Brano
Brano has eleven sites in the Czech Republic, offices in North America and Germany, and production locations in China and South Africa. Managing projects among the different sites was not always easy. Locating information, coordinating designers and engineers, sticking to schedules and delivering on time and on budget were becoming increasingly tedious and time-consuming tasks. To improve efficiencies, Brano selected Dassault Systèmes’ (3DS) 3DEXPERIENCE Platform, including its ENOVIA V6 application for collaborative innovation.
Features, quality and price
Technological advances and fast changing consumer preferences drive automotive OEMs to innovate and improve the driving experience. Tier 1 automotive suppliers such as the Czech Republic’s Brano are critical partners in that innovation process. “For 17 years, we have been working hard to make a name for ourselves in the automotive market by designing innovative products for our OEM customers,” Daniel Otáhal, Ph.D., Key Account Manager, Brano, said.
“Our goal is to be the best automotive supplier worldwide with the product portfolio we offer to customers,” Otáhal added. “As a privately owned company, our decision-making process is shorter so our turnaround times are faster. This flexibility enables us to adapt quickly and to come up with a more suitable response to our customers’ needs. This is what distinguishes us from other suppliers.”
While response time is important to an OEM, so are quality and price. “Many of the world’s leading automotive companies, including VW, General Motors and Volvo install our products in their cars and the price/feature ratio is a critical factor in their choice of supplier,” Otáhal said. “And in this area, we are generally less expensive than our competitors while still delivering quality products.”
Multiple sites working together
Brano has eleven sites in the Czech Republic, offices in North America and Germany, and production locations in China and South Africa. Managing projects among the different sites was not always easy. Locating information, coordinating designers and engineers, sticking to schedules and delivering on time and on budget were becoming increasingly tedious and time-consuming tasks.
“Projects generate huge quantities of data,” Otáhal said. “Information was filed in multiple isolated systems and even drawers storing hard copies; we wasted countless hours and even days looking for a document or the person responsible for a task. Inefficient project management was threatening our competitiveness and our customers’ satisfaction.”
To improve efficiencies, Brano selected Dassault Systèmes’ (3DS) 3DEXPERIENCE Platform, including its ENOVIA V6 application for collaborative innovation. In particular, Brano uses ENOVIA for project management, product data and structure management, change process management and internal collaboration.
“We follow and still improve an industry methodology for product development that was designed by Ford, GM and Daimler 15 years ago called Advanced Product Quality Planning (APQP). This set of procedures, along with the Production Part Approval Process (PPAP), is used to develop products for the automotive industry and ensure that we develop with the level of quality expected by automotive OEMs,” Otáhal said.
“We configured ENOVIA V6 Program Central to manage the 220 tasks linked to APQP. Now, our approach is consistent and every time we bid for new business we can guarantee that all project tasks are assigned to the right people and accounted for,” he said. Moreover, ENOVIA V6 helps reduce proposal response time. “We answer hundreds of requests for quotations (RFQ) every year. By capitalizing each proposal in ENOVIA V6, we are able to reuse this information for future bids, which saves us time and enables us to learn from, and avoid past mistakes,” Otáhal said. “With 3DEXPERIENCE, we increase our business potential.”
DYTRON, a Dassault Systèmes’ business partner, has established a long-standing relationship with Brano over the years and greatly contributed to tipping the scales in favor of the 3DEXPERIENCE Platform. “Their automotive experience, knowledge of the 3DS offering and complete understanding of our specific processes and way of working were all elements we believed would guarantee the success of our implementation,” Otáhal said.
Secure access, improved collaboration, more confidence
With ENOVIA V6, Brano’s management has a comprehensive view of what stage each project is in and who is responsible for what action. This helps identify bottlenecks and risks that can potentially jeopardize product delivery. “We have greatly reduced the number of manual tasks tied to locating information and status of delivery. Everything is in ENOVIA V6 and each Brano manager has secure access to this information whether they are in the Czech Republic or in our extended ecosystem, via an Internet connection,” Otáhal said.
We configured ENOVIA Program Central to manage the 220 tasks linked to APQP. Now, our approach is consistent every time we bid for new business.
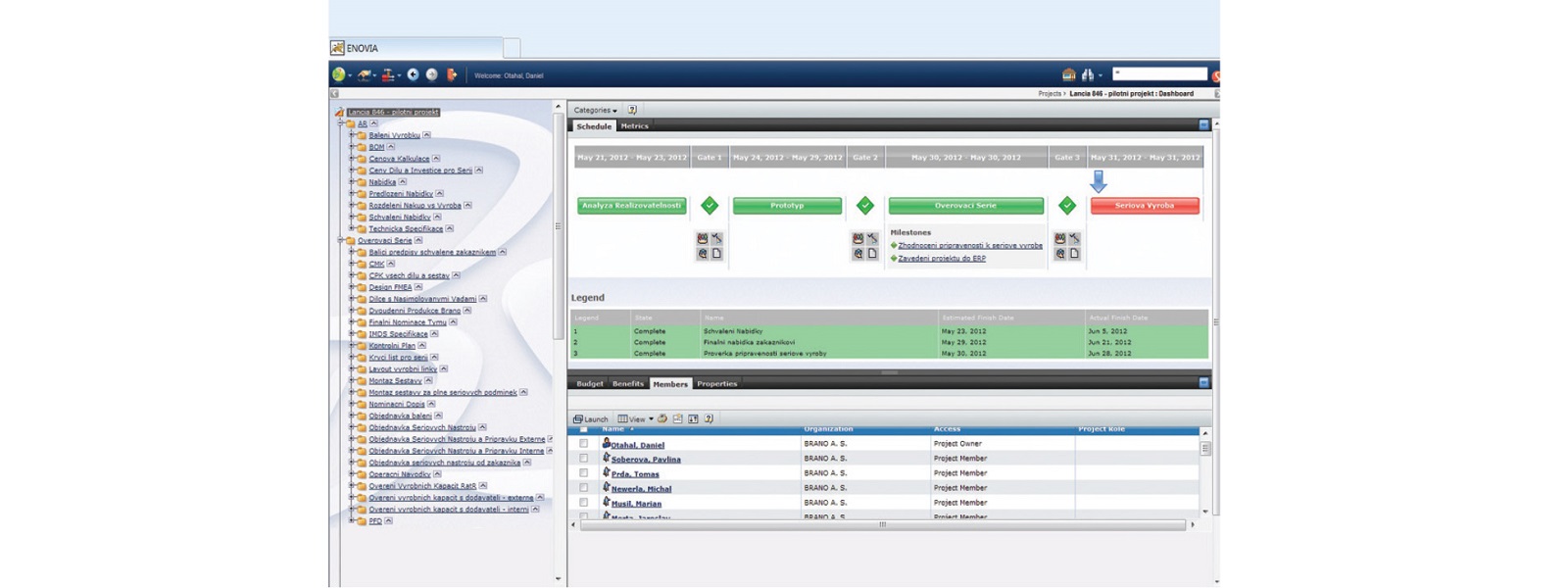
“This level of transparency has improved the collaborative experience for our designers and project actors since everyone has immediate access to the right information,” Otáhal said. “Moreover, we now have a foundation for innovation since ideas are more easily exchanged based on a 3D visualization of the product using the 3DEXPERIENCE application ENOVIA 3DLive.”
Brano can approach any OEM quality audit with confidence since there is traceability for each project. Data, documents, workflows, and tasks are all labelled and documented in ENOVIA V6. “Traceability contributes to the sustainability of our products,” Otáhal said. “Our OEMs are satisfied because all the information is accounted for. At Brano, we have the means to analyze what went right and what went wrong for each project,” he added.
Brano works for many OEMs and designs its products using the same design solution as its customers. All its multi-vendor CAD data, however, is managed by ENOVIA. Engineers can access engineering information in the 3DEXPERIENCE Platform from within their native CAD application, which includes CATIA V5 as well as other design software. “We also manage a multi-discipline bill of materials with ENOVIA Engineering Central that reflects the different technologies (software, electrical, mechanical) that can go into a product,” Otáhal said.
Recently, Brano showed a customer a virtual preview of one of its product designs. “We arrived with an animated 3D model and demonstrated its capabilities with the 3DEXPERIENCE application 3DVIA Composer,” Otáhal said. “As a marketing tool, there is nothing more powerful than a realistic representation of a future door mechanism or trunk releasing system that the customer has the impression he can almost touch and experience. We plan to extend the use of 3DVIA Composer to showcase our innovations through this type of experience, which we want to systematically generate for our customers and prospects,” he said.
Over 130 Brano employees use the 3DEXPERIENCE Platform at the moment and this number will continue to grow. The company also plans to cover other aspects of their development process in the future. “We are considering managing customer requirements with ENOVIA and linking them with project tasks. By capitalizing all OEM requirements, we ensure better traceability,” Otáhal said.
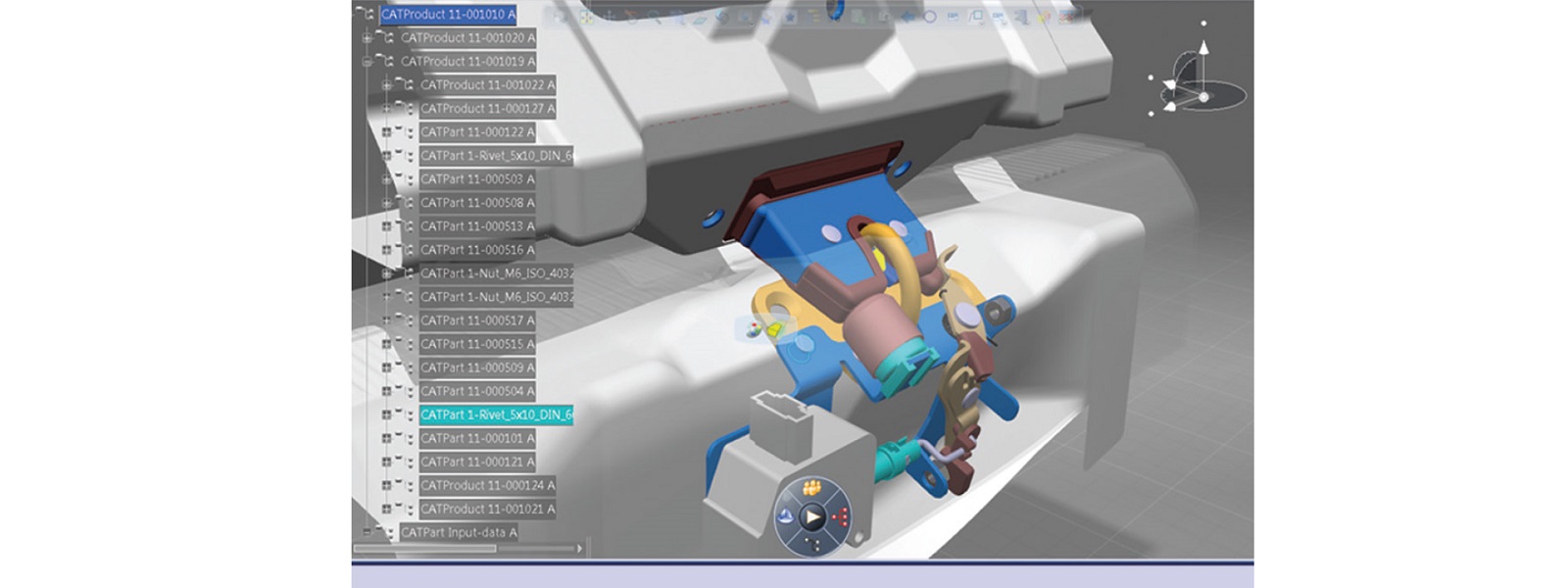
Consistent project management, automated resource planning, phased-base decision making process, traceability, collaboration, multi-CAD data management, virtual preview: these are all reasons why Brano’s dream to become the best automotive supplier may just come true.

Focus on Brano
Tier 1 supplier of automotive products.
Products: Door mechanisms, pedals, carjacks, cockpit systems, hinges, shock-absorbers, latches, tools, etc.
Employees: 2,300
Headquarters: Hradec nad Moravici, Czech Republic
For more information www.brano.eu
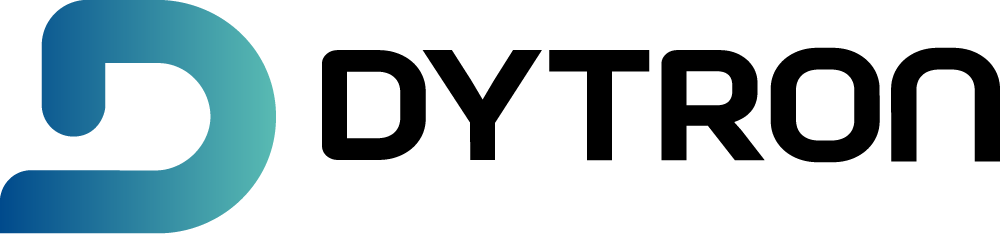
Focus on Dytron
DYTRON Company Ltd. was established in 1992 and is an authorized industry solution provider of Dassault Systèmes’ 3DEXPERIENCE Platform in Czech Republic. DYTRON helps to improve business innovation and quality process, mainly in Product Lifecycle Management area, delivering consulting services and expertise to its partners. DYTRON operates in Aerospace & Defence, Transportation & Mobility (Automotive), Electronics and High Tech, Energy and Building Industry. Based on its deep automotive industry knowledge, DYTRON developed implementation methodology to support Tier 1 automotive suppliers in their effort to follow APQP / PPAP processes.