CARBOMILL
CARBOMILL in Switzerland is a specialist in the machining of composite materials and supplies leading manufacturers in the aerospace, defence and automotive industries. The company has moved its design, engineering and manufacturing processes to the 3DEXPERIENCE platform on the cloud to deliver parts of the highest quality. It uses the Digital Equipment Continuity industry solution to visualize parts, modify geometries, and plan, detail, test and optimize its machining processes.
High precision milling all the way to Mars
When the European Space Agency’s (ESA) Rosalind Franklin rover lands on Mars, it will begin an unprecedented search for past and present signs of life on the Red Planet. Roaming the Martian terrain, the rover will drill into the planet’s surface looking for evidence of organic matter buried deep underground. All of the scientific instruments and computers needed for this endeavor are housed within the rover’s bathtub-shaped chassis. Made from carbon fiber with an inner honeycomb structure, the chassis is a culmination of engineering expertise from across Europe, including a team of mechanical machining specialists from CARBOMILL, based in Switzerland.
CARBOMILL’s role was to precisely mill hundreds of contours in the chassis’ laminated mold and then, at a later stage, mechanically machine it once the inserts and brackets were bonded in place.
“We received the carbon bonded structure from the customer along with the CAD model,” said Roland Hoffmann, key account manager and quality manager at CARBOMILL. “It was already worth over a million euros so there was a great deal of pressure to get our job right. There were more than 2,000 different operations for us to do on it.”
The CARBOMILL team couldn’t afford to make a single mistake. One hole milled even a fraction of a millimeter out of place could have jeopardized the entire chassis. That’s why the decision was made to simulate every process virtually first – a task carried out using the 3DEXPERIENCE platform on the cloud. CARBOMILL simulated all the numeric code (NC) before running it on the machine. This was particularly important for positioning the carbon fiber component on the table in the correct orientation and defining the optimal set up. Because of the machine kinematics, there are two possibilities to get to the same point and it was only through simulation that the team could determine the best approach and ensure high accuracy.
“We had to define the dimensions and make sure the milling and drilling job was going to be completely error free,” said Markus Speckert, IT business analyst at CARBOMILL. “All of this was achieved using the 3DEXPERIENCE platform on the cloud. From the CAD model, we programmed and simulated the entire NC for the machine so we could virtually see and understand exactly what it needed to do.”
Sometimes, we’re under extreme time pressure and the platform gives us the security to say we can deliver. Whatever the customer needs to mill or drill, we have the confidence and the capabilities to do it.
A one-stop shop for high performance milling
CARBOMILL is used to complex, high accuracy jobs like the rover project for ESA. The company began life processing composite components for automotive racing and has since built up a strong reputation within the aviation, aerospace, medical and industrial sectors, which seek its expertise in high precision machining. Today, CARBOMILL has multiple state-of-the-art machining centers and a technology infrastructure to match – every project is handled within the 3DEXPERIENCE platform on the cloud.
“We are a one-stop machining shop, carrying out all design, engineering and production in house as we work closely with our customers to understand their needs all the way to delivering the final part,” Hoffmann said. “Working in fields like car racing, we must be fast and very flexible. We also serve highly regulated industries such as aerospace where we must adhere to the latest standards. The 3DEXPERIENCE platform supports us to manage all the engineering behind each different process, maintain full traceability and deliver on time.”
Connecting data and precision cnc machines in the cloud
CARBOMILL’s cnc programmer have long been familiar with Dassault Systèmes solutions and want to continue using industry-leading technology to support them. Moving from an on-premise installation of the 3DEXPERIENCE platform to the cloud-based version made sense for the company on many levels. Not only was it easy to transfer existing CAD data, but the team valued the ability to centralize all product data with full version control, as well as gaining access to automatic upgrades and new features.
“The aim of switching to the cloud was to make it easier to handle our IT internally – no more time and cost intensive server installations and updates,” Speckert said. “Because we’re always using the latest version, we can read any data file from our customers. We really appreciate having all our data, tools and machines connected in the platform’s standardized environment. It means that everyone is working from the right information and there’s no risk of duplication. We can also reuse existing data for new projects so that we’re not always starting from scratch.”
Cenit is always on hand to provide support to CARBOMILL. Speckert and the team appreciate the one-to-one contact and tailored advice provided by the Dassault Systèmes business partner.
“If we ever have any issues to discuss, Cenit gives us a single point of contact and we can get the information we need,” he said. “They join our frequent development meetings along with Dassault Systèmes to help shape our roadmap and hear about the ideas we have. I feel like they treat us on the same level as a big company. The relationship is really important to all of us.”
CARBOMILL's task in developing the rover was to mill hundreds of contours into the laminate of the chassis. They couldn't afford to make a single mistake - and thanks to the 3DEXPERIENCE platform, it all worked out. The team first simulated each process virtually in the platform, using the CAD model to programme and simulate the entire NC for the machine.
Tailored processes for a limited-edition watch
The scope and scale of projects CARBOMILL takes on varies widely, ranging from one-off jobs like the ESA chassis all the way to producing 1,000 carbon fiber cases for the Coulson Limited Edition watch from ORIS. For this highly specialized project, the team helped to define the case’s final geometry and shape using the 3DEXPERIENCE platform and then developed the appropriate method for processing each piece.
“It was entirely new for us working on such a small scale,” Speckert said. “The smallest hole we had to mill in the 3D printed carbon housing was 0.3 millimeters. We used CATIA to get the optimal shape for the stock material and modified the geometry to make it easier to mill and get a better quality finish. The first prototype was tested and validated in the 3DEXPERIENCE platform. Then, with DELMIA Machining, we developed a special clamping and processing concept to mill the 1,000 carbon fiber watch cases. We looked at how to machine it and made all the checks. If we have to drill a specific hole or mill a complex surface like this, DELMIA gives us those opportunities.”
Working in fields like car racing, we must be fast and very flexible. We also serve highly regulated industries such as aerospace where we must adhere to the latest standards. The 3DEXPERIENCE platform supports us to manage all the engineering behind each different process, maintain full traceability and deliver on time.
Faster, more accurate quotes
One of the key benefits CARBOMILL is seeing from moving to the 3DEXPERIENCE platform on the cloud is the ability to accelerate the quoting process. Being able to check each customer brief in detail and virtually validate the machining process allows the team to generate estimates with high accuracy from the onset, rather than encountering costly setbacks when unexpected issues arise.
“We are far more efficient issuing offers and more accurate in our price estimates because we’re all working from the same data,” Hoffmann said. “We can help our customers make a better choice. There’s also no longer a risk of production using the wrong version of a design.”
Now, from the moment a customer wants to discuss a new project, CARBOMILL is able to explore how to effectively machine the part and consider all possible options, such as whether additional geometry modifications or vacuum tools are needed. The entire process is managed in the 3DEXPERIENCE platform with all technical data and versioning control to keep each project on track.
“Recently, we took on what initially seemed like a simple project to mill the shape of a big square box and drill holes into it,” Speckert said. “However, when we loaded the model into the platform, we could see that the faces weren’t flat; the time to machine everything was going to take much longer and we’d need to use different tools. Because we checked this upfront, we could give the customer a clear indication of the cost and time involved – there were no surprises.”
As CARBOMILL continues to develop its capabilities and bring in new state-of-the-art machinery, it knows it can rely on the 3DEXPERIENCE platform to support every project it takes on. No part or geometry is too complex for the CARBOMILL team to tackle.
“Everybody here uses the 3DEXPERIENCE platform deeply,” Speckert said. “There aren’t many functions not known or used by us, and there’s always a solution for what we need to do. Sometimes, we’re under extreme time pressure and the platform gives us the security to say we can deliver. Whatever the customer needs to mill or drill, we have the confidence and the capabilities to do it.”
Using the 3DEXPERIENCE platform, CARBOMILL produced 1000 carbon fibre enclosures for the Coulson Limited Edition from ORIS. The team used the platform to find the perfect shape and modify the geometry, and then tested and validated the first prototype.
Q&A high precision machining
High precision machining is a subtractive manufacturing process using computer-controlled machine tools for making complex and intricate parts with very tight tolerances so they perfectly fit and work together. CNC machines cut, drill, mill and turn material according to exact specifications to create components and finished pieces.
One of the biggest benefits of this manufacturing processes is its speed and accuracy. Parts are designed and tested using CAD software so that any potential issues or errors are identified before physical manufacturing. This approach also allows for the manufacturing of parts with highly complex geometries.
Discover more about the Digital Equipment Continuity industry solution experience.

Focus on CARBOMILL
Carbomill specializes in machining fiber composite materials, metallic integral milling parts, tool making, mold making and engineering services for aerospace, racing and research. Its parts are also used in medical technology, apparatus, plant and mechanical engineering. The Swiss company was founded by Patrick Meyer in 2011 and has built up a strong reputation for its complex mechanical machining expertise. Well-known companies from the high-tech industry rely on CARBOMILL’s know-how and appreciate the enormously versatile range of services it delivers as it constantly expands its infrastructure in a targeted and future-oriented manner.
For more information: https:carbomill.ch
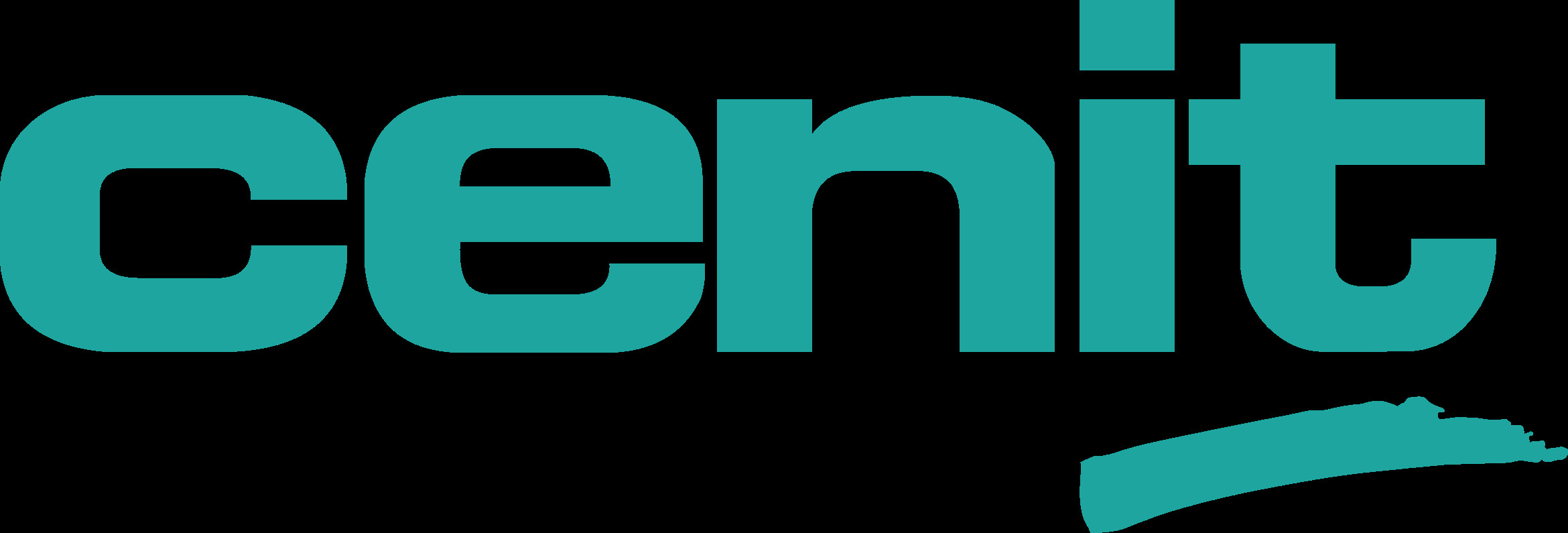
Focus on CENIT
CENIT empowers sustainable digitalization. Our solutions are based on innovative technologies in product lifecycle management, the digital factory and enterprise information management. CENIT consultants provide customers with end-to-end advice to ensure that solutions are implemented with an understanding of the entire value chain. With a holistic approach and based on trusted partnerships, CENIT takes responsibility for solutions on behalf of our clients. CENIT has been helping prestigious customers in key industries to gain competitive advantages for over 30 years.
For more Information: http://www.cenit.com/