customers are the ones who provide the products for packaging; they are our suppliers.
DELMIA Ortems has provided us with a planning tool that is very flexible and communicates well with the ERP. This allows us to integrate our planning and requirements calculation processes into stable and efficient software packages.
The solution also allows us to anticipate a certain seasonality depending on the products and the use of temporary staff which can reach 40%. We have gained in processing time and in communication on the planning.
It also provides a support that allows us to more easily perpetuate the necessary planning knowledge and thus allows other technicians to be able to intervene on the planning. The planning rules can be understood and there are a certain number of constraints that can be imposed on the machines. It is relatively easy today to train a new planner, for example, in anticipation of vacations, which was very complicated before. So we’re capitalizing on the planning information in the solution.”
What about the optimization of format changes?
“The information that comes down from the ERP into DELMIA Ortems and that reappears in the tool allows us to have a more global vision. We have the ability to better optimize production and format changes than we did before the solution was deployed.
“I couldn’t work with spreadsheet file because each modification takes a lot of time and is manual, whereas with DELMIA Ortems, everything falls into place in a few seconds,” says Cécile Boyer.
What developments would you like to see in this project?
“Following the upgrade of our ERP, we are considering deepening the communication between the two tools in order to save data entry time.
Today, we have an interface between the ERP and DELMIA Ortems that is only top-down. Our ambition would be to activate the feedback of information from DELMIA Ortems to the ERP (especially the start and end dates of WOs) so that the calculation of needs in our ERP is based on these dates.
In addition, we would like to resume training to go further in the use of the solution’s functionalities, in particular to be able to carry out scheduling simulations."
Finally, how did DELMIA Ortems and Visiativ support the project?
The project was deployed by the DELMIA Ortems teams and Visiativ took care of the support.
“Visiativ was always available to answer our questions and guide us towards solutions adapted to our needs and our size (SME). The consultants are available and intervene quickly in case of problems.”
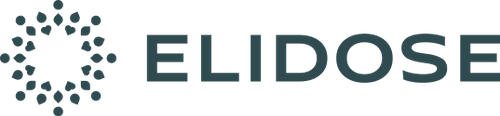
Focus on Elidose
A specialist in flexible packaging packaging solutions, Elidose produces nearly 750 million sachets each year, mainly containing cosmetic products such as skincare, makeup, perfume and hair products.
Elidose has two production sites: one in Bourgogne-Franche-Comté the other in the Provence-Alpes-Côte d’Azur region. Headed by a central team, they allow for an agile response to all projects.
- 5400 m2 of production space
- 4 dedicated workshops & 10 independent production cells
- 40 machines
- 150 employees
For more information: www.elidose.com
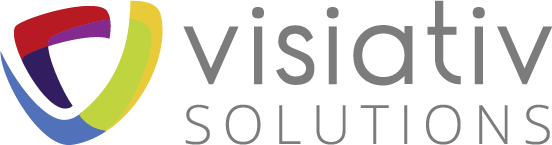
Focus on Visiativ
As a subsidiary of Visiativ Group and with 25 years of customer experience, Visiativ Solutions has positioned itself as a global platforms designer to shorten time-to-market for its customers thanks to Dassault Systèmes PLM and Visiativ technologies.
Visiativ Solutions enables industrial companies to drive innovation, increase efficiency, reduce costs and improve quality through integration and resourceful utilization of innovative solutions.
For more information: https://www.visiativ.com