CoorsTek
US-based technical ceramics manufacturer CoorsTek selected the Ready to Make industry solution experience on Dassault Systèmes’ 3DEXPERIENCE platform, including ENOVIA for collaboration, document management and quality process management and DELMIA Apriso Manufacturing Operations Management Suite to improve manufacturing efficiency, productivity quality and maintenance operations.
Engineering ceramics to outperform metals
For over 100 years, Colorado-based technical ceramics manufacturer CoorsTek has continued to be at the forefront of developing advanced ceramic materials to meet the world’s most perplexing engineering and manufacturing challenges. Ceramics are engineered to be as strong as metals, and outperform them in many mechanically demanding applications.
“We like to say that ceramics are the last resort material,” said Matt Mehlbrech, CoorsTek’s vice president of information technology. “You'd probably use a metal or a plastic if you could because they are cheaper, but they can't perform the way ceramics can.”
“Design engineers are constantly looking for ways to improve performance in systems where strength, extreme temperatures, electrical insulation, chemical resistance and other demands are persistent factors,” said Brian Frimel, CoorsTek’s senior director of IT. “This is where technical ceramics come into their own.”
The company’s solutions are used across a wide range of industries and applications, from fuel injection technology for automotive firms to jet propulsion systems for aerospace companies. The unique attributes of ceramics make CoorsTek’s team incredibly passionate about its products.
“CoorsTek's vision statement is ‘we make the world measurably better,’ and we believe in that through and through,” Mehlbrech said.
Complex products result in complex operations
Due to high demand of its products, CoorsTek grew rapidly into a multinational organization employing over 6,000 employees across 27 manufacturing facilities spread primarily across the US, Europe and Asia – producing over 400 advanced ceramic formulations.
“It’s a complex operation,” Frimel said. “When you make precision ceramics, you form the ceramic in a specific way such as via pressing or a slurry, you then fire that through a kiln, and then you finish it through either a grinding or CNC operation. It’s an incredibly asset-intensive organization.”
In fact, CoorsTek runs over 10,000 pieces of equipment within its global operation. The equipment uptime is critical to on-time delivery, and it needs to perform in a fast-paced production environment.
“We have high demands from our customers when it comes to lead times, and we need to be able to react very quickly,” Mehlbrech said. “Making sure that our operations are efficient so we can get the product out the door on time is very critical to our success with our customers.”
We needed a solution that is easily trainable, repeatable, and consistent – and we get that with DELMIA Apriso.
Performance also is imperative. “Our customers demand high quality,” Mehlbrech said. “They choose technical ceramics because they need specific material properties. So quality is exceptionally important for us.”
This requires CoorsTek to guarantee a high level of predictability for its output. “When we’re trying to make a product, we might say, ‘Okay, we’re going to make a hundred,’” Mehlbrech said. “And based on the processes that our materials have to go through, we might produce 90, or we might produce 110. For us, the goal is to hit a hundred every single time.”
Due to this growing pressure to run its operations more efficiently, effectively and predictably, CoorsTek chose the Ready to Make industry solution experience on Dassault Systèmes’ 3DEXPERIENCE® platform, including ENOVIA and DELMIA Apriso Manufacturing Operations Management Suite.
“The solution is helping us make sure that we’re hitting those marks for our customers,” Mehlbrech said. “We also saw how it can drive productivity. We really wanted to simplify the user interface for our shop-floor workers since we have a lot of new staff. We needed a solution that is easily trainable, repeatable, and consistent – and we get that with DELMIA Apriso.”
Delivering enterprise-wide benefits
CoorsTek is experiencing real change with DELMIA Apriso due to its enhanced visibility of the shop-floor operations.
“We can now maintain our factories in a way that we’ve never been able to before, thanks to our new preventative maintenance capabilities,” Mehlbrech said. “That’s setting the stage for us to do more prescriptive planning of what we need to do in our operations. We can see what’s happening on the shop floor in real time, so we can proactively react before there’s a need for maintenance, thereby avoiding unplanned and long downtime. With the data we now have at our fingertips, we can accelerate the modernization of our business.”
For example, Coorstek uses DELMIA Apriso to execute its inline inspection processes to identify any quality issues before products are shipped. “So when work orders are flowing through our factory and they get to an inspection step, the product has to pass that step before moving forward,” Mehlbrech said. “We have minimized quality escapes, and we’ve seen direct reductions in our scrap too.”
Because of the fragility of the ceramic-making process, scrap is inevitable. “However, by understanding why scrap was produced, and by having common scrap codes within the system, we can better analyze and improve specific areas where we’re producing scrap in the operation,” Frimel said.
Making decisions with fact-based information is a game-changer, according to Bob Sendek, director of ERP program management. “Instead of having to hunt around on the shop floor for work orders, or determine job status, sales people simply go into DELMIA Apriso and everything is there,” he said. “The ability to access that information visually and quickly is priceless.”
Life is much easier for shop-floor workers too. “In DELMIA Apriso, they can go to their work center, find their work order and then find everything they need to plan their day,” Sendek said. “They can find which machine they have been allocated to, what quality checks are required, and more. They can even submit reports right within the solution. Overall, DELMIA Apriso has removed all of the complexity from the shop floor.”
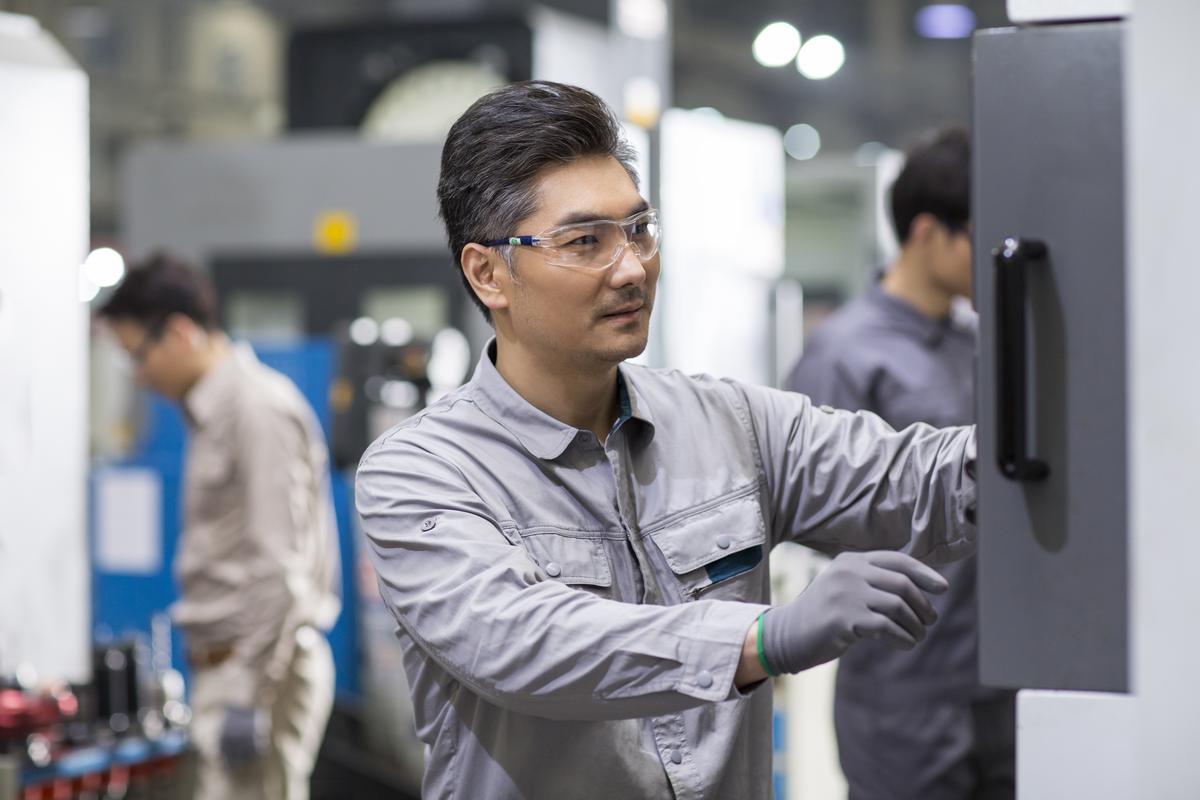
Better document management
With ENOVIA on the 3DEXPERIENCE platform, stakeholder engagement and decision-making has improved at CoorsTek through better document management. For example, common quality procedures and work instructions within ENOVIA help CoorsTek meet regulatory requirements such as ISO and stringent aerospace requirements.
“We always have the latest iteration of a document available to all members of the CoorsTek team,” Frimel said. “This helps us consistently produce a quality product.”
The corrective action preventive action (CAPA) portion of the solution also helps with nonconformance reporting. “Today, nonconformance reporting is completed through DELMIA Apriso,” Frimel said. “It’s integrated with the work order so that an operator can input a nonconformance if there’s a problem on the shop floor. And if that needs to get escalated to a CAPA, it is interfaced to ENOVIA so that the quality team can review it easily.”
For Sendek, the 3DEXPERIENCE implementation has made a positive impact on the company. “It’s actually delivered a real ‘wow’ factor,” he said. “So as the [shop-floor operator] looks at a work center or an operation, they see what documents are associated with a part, with a work center or department, and they click on a link, pull in that document from ENOVIA, and see everything they need on the screen.”
This process eliminated the need for paper. “We’ve removed stacks of binders from the shop floor,” Sendek said. “We no longer need to worry if we are working on the latest revision, as that’s what is always presented to the user. It’s really transformed things for us.”
Additionally, better document management positively impacts quality at CoorsTek. “Shop-floor users can go into ENOVIA and record quality information at the point of use,” Sendek said. “They’re able to record critical parameters, which we can run different types of checks against to ensure a product is within its process capability. I think integrating quality into the shop floor in this way has been one of the biggest benefits we’ve seen from the implementation.”
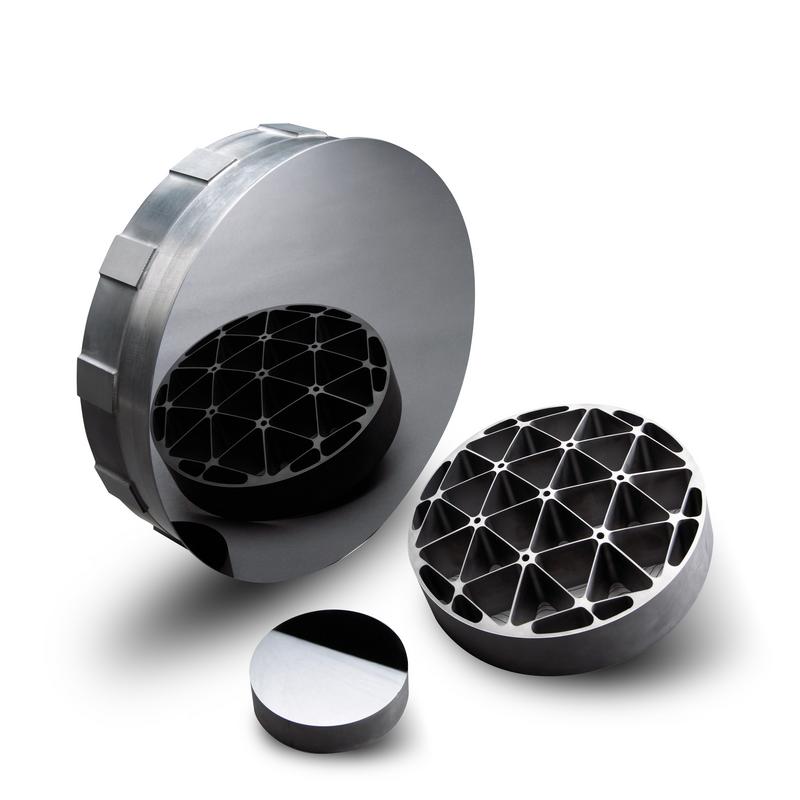
A foundation for solid growth
Overall, Mehlbrech believes the implementation of the 3DEXPERIENCE platform with DELMIA Apriso provides a solid foundation that will help the company to accelerate its growth. And in many ways, DELMIA Apriso is extending the effective life of CoorsTek’s ERP solution.
“We were fortunate to win another CIO 100 Award this year, and that was due to our orchestration of different systems that come together to modernize our shop floor,” he said. “And this orchestration we believe is fairly unique. It gives us a lot of flexibility in what we can do with other systems such as the ERP going forward. It's a huge advantage, not just in how we execute our day-to-day manufacturing, but from an IT point of view.”
As a result of this success, Frimel wouldn’t hesitate to recommend the 3DEXPERIENCE platform with DELMIA Apriso to other companies. However, he does offer a word of advice. “It’s important to truly understand the functionality of the DELMIA Apriso solution and how it will work within your organization,” Frimel said. “Think about configuring the front end to look and behave in a way that will work for you. Additionally, having a strong interface capability in DELMIA Apriso ensures timely updates and consistency in the ERP.”
Sendek also shares his recommendations for customers looking to implement these solutions. “Take the time to look at your processes,” he said. “And don’t try to force a pre-packaged capability out to your factories. Also, it’s very important to pay attention to your data. Everything’s going to be data-based. So if your data isn’t clean, it’s hard to roll this out.”
With its DELMIA Apriso and 3DEXPERIENCE platform implementation, CoorsTek is well positioned for future growth. “In the long-term, we want to continue to develop, grow and modernize our factories to be more flexible, be more dynamic, and have a better use of data,” Melbrech said. “We want to use the 3DEXPERIENCE platform to simulate, predict and prescribe what we need to do on the shop floor and allow us to be more nimble than we’ve ever been before.”
00:00 – 00:49
Matt Mehlbrech, VP of Information Technology, CoorsTek:
CoorsTek products are virtually everywhere. They're in electrical vehicles in every piece of computer equipment that you use every single day, they're in implantables in people's bodies, they're on the international space station. Mostly anything you've touched in the last couple of days has had products associated with Coorstek in it. CoorsTek is a global manufacturer in technical ceramics. Technical ceramics are material sets used when a particular application has really specific, consistent needs for performance. That might be temperature resistance, or chemical resistance, or strength. A couple of consistent things that we see from our customers is they demand high quality and delivery. So we need to react very quickly. And so making sure that our operations can operate effectively and get product out the door is really critical to the success with our customer.
00:50 – 01:03
Brian Frimel, Senior Director of IT, CoorsTek:
CoorsTek is an asset intensive organization. We have over 10,000 pieces of equipment within our global operation things such as presses, kilns and CNC equipment. And the uptime of that equipment is critical to our on-time delivery.
01:04 – 01:26
Matt Mehlbrech:
One of the ways that we're addressing that is with the help of Dassault Systèmes products. For example, we use DELMIA Apriso to execute our inline inspection process. So when work orders are flowing through our factory and they get to an inspection step, the product has to pass that inspection step before it can move forward. We're directly seeing reductions in quality spills with our customers a result of deploying these tools.
01:27 – 01:40
Brian Frimel:
We have seen an improvement of productivity specifically around the tracking of scrap. Understanding why that scrap was produced, having common scrap codes within the system allows us to better analyze and improve specific areas where we're producing scrap in the operation.
01:41 – 01:57
Matt Mehlbrech:
We were fortunate enough to win another CIO 100 award this year and it was really based on our orchestration of different systems that come together to really modernize our shop floor, giving us real-time visibility into what's going on and really foundationally, how we execute our work orders on the shop floor.
01:58 – 02:15
Brian Frimel:
So the 3DEXPERIENCE platform is going to be a major part of our manufacturing IT strategy. From engineering and product development, through the manufacturing and understanding simulations of future plants, and the execution on the shop floor with DELMIA Apriso, all those components are going to play very well together.
02:16 – 02:40
Matt Mehlbrech:
We want to continue to develop, grow and modernize our factories to be more flexible, be more dynamic, and the use of the data that we now are getting out of our model plant initiative and the 3DEXPERIENCE puts us in a position where we can simulate, predict and prescribe what we need to do on the shop floor. And allow us to be more nimble and start planning in a different way than what we've ever been able to do before.
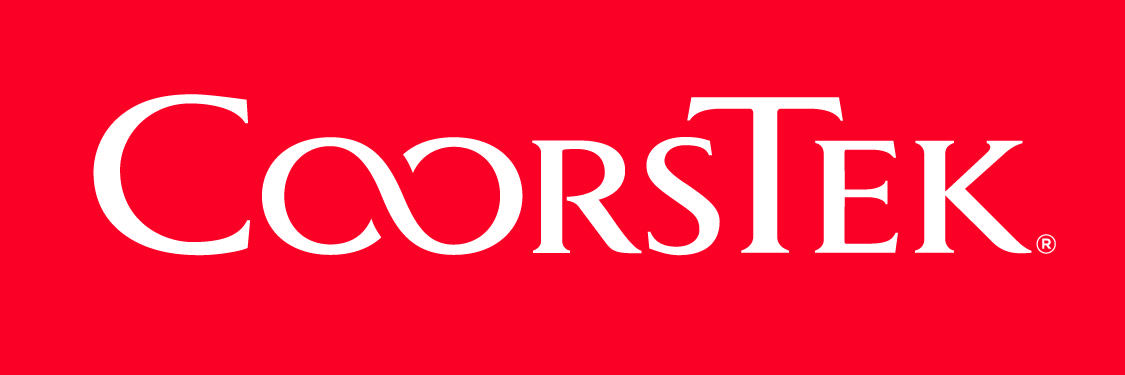
Focus on CoorsTek
CoorsTek is a 110-year-old materials science company that develops proprietary technical ceramic material formulations. With manufacturing, sales, and research facilities around the world, it serves a wide variety of essential industries by creating new materials and technologies to meet the most demanding component needs and challenges. CoorsTek’s success is achieved by closely collaborating with customers on component design and material selection for the most efficient manufacturing process to achieve their business goals. Today the company is led by the fifth generation of Coors family members.