BETA Technologies
US-based electric aerospace manufacturer BETA Technologies sought to replace multiple disparate software solutions with a single integrated environment to facilitate a more holistic approach to design and manufacturing as the company looks to achieve regulatory approval of its aircraft. BETA chose Dassault Systèmes’ solutions to reduce time to market through the 3DEXPERIENCE platform, a collaborative product development environment. The Reinvent the Sky and Co-Design to Target industry solution experiences support Beta Technologies’ process acceleration from concept to certification.
A holistic approach to electric air travel
Kyle Clark, the founder and CEO of Vermont-based electric aerospace manufacturer BETA Technologies, may have mastered the art of big-picture thinking.
Recognizing the opportunity of electric air travel, Clark not only developed two all-electric aircraft — the ALIA VTOL and ALIA CTOL — for transporting cargo, medical supplies and, ultimately, people but also created the infrastructure and training programs required to support their operation. BETA is already rolling out a comprehensive charging network comprising multimodal and interoperable chargers capable of powering various types of electric vehicles, including electric aircraft as they come into service. In addition, BETA provides immersive simulators to train pilots and mechanics, while working with local schools to create curriculums that help prepare a new generation of engineers to work in electrical aircraft development.
Clark’s holistic approach also is apparent in how his company designs and manufactures its products. He advocates integrated design – an approach that connects traditionally siloed disciplines, such as engineering, design and production, in a single collaborative environment. He’s doing all this with Dassault Systèmes’ solutions portfolio for the aerospace industry.
“We quickly learned that designing an electric aircraft is a complex holistic process – this requires a collaborative and highly integrated product development software environment,” said Jesse Cannon, BETA’s Product Lifecycle Management systems lead. “With Dassault Systèmes’ portfolio, we get an industry-leading solution with plenty of scope to grow with as we achieve BETA’s goals.”
We quickly learned that designing an electric aircraft is a complex holistic process – this requires a collaborative and highly integrated product development software environment. With Dassault Systèmes’ portfolio, we get an industry-leading solution with plenty of scope to grow with as we achieve BETA’s goals.
Challenge
BETA’s early use of multiple disparate software solutions inhibited Clark’s goal of a collaborative approach to design and manufacturing. Without a single source of truth, it was difficult for the company to achieve regulatory approval of its aircraft.
BETA explored Dassault Systèmes solutions to facilitate a robust, integrated environment. This search was key to establishing a fully connected product development lifecycle that would help BETA achieve certification to fly from the United States Federal Aviation Administration (FAA).
Solution
After seeking advice from local Dassault Systèmes technology partner Inceptra, BETA chose the 3DEXPERIENCE® platform as it’s a best-of-breed environment that includes CATIA for product design, DELMIA for process planning, ENOVIA for product data management and SIMULIA for stress analysis.
Inceptra’s team was on hand to support the implementation at every stage, analyzing and addressing key infrastructure requirements and providing training to BETAs’ team leaders on how Dassault Systèmes’ applications work together to provide optimum value.
Benefits
Now, BETA increasingly works in a single, integrated software environment that facilitates great collaboration and fast development of its aircraft.
Using various roles within CATIA and working across multiple locations, engineers design aircraft systems including the wing, booms, empennage and fuselage. Battery and motor products also are developed within the platform’s unified environment so the engineers can easily manage and visualize data. The virtual twin of the assembled aircraft combines these various parts for a holistic view.
SIMULIA’s structural stress analysis helps BETA’s engineers conduct detailed simulations and ensure certification viability. Any issues can be resolved quickly and easily using collaborative Digital Mock-up (DMU) reviews in ENOVIA that show reviewers’ mark-ups in real time.
At the same time, manufacturing and production teams generate a manufacturing bill of materials (MBOM) with DELMIA and utilize its capabilities to create process plans and deploy a collaborative, end-to-end change management process. ENOVIA and DELMIA enable evaluation of engineering change, and facilitate parallel updates to impacted manufacturing definitions.
As production ramps up, BETA plans to develop process plans and work instructions in the context of the assembly line before any physical builds take place. This approach forms the basis of a 3D virtual twin of the company’s entire manufacturing facilities and processes that will help BETA achieve digital continuity across its business and, ultimately, help meet its aim of starting commercial operations in 2025.
Discover more about the Reinvent the Sky and Co-Design to Target industry solution experience.
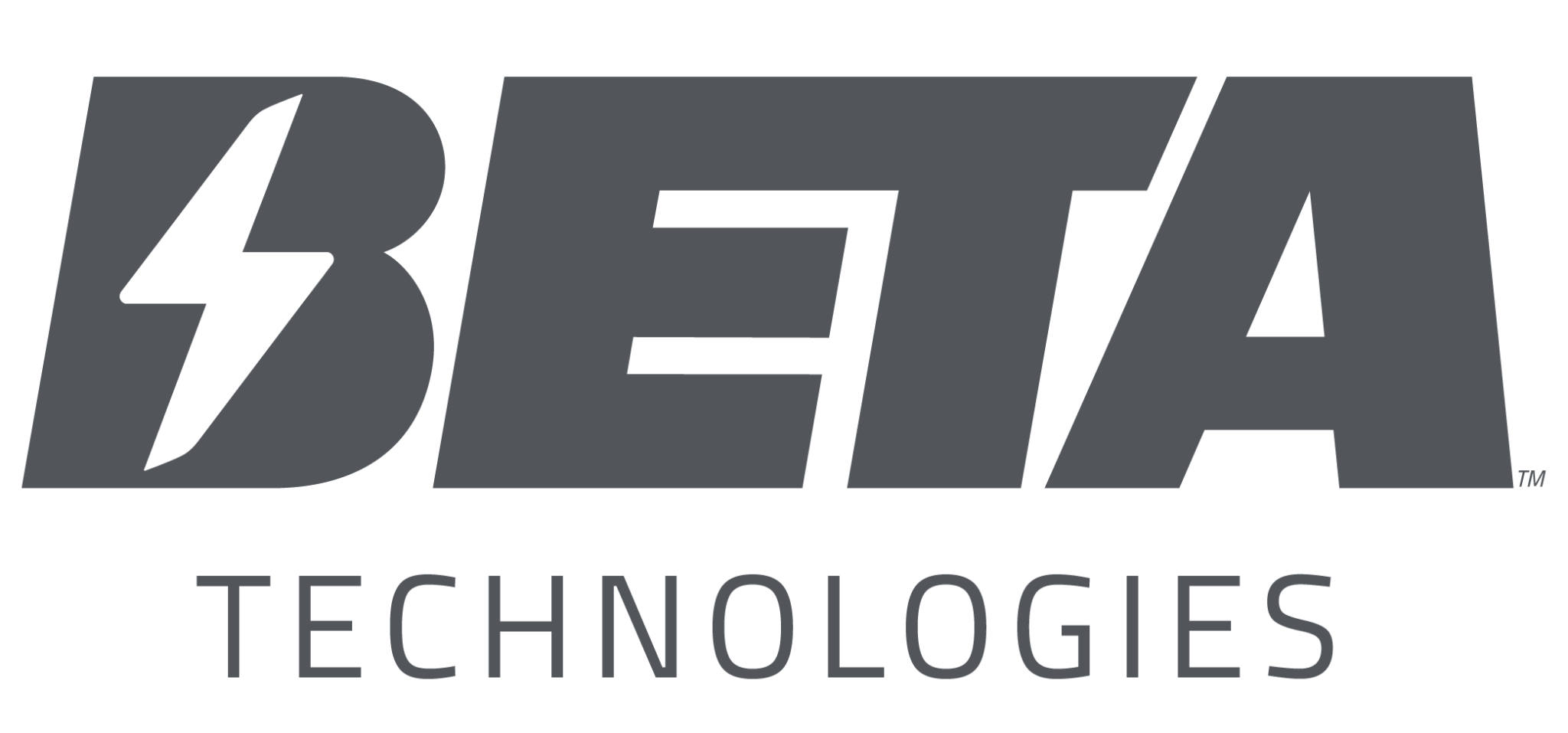
Focus on BETA Technologies
BETA Technologies is an electric aviation company based in Burlington, Vermont. Founded in 2017, BETA is working to change the paradigm of how we transport goods and people by making aviation cleaner, safer and more cost-effective. To do this, the company is producing all-electric aircraft; multimodal, interoperable charging infrastructure; and training programs for next-generation pilots and maintainers. The BETA team designed and is pursuing certification of two electric aircraft, including an electric fixed-wing and an electric vertical takeoff and landing (eVTOL) aircraft. The company also brought more than 20 chargers online across the East and Gulf coasts, with over 50 more in development.
For more information: https://www.beta.team
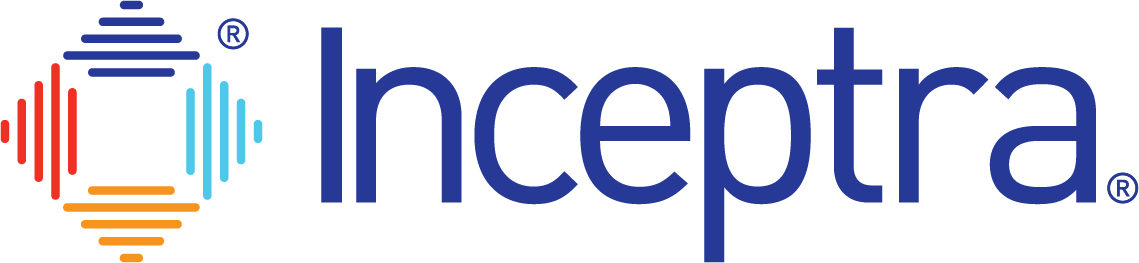
Focus on Inceptra
Inceptra helps engineering and manufacturing enterprises of all sizes across a variety of industries with best fit solutions to digitally design, simulate, produce, and manage their products and processes, enabling enhanced innovation and productivity. We are dedicated to Dassault Systèmes’ product portfolio, plus complementary software and internally developed PLM acceleration solutions. Inceptra’s offerings include software, support, training, and consulting services, including integration services, automation services, and industry best practices.