COMEZ INTERNATIONAL
COMEZ INTERNATIONAL S.R.L, a member of Jakob Müller Group, a world leader of narrow fabric machinery, had to meet the needs of its high-end customers by ensuring high quality and on time delivery of make to order machines.
During the COVID-19 pandemic, we had an unexpected and extremely important need: to double production for our machines for making masks. We had to quickly convert our production equipment to produce double the quantity in a very short amount of time. Without DELMIA Ortems, this planning would not have been possible
World leader in machine processing solutions
The market is more and more demanding and competitive in terms of time and costs and COMEZ INTERNATIONAL S.R.L., a company operating in the industry of machine technology for narrow fabrics production and with tens of thousands of installations all over the world, knows it well. In the constant competition with companies that play on price by offering machines for simple fabrics with a lower technological standard, it is not always easy to excel. However, COMEZ maintains its industry leadership with its strong focus on customer satisfaction and product quality. Competitively, dependability and efficiency are the objectives that COMEZ strives to achieve every day, based on its constant attention to technological innovation and application development.
Established in 1953, COMEZ has become a world leader with its crochet and warp knitting machines, used for the production of a wide range of narrow fabrics (lace, ribbons, bands), technical textiles, trimmings, fancy yarns and clothing fabrics. In October 2012 the company joined Jakob Müller AG Frick and has been operating under the name “COMEZ INTERNATIONAL S.R.L.” ever since. 90% of its turnover derives from export sales. Comez currently employs 80 people.
Challenges
COMEZ INTERNATIONAL S.R.L., world leader in the technology of narrow fabric machinery, had to meet the needs of its high-end customers by ensuring high quality and on time delivery of tailor-made machines.
Solution
The Italian manufacturing company employs Dassault Systèmes’ DELMIA Ortems solution as an operational flywheel to improve production effectiveness and efficiency.
Advantages
DELMIA Ortems enables measurability, predictability and continuity of production processes. Thanks to real-time data updates, COMEZ INTERNATIONAL can quickly make decisions regarding the allocation and distribution of resources to fulfill orders, but above all, meet deadlines and product lead times.
The steps toward digital planning
COMEZ’s motivation for technological change and the adoption of DELMIA Ortems for business continuity and sustainability arose several years ago, although it took some time to achieve substantial change.
In 2013, Comez decided to implement a commonly used commercial product for process planning, a simple Excel spreadsheet, initially comprising a few hundred lines and a few formulas. In 2018, it turned into a 30-page spreadsheet made up of thousands of lines with hundreds of formulas. The file included all COMEZ production elements - machine tools, work orders divided in cycles with times and setup and working hours. This data - divided by the 22 operators – was subsequently merged into a single file to have a global view of the production process. “The various steps with all the operators were marked in the file, with the working time and the return dates of the finished piece; we were doing 40/50 orders per day, with five or six daily phases”, but, as Flavio Biscaldi, Planning Manager of COMEZ says, “when I gave the answer on the date, by then the order was already out of time. For example, it took me a week to schedule a two-week job. We work on the short term, so we cannot waste days and days of production”. Due to a lack of scheduling software most of the day was spent trying to plan and define times and resources. “We needed to provide dates to customers as regarding their deliveries” - says Flavio Biscaldi. As COMEZ does not manufacture standard machines, each request is managed individually – we need to define the times and the necessary steps between the technical department and the production department. In the past, we used systems on which we worked for many hours. It was not possible to ensure the achievement of the KPIs required by the customer and the company”.
With the implementation of DELMIA Ortems, however, Flavio Biscaldi’s daily routine has changed: “Thanks to DELMIA Ortems, updating the planning takes only two hours a day compared to the six hours I previously spent. This change improves not only my working life, but also the attitude inside the production department: times are predictable and we can communicate the delivery date to the customer the day after we receive the order. The manufacturing process is now measurable, taking into account downtimes, emergencies, service network, spare parts and machining processes for our parent company. Gathering all this information in an Excel file had become very difficult. Now it isn’t anymore”. How was this choice made? “When we reached the limit of the Excel file capabilities - says Biscaldi - COMEZ decided to get help from experts in the field, in particular from Turin-based SORMA, which deals with management systems for manufacturing companies.
SORMA followed us step by step, listened to all our needs and created a tailor-made DELMIA Ortems solution for COMEZ. Training lasted for one month and, at some point, after a parallel processing, the Excel file was turned off. Transition was natural and guaranteed the continuity of our business. The goal achieved was a new start for COMEZ: “This is where the new way of managing production was born, with the help of the DELMIA Ortems scheduler, which is obviously tailored to our production needs. In my opinion, we managed to achieve excellent results. First of all, with the Excel file, data was entered manually. It took hours just to enter and analyze it and when the results came, they were rough and it was too late. In addition, it was difficult to predict obstacles and plan times. It was always too late to remedy and act on time.”
Data is the litmus test of the turning point in the company: in 2019, COMEX documented a total of 202 hours dedicated to data entry in Excel files. After DELMIA Ortems, a total of 82 hours were clocked for the same orders, a net time saving of 59.43%.
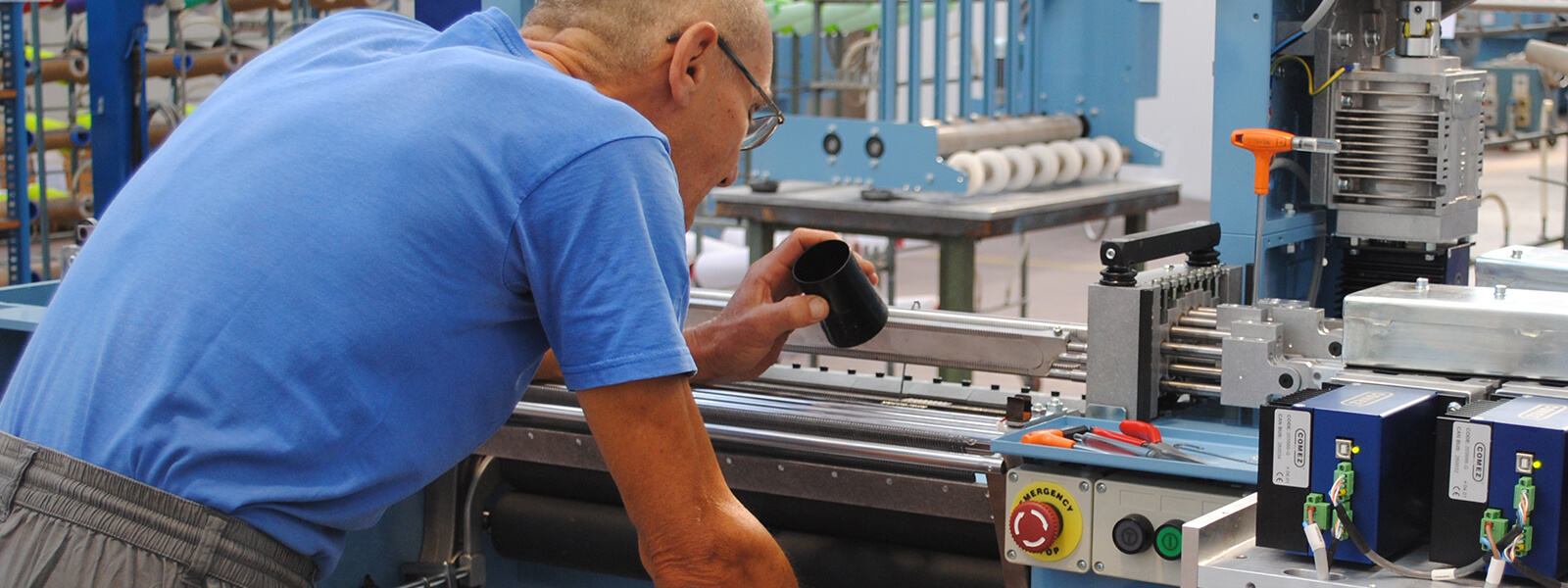
Perfect synchronization of data and timing
The introduction of the DELMIA Ortems scheduler, which has changed the way work is done, was therefore a clear benefit from the outset. “First of all, the reliability of the system is important: it does not stop or freeze” says Biscaldi. “Then the speed of production changes: we are very fast and reactive. We have long-term visibility of orders, being a very modular system. If we have a person who gets sick, in a few minutes I can move the workload to another operator and reschedule everything”.
Numbers speak for themselves: 30% reduction in forecast errors, 8% increase in production, 27% reduction in production delays, 20% reduction in setup times.
Targeted and quality investments
“In the production department it is important that processing and method are aligned, both for customers and suppliers. From one serial number to another, customer changes drive, part changes and this must be kept under control”. Biscaldi underlines another key benefit for the company’s growth achieved thanks to DELMIA Ortems: “We needed a scalable, but tailor-made production process. Having already a management system in place, we decided to use a single working environment to speed up and improve the alignment between the production and technical departments”.
The key factors that influenced the evaluation process were modularity, flexibility and the top-level potential. “Every company is unique - says Biscaldi - every company has its own needs. Moreover, the systems previously adopted had too long and demanding times and were not effective for the planning and management of emergencies, a fundamental aspect for COMEZ to ensure accuracy”.
The possibility to analyze data proved to be crucial also during the renewal of the machine fleet: “Last year we purchased a new numerical control machine for our workshop department - says Biscaldi. Before the purchase, we made an analysis on all the results of the new potential machine, how it could be used, for how many hours it would be used. Once the investment was made, we can say today that it was a profitable, conscious purchase. We have prepared new scenarios to define whether and when it is worth investing and the impact that each investment can have on our business. For each purchase, even of only 100,000 euros, you can make a cost-benefit evaluation. And even within the company, a targeted and successful purchase gives credibility to future investment forecasts”.
Another key aspect is the easier management of stocks and orders: thanks to accurate planning by our employees, machine by machine, it is easier to understand the production status and decide if it is possible to keep some orders in-house or if it is necessary to turn to third party suppliers. In addition, scheduling in advance helps to avoid unforeseen events and uncertainties. The way of working has not changed but has been optimized: repetitions or wasted time are avoided. “The advantage - says Biscaldi - is above all for our workshop manager, who has essential information, while, for the operators, the new way of working is important because they see what they are doing and can estimate their times”. This is achievable thanks to the 11 PC tablets the employees utilize from shift to shift.
- 30% reduction in forecast errors
- 8% increase in production
- 27% reduction in production delays
- 20% reduction in setup times
Future possibilities of implementation
The results that COMEZ had set itself were achieved, now it is possible to look even further: “We are currently using DELMIA Ortems 100%. The next steps could be to integrate some other departments within the solution, such as assembly, or to connect the machines directly to DELMIA Ortems.”
COMEZ has managed to increase its competitiveness - and this was its main challenge and objective - through a single tool that aligns processes and scheduler and allows for greater management capacity by fostering strategic collaboration. In a year, the way of working, productivity, visibility and agility have changed. The accuracy of forecasts has improved and the level of service has been maximized.
Today, production problems are displayed in advance through advanced simulations that take into account factory, suppliers and customers constraints. Reactivity to the unexpected has increased. Optimized production sequences can be created taking into account production constraints and criteria, which can be modified at any time, such as plants, equipment and raw materials. This increases production efficiency and reduces setup and lead time. For COMEZ, Biscaldi expresses full satisfaction: “We are at the beginning of 2020 and, after about one year of using DELMIA Ortems, we can say that we have improved a lot in the production organization. Now we have access to previously unknown or, at least, unclear information, such as the global view of the production in the workshop, the lead time (workflow) for each single work order, the waiting time for an order from its launch to the actual production and the workload of each single machine tool”. It is thanks to this starting point that COMEZ and its planning manager Flavio Biscaldi are eager to take up the challenges of the future: “We can still increase reliability and efficiency; in the meantime, I have saved 6 hours a day”.

Focus on COMEZ INTERNATIONAL
World leader in the technology of narrow fabric machines
Revenue: € 12 million (2018)
Headquarters: Cilavegna (PV), Italia
For more information: www.comez.com