CAREL INDUSTRIES
Italian company CAREL specializes in electronic control solutions for air conditioning, refrigeration and heating systems and uses the 3DEXPERIENCE platform on the cloud for its development processes. By adopting the Digital Equipment Continuity industry solution experience, CAREL is able to connect all disciplines and systems, which shortens configuration and production time, reduces errors and offers more customization options.
Smart and customizable electronic control solutions
The days of one-size-fits-all mass production are giving way to a new era of customization. In the same way that consumers now expect products tailored to their distinctive tastes and preferences, industrial companies also demand new levels of choice from their suppliers. In the commercial refrigeration market, original equipment manufacturers (OEMs) increasingly demand electronic controls and displays to better regulate temperatures and optimize energy usage in the refrigerators, freezers and wine coolers that they make. They also need them to be customizable so that they blend into their products seamlessly, tailoring everything from the color and size of displays and cases down to creating unique icons and buttons.
Suppliers like Italian company CAREL – which specializes in control solutions for air conditioning, refrigeration and heating – understand the importance and growing value of customization. To this end, CAREL has developed a new range of configurable smart thermostats. The new iJ solution is one of the company’s most customizable range of products and combines the latest energy management and smart connectivity features. It was also the first to be developed in an entirely new way, embracing the latest collaborative engineering and configuration management capabilities on the 3DEXPERIENCE platform on the cloud to accelerate time to market.
“The iJ thermostat for refrigeration units is a highly configurable product, serving the needs of many different customers in terms of its power supply, display, connector and packaging options,” said Luca Toffanin, group product platform manager and PLM manager at CAREL. “Customization was key, but we knew that our configuration approach was too slow. Before, we used spreadsheets to configure each product, taking us around 100 days to get it designed, made and out in the field. We had to be much faster. With the 3DEXPERIENCE platform, we successfully reduced the development cycle from 100 days to just 10 days.”
Transforming a product's entire development cycle
When most companies implement the 3DEXPERIENCE platform on the cloud, they begin by transforming their design and engineering processes. CAREL took a different approach. It decided to change the entire development cycle for a single product line to achieve fast and meaningful results. The initial goal was to master variance management and release a highly configurable product in record time.
“We want to achieve digital continuity across the value chain, from the voice of our customers to production, and eventually the field,” Toffanin said. “With our customers’ needs in mind, we began by accelerating product variance generation. We didn’t want to waste time moving all our old data. Instead, the idea was to focus on new products and connect all related development processes in the 3DEXPERIENCE platform.”
Accelerating the configuration stage to such an extent was down to CAREL’s ability to break down data silos between design, engineering and manufacturing, and connect its processes. Today, the company feeds its manufacturing execution system (MES), enterprise resource planning and supervisory control and data acquisition systems with information from a single, centralized data model managed and updated in the 3DEXPERIENCE platform.
“Being able to centrally manage our data in the platform allows us to industrialize a new product very quickly,” Toffanin said. “Handling all processes via the 3DEXPERIENCE platform means that everything is clear and connected, and information flows between systems. When you need to package the product in a specific way, you immediately have the correct bill of materials and bill of processes – everything is aligned.”
- From 100 to 10 days
SHORTENED DEVELOPMENT CYCLE
Mastering complexity and scalability
CAREL’s OEM customers choose to work with the company for its expertise in delivering a comprehensive, end-to-end offering of well-integrated solutions and services that bring energy savings and reduce the environmental impact of their commercial refrigeration products. Over time, CAREL has had to tackle increasing complexity, both in terms of the control solutions it develops and across the business as the scale of its organization expands – both organically and through acquisitions. Today, the company has 38 subsidiaries and runs 15 production plants worldwide. CAREL is keen to retain full control and visibility across its value chain so it can deliver the same levels of quality and service its customers expect.
The company already uses the Dassault Systèmes solutions DELMIA Apriso for MES and SOLIDWORKS for the design of plastics and mechanical components. When its technology partner Hermes Reply suggested the 3DEXPERIENCE platform on the cloud as its centralized product development environment, it was a natural choice.
“During the software selection, we really valued the strong integration the 3DEXPERIENCE platform could help us achieve between engineering and manufacturing,” Toffanin said. “It aligns with our vision to have everything in one place within an integrated data model so we can operate in a simpler and leaner manner. For us, the 3DEXPERIENCE is a business enabler for boosting innovation through better knowledge management and accelerating time to market by reducing the time between different development stages, so we can keep up with the latest technological trends and growing need to protect our planet.”
CAREL opted for the cloud-based version of the platform so it could easily connect its geographically dispersed subsidiaries and plants and add new functionality and features according to its evolving needs. As it brings new disciplines, offices and locations onboard, it simply adds new licenses to its package to fit requirements. The company also values the cloud’s out of the box functionality and availability, without the need for a lengthy implementation process. Throughout its digital transformation journey, CAREL is confident it can rely on Dassault Systèmes, Hermes Reply and its SOLIDWORKS partner Nuovamacut to guide it in the right direction.
“Hermes Reply was instrumental in our decision to implement the 3DEXPERIENCE platform,” Toffanin said. “It’s essential to have reliable partners who can bring their technical expertise and experience to ensure the success of the project. Our teams are collaborating effectively, and all companies are aligned on our long-term targets.”
The 3DEXPERIENCE platform can contribute to our environmental, social and governance targets by making our design and industrial processes even more efficient by reducing material waste in production, improving remote collaboration to lessen the need for travel, and supporting us to develop smart, sustainable products.
Single source of truth reduces errors
Today, CAREL can efficiently manage all product variances for its iJ control solution within the 3DEXPERIENCE platform on the cloud. Project stakeholders have access to up-to-date information and can communicate changes quickly and effectively on the platform. This speeds up design and saves CAREL significant time at the testing and verification stage – a process that previously took up to 30 days, involving the production of at least two physical prototypes.
“We now have a product structure in the platform where you can clearly see what the options are, the rules between the variants, how the different components work together and whether a particular combination is possible or not,” Toffanin said. “We select within boundaries and verify everything virtually. Before, we didn’t have a way of testing a product variant worked until we made it. And this single source of truth based on aligned processes significantly reduces the risk of errors.”
Customer satisfaction is improving, too. OEMs no longer need to check multiple samples, or risk receiving products that don’t carry the features they wanted.
“We are also able to expand our offering as we no longer need to limit the options available to our customers,” Toffanin said. “We can master all that complexity in the background. Eventually, we hope to give our commercial subsidiaries access to a true virtual representation of each product – a virtual twin – that follows the development of each product from design to production so that everyone has a clear idea of what will be delivered.”
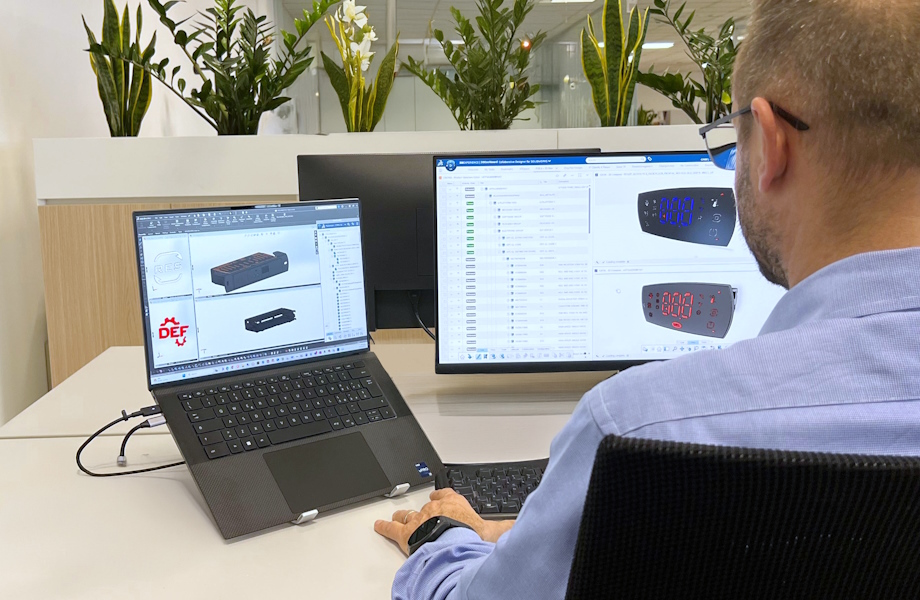
Customer-focused change
Building on the success it has achieved so far, CAREL’s goal is to scale up its use of the 3DEXPERIENCE platform across more product lines. The company also aims to bring incremental improvements to its development approach by integrating more of its engineering design processes into the platform and embracing ENOVIA’s change and issue management capabilities. From there, it will further optimize its manufacturing operations and explore ways to help customers become more efficient and sustainable through its control solutions.
“We’re well aware that our industry consumes a lot of energy, so we’re committed to helping our customers reduce their usage,” Toffanin said. “The 3DEXPERIENCE platform can contribute to our environmental, social and governance targets by making our design and industrial processes even more efficient by reducing material waste in production, improving remote collaboration to lessen the need for travel, and supporting us to develop smart, sustainable products.”
At every stage, CAREL will retain a firm focus on its customers, making sure that its own digital transformation aligns closely with their ongoing requirements and delivers meaningful value.
“Our approach is customer first – we discuss with our customers what they need and how we can help,” Toffanin said. “You could risk wasting time improving your internal processes without any positive benefits to your customers, so we wanted to be more holistic in our approach and make changes across the entire value chain. The decision to begin the digital transformation journey step by step allowed us to achieve fast and tangible results early on – and this motivates everyone to support our vision.”
Discover more about the Digital Equipment Continuity industry solution experience.
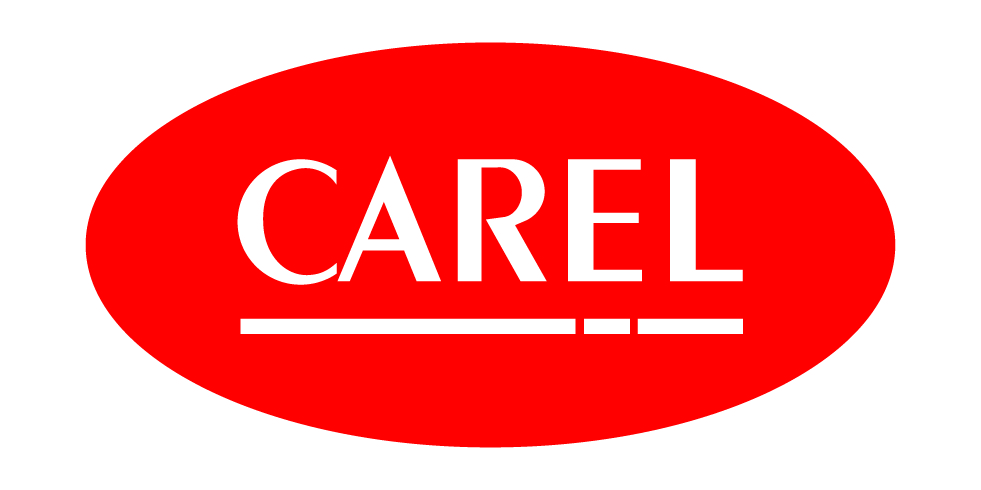
Focus on CAREL INDUSTRIES
Based in Italy, CAREL is one of the world’s leading manufacturers of control solutions for air conditioning, refrigeration and heating, and systems for the improvement of indoor air quality. The company designs products to help its customers achieve energy savings and reduce their environmental impact, combining the most advanced technologies and customized services to optimize the performance of equipment and systems. CAREL’s solutions are used in commercial, industrial and residential applications.
For more information: https://carel.com
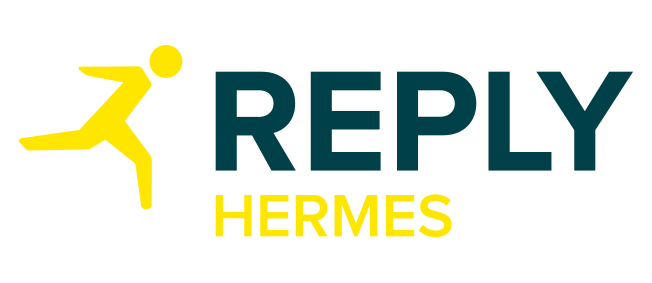
Focus on Hermes Reply
Hermes Reply offers management consulting, IT advisory and implementation services for the introduction of industry 4.0 technologies. The company has 20 years’ experience in the automotive and manufacturing sector and an international presence with offices located in Italy, Poland and China. Part of Reply Network, Hermes Reply provides access to a technology playground with expertise in a broad array of innovation domains.
For more information: http://reply.com/hermes-reply
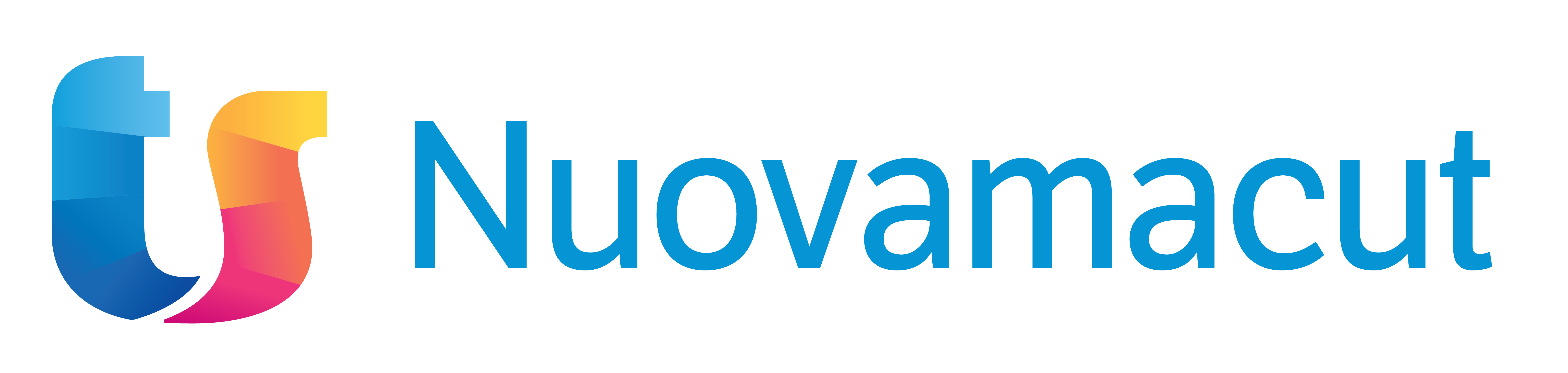
Focus on Nuovamacut
Nuovamacut is an Italian company and Dassault Systèmes partner with strong expertise in CAD, CAM, CAE and PLM. The company is active across Italy, supporting customers of all sizes and complexities, operating in different sectors ranging from the mechanical industry, design, and construction of molds, consumer goods, and technological equipment to aerospace, transport, planning, and design services.