Axelent Engineering
As part of its transformation from a traditional mechanical workshop to a smart machine solutions provider and knowledge company, Axelent Engineering in Sweden needed a powerful platform to bring its vision to life. The company adopted Dassault Systèmes‘ Simplified Smart Equipment industry solution based on the 3DEXPERIENCE platform to digitalize its processes and seamlessly connect design, engineering and manufacturing.
Leading through knowledge
Axelent Engineering is on a mission to create machines that work even harder for its industrial clients. The Swedish business, which builds unique specialist machinery for local industries, plans to create smart machines that are connected to a digital environment, giving them the capabilities to automatically adjust their settings to work more efficiently and to flag maintenance issues and order spare parts without human intervention.
It’s all part of Axelent Engineering’s wider vision to become a leading smart automation solutions provider. Since it was founded in 1972 under the name Hestra Mekaniska, the company has established a strong reputation for its high-quality, unique machinery designed for more efficient production. Today, it is going a step further by honing its automation expertise.
“We started out as a traditional mechanical workshop but today we define ourselves as a competence company,” said Richard Skogward, CEO of Axelent Engineering. “A big part of our business is the development of special machinery. Our core competence is making our customers profitable throughout the lifetime of the machines they buy from us. They look to us to deliver smart, self-correcting machines that are easy to run but deliver maximum efficiency and output. To achieve this, we needed to combine our strong history in machine building with high technology and embrace the concepts of Industry 4.0.”
The company entered into a partnership with Dassault Systèmes to implement the 3DEXPERIENCE® platform and digitalize its processes as well as explore the potential of simulation and virtual twin experiences.
“A few years ago, there was a general trend for manufacturers to move production to regions with lower labor costs and we were amazed that they hadn’t analyzed what automation could bring to the table,” Skogward said. “We wanted to continue to produce within our own country and turned to high technology and automation to differentiate ourselves. We also saw the vision that Dassault Systèmes had and combined it with our own, to embrace the virtual twin concept to simulate a complete machine, as well as include a network of suppliers to join our complex projects. To be collaborative and effective, you need a good platform, and for us that was the 3DEXPERIENCE platform. With the latest technology, we want to deliver the best, highest quality machines to our customers and ensure they remain relevant in a highly competitive world.”
To be a competitive company and attract highly skilled people, you need the best platforms and to be modern in your thinking.
Top talent takes business to another league
Axelent Engineering’s decision to implement the 3DEXPERIENCE platform goes hand in hand with its growth as a competence company, helping it to upskill its workers, pursue highly skilled talent and continuously develop its workforce.
“We need to attract and retain the best engineers and students to stay ahead in the market,” Skogward said. “If you have the best platform, you can appeal to the best engineers and empower them to work in a modern way.”
As the company continues to make more sophisticated machines, it also needs to be able to work with a network of highly skilled suppliers.
“Another challenge we wanted to solve is integration with our suppliers,” Skogward said. “To do that, we needed an open platform, and to fully integrate them into our processes. We also wanted a way of recording what we do and how we develop so we can play it back again and learn from it. It’s about recording competence to communicate competence.”
Backed by powerful, modern technology, Axelent Engineering has set itself on an upward trajectory for success as it grows its capabilities and adopts new, more efficient ways of working. “We now employ more highly educated people and it enables us to make more advanced things,” Skogward said. “To be a competitive company and attract highly skilled people, you need the best platforms and to be modern in your thinking – you need to be a visionary. To have this platform is also a statement to our customers. It shows that we’re investing heavily in our future, and it puts us in another league from the competition.”
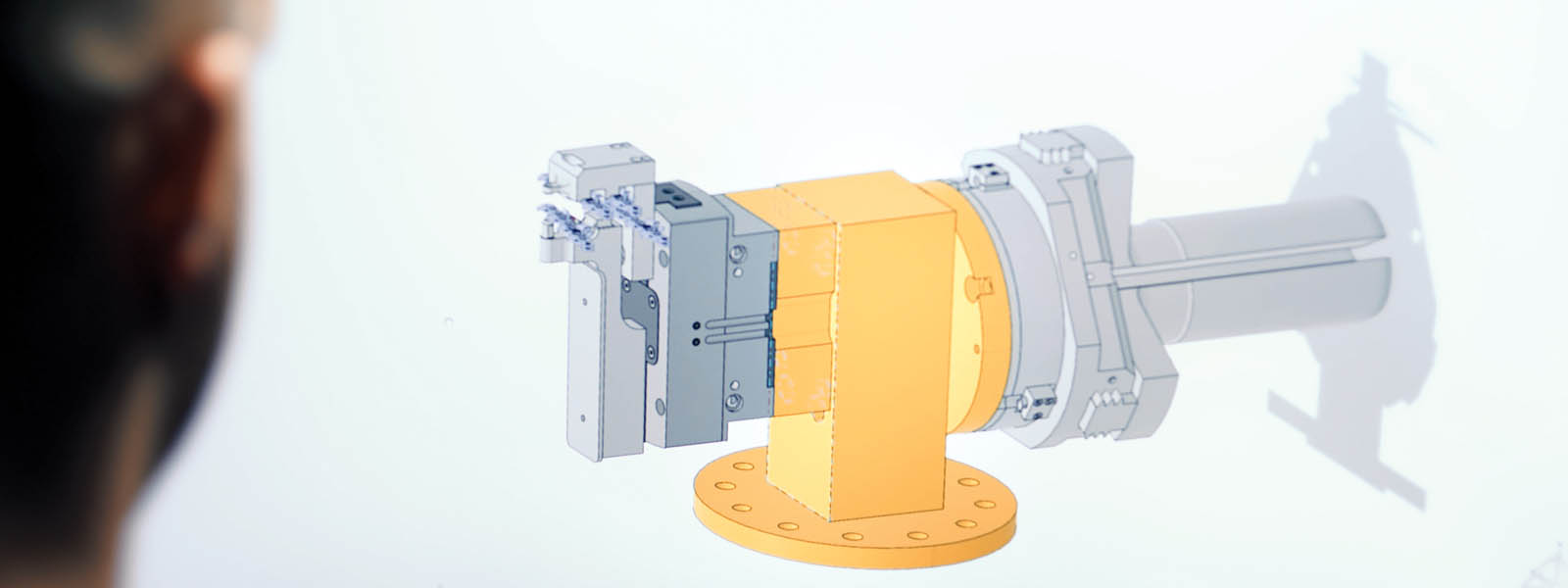
3D Design Library
The machines Axelent Engineering makes today involve many more parts, components and disciplines than before.
“An ordinary machine that we make today involves 10-20,000 new drawings in the design stage,” Skogward said. “And we need to handle these drawings in the project lifecycle, which can last anything from six to 12 months. We also needed to involve a lot more competences.”
The company is using the design application CATIA on the 3DEXPERIENCE platform to develop its 3D models. This helps to speed up product development and at the same time, it can create a design database to reuse part designs for future machines, no matter how complex and unique they may be. The platform also can handle and incorporate CAD files in different formats received from Axelent Engineering’s suppliers.
“Now, we’re using 3D models to create every part,” said Mirko Miljevic, PLM manager at Axelent Engineering. “We have reduced a lot of drawings that we need for our components as we can reuse much more of what we’ve designed already. You need to have a good database and feature recognition capabilities to find the parts you need, which the 3DEXPERIENCE platform has. With CATIA, we have a complete design library at our fingertips from wherever we are.”
This new 3D approach, combined with enhanced project management capabilities enabled by ENOVIA, saves time during the design phase and brings about efficiencies further down the production chain.
“At the assembly stage, it was impossible to see the full assembly, but now our teams can look at the machine virtually, which makes it much easier to see how the machine should be assembled,” Miljevic said. “We also had this problem with suppliers. If you’re a project leader and you have 20,000 parts, some made by sub suppliers, you want to know where all the parts are. Our mission was to connect the ERP system to the 3DEXPERIENCE platform so we could see in the visual where all the parts are. So, for example, you could look at the model and see which parts haven’t yet arrived, which are mounted and so on. We wanted to give our project leaders the best tools to be able to deliver the machine on time with the right specifications for the customer.”
The time we spend on warranties is five to ten times lower as we now don’t need to be at the customer site for as long fixing problems.
Build once, build well
Axelent Engineering also is taking advantage of the manufacturing simulation capabilities in DELMIA to develop machines right first time, guaranteeing quality at every step of the development process.
“We’re doing a lot of simulation of robotics using DELMIA to solve problems early on,” Miljevic said. “It helps our engineers to have the right information delivered to the right departments. We don’t have a lot of time to develop a product, so we’re building on experience. And when you’re making one-of-akind machines, you need to deliver the correct information to the next department, and we’ve achieved that. Our engineers have access to all the information and revisions they need and they have full control of them, even if the products are very complex. And then all colleagues on other sites have access to that information too.”
With a more efficient product development process, Axelent Engineering is not only making fewer errors, it also is becoming more sustainable – generating far less waste and making better use of its resources.
“The platform enables us to handle all materials responsibly,” Skogward said. “If you have a good platform you naturally use and need fewer materials.” “If you measure our scrap, it is five to ten times lower since we implemented the platform,” Miljevic added.
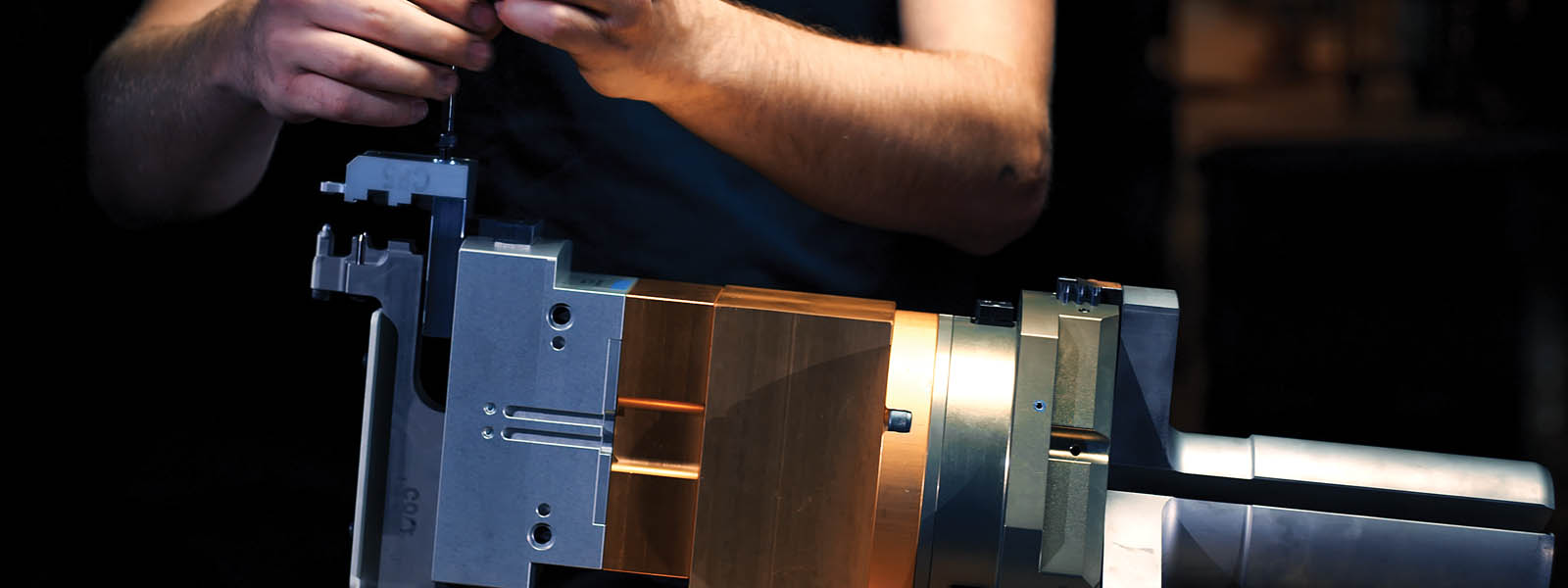
Sharing and reducing risk
As Axelent Engineering continues to build its design library and database on the 3DEXPERIENCE platform, it is also helping to solve a critical issue that businesses in this industry face: risk.
“Building specialty machinery is a high-risk business,” Skogward said. “You need to promise that the machine will deliver to the specification. If you do not deliver, you get penalties – for late delivery, for not reaching targets, for errors and malfunctions under warranty and so on. You need to have a good database to minimize these risks, and that means you need to reuse a lot of data and be able to calculate the risk at every stage. The risk management functionality included in the platform helps us handle risk and identify issues before they become a bigger problem. We can classify the risk too and calculate the total risk management for each project.”
Axelent Engineering now learns from past mistakes and has rigorous quality checks and reporting capabilities in place to keep its risk profile under control.
“We can now compare machines and find similarities to minimize the risk for some of the parts,” Miljevic said. “And if something is amiss, you can always create a comment that is connected to a specific part, complete with a photo or request. That information is then immediately available to the other engineers so the issue can get quickly resolved before progressing to the next stage in the development process.”
These capabilities also translate into improvements in the aftersales stage of the product lifecycle.
“The time we spend on warranties is five to ten times lower as we now don’t need to be at the customer site for as long fixing problems,” Miljevic said.
Making customers more profitable
Axelent Engineering’s customers need smart, automated machines that are flexible and intelligent, and able to adapt their behavior automatically to maximize output, run efficiently and ensure profitability throughout their entire lifecycle. As the company explores how it can better serve its customers, then, it will increasingly turn to virtual experience twins to improve the performance of its machines.
“Our vision is to deliver a virtual twin with the machine so when the customer wants to make adjustments, we can make them on the virtual twin and prove they work before we make the physical upgrade, all without interrupting their production,” Skogward said.
Soon, Axelent Engineering plans to sell the 3DEXPERIENCE platform on cloud along with its machines as an entire package. “We want to make it easier for our clients to program their machines and robots,” Miljevic said. “They can see the success we’re having with the 3DEXPERIENCE platform and we want to help them be more successful too. Our goal is to sell the machine and the platform together, so they can reprogram their robots to carry out specific tasks. We’re not there yet, but we will be.”
Backed by the 3DEXPERIENCE platform, Axelent Engineering will continue to evolve and grow its business as a leading knowledge company that its customers can rely on and become more successful with.
“We have been very profitable and would not have been so without this strategy,” Skogward said. “It’s not just words for us. We look at what value we can create for our customers and the platform helps us do it better.”
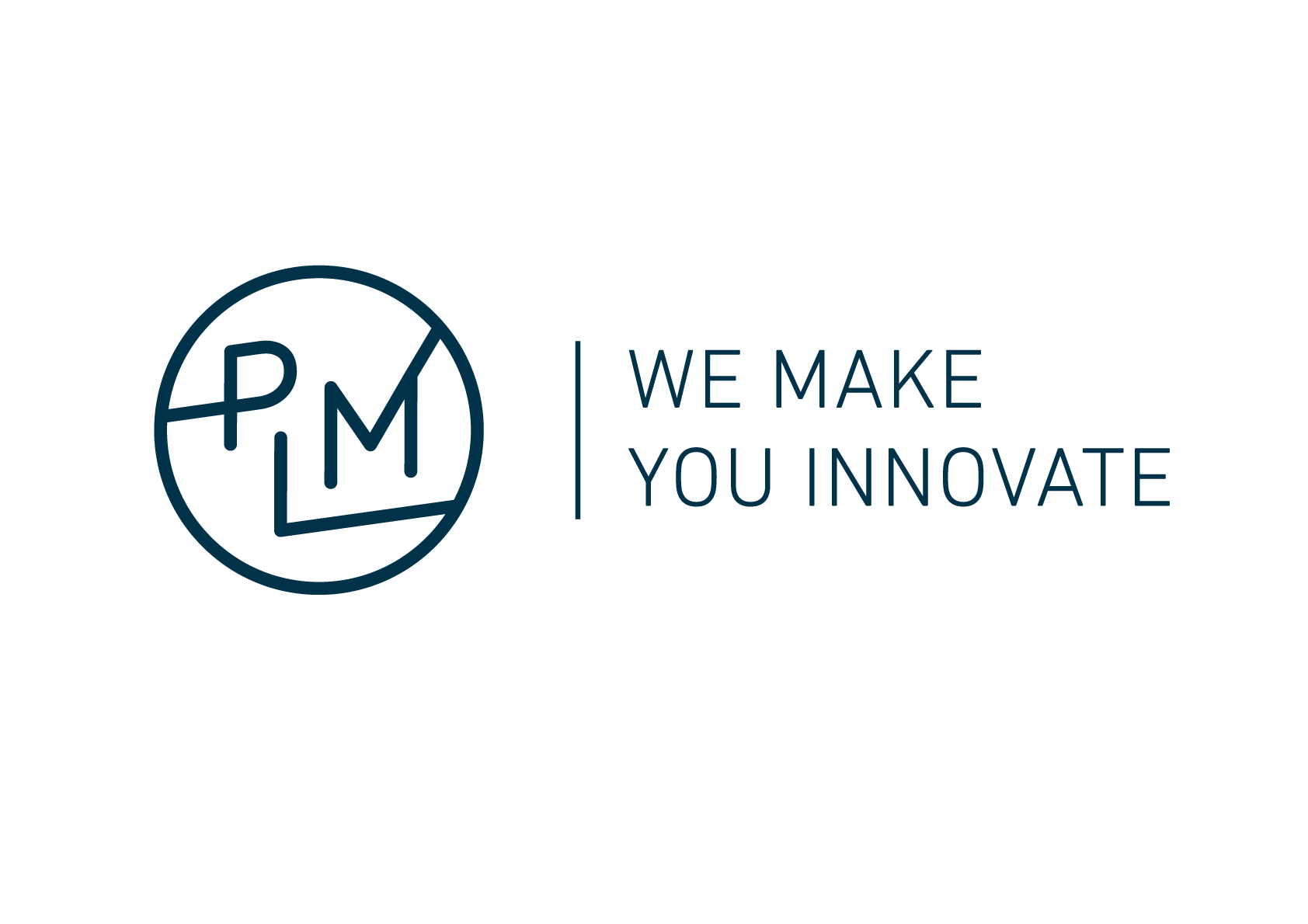
Focus on PLM Group
PLM Group has been collaborating with Dassault Systèmes for over 25 years as a value-adding partner. The company's expertise in 3DEXPERIENCE is helping companies connect people, processes, and ideas enabling them to pioneer the future and gain a competitive advantage in the market. PLM Group helps its customers transform their value chain by adding the latest technology including augmented reality, virtual testing, and generative design for a future-proof business.
For more information: https://plmgroup.eu