The University of Sheffield / AMRC
Dassault Systèmes’ technology enables the University of Sheffield Advanced Manufacturing Research Center (AMRC) to create a digital thread across the end-to-end manufacturing process and to leverage the virtual twin to evaluate transformational approaches for the aerospace and defense industry. Using the Ready for Rate industry solution experience allows the AMRC to deliver better outcomes for the industry and provide students with industry-relevant capabilities.
Bridging the gap in aircraft manufacturing
Recognizing that academic research doesn’t always filter down into real-world manufacturing businesses, Professor Keith Ridgway from the University of Sheffield in the UK teamed up with local businessman Adrian Allen to create the Advanced Manufacturing Research Centre (AMRC). This facility bridges the gap between cutting-edge research in university labs and the day-to-day needs of businesses, particularly those in the aircraft industry.
Since its establishment in 2001, the AMRC has become a world leader in manufacturing excellence and part of the UK’s High Value Manufacturing Catapult strategic research and innovation hub. Its network includes 70 universities and more than 1,000 companies of all sizes, from the smallest start-ups to the biggest names in manufacturing. To date, the AMRC Training Centre has recruited over 2,200 apprentices.
To drive the next wave of innovation in the aircraft industry, the AMRC acknowledges the importance of adopting top-tier technologies already utilized by industry leaders. In line with this vision, it recently renewed and expanded its partnership with Dassault Systèmes. This collaboration includes the provision of software, training, and support to help the AMRC deliver advanced insights to aircraft manufacturers while equipping the next generation of professionals with the skills needed to excel in the sector.
Stephen Beecher, Senior Engagement Manager for Aerospace, AMRC:
The AMRC is the Advanced Manufacturing Research Centre, part of the University of Sheffield, that deals with automation, robotics and digital technology.
CHALLENGE
There's a significant demand for manufacturing aircraft in which the typical ramp rates are around 30 to 40 shipsets per month. Companies are now being asked for 80 shipsets per month. So with the traditional techniques, that's not economically viable. With regards this evolving change, we're moving more into digital technology and the handling of data in particular.
SOLUTION
By having Dassault Systèmes as an overarching platform, we're actually able to string that data together, and can identify where there's non-conformities to make changes to the process and see how that influences downstream and upstream processes, and really be able to look at it as a complete digital thread, and manage that data as part of the virtual twin.
BENEFITS
My main takeaway would be the case of being able to have a platform that has individual elements that can all talk that one language. And if there's any changes within an item, you can see the influence it has everywhere else within the sequence of events.
Modernizing aircraft industry
Aircraft manufacturers are currently finding it challenging to meet demand. In fact, backlogs of commercial aircraft at major companies are at record heights.
“To meet this demand, companies need to double their production capabilities,” said Stephen Beecher, AMRC’s senior sector engagement manager for aerospace. “But this isn’t economically viable with traditional manufacturing techniques or manual layup approaches since you’d need much more manpower and ten times the floor space.”
However, with advanced digital technologies, automated processes and robotics, manufacturing can achieve more with less. The AMRC is focusing its research efforts on how the latest technologies can help aerospace and defense (A&D) manufacturers to make faster, more cost-effective, safer and sustainable products.
Manufacturers need to create a digital thread across their entire operations and ecosystems – and the Dassault Systèmes’ portfolio will facilitate that.
Building on a successful collaboration
The AMRC has a long history of working with Dassault Systèmes, having developed a new approach to the Factory of the Future, including the DELMIA Factory of the Future Showcase at the AMRC Cymru in Wales and the Airbus DAWN and Smarter Test Programs.
The new collaboration will see the AMRC leverage Dassault Systèmes’ full portfolio of cloud-based solutions, including CATIA for design, ENOVIA for project management, SIMULIA for simulation and DELMIA for manufacturing operations management all encompassed on the 3DEXPERIENCE® platform. They will also work together to define how virtual twin technology can drive new levels of efficiency and intelligence. These developments will be aligned with the AMRC’s strategic pillars including sustainable manufacturing, industrial digitalization, supply chain resilience, future products and processes, and culture.
“Our renewed partnership will enable us to deliver on our mission to achieve even better outcomes for the industry,” Beecher said. “This is crucial as the A&D industry moves away from traditional manufacturing techniques and a reliance on manual labor, and towards a future that capitalizes on automation and robotics. Manufacturers need to create a digital thread across their entire operations and ecosystems – and the Dassault Systèmes’ portfolio will facilitate that.”
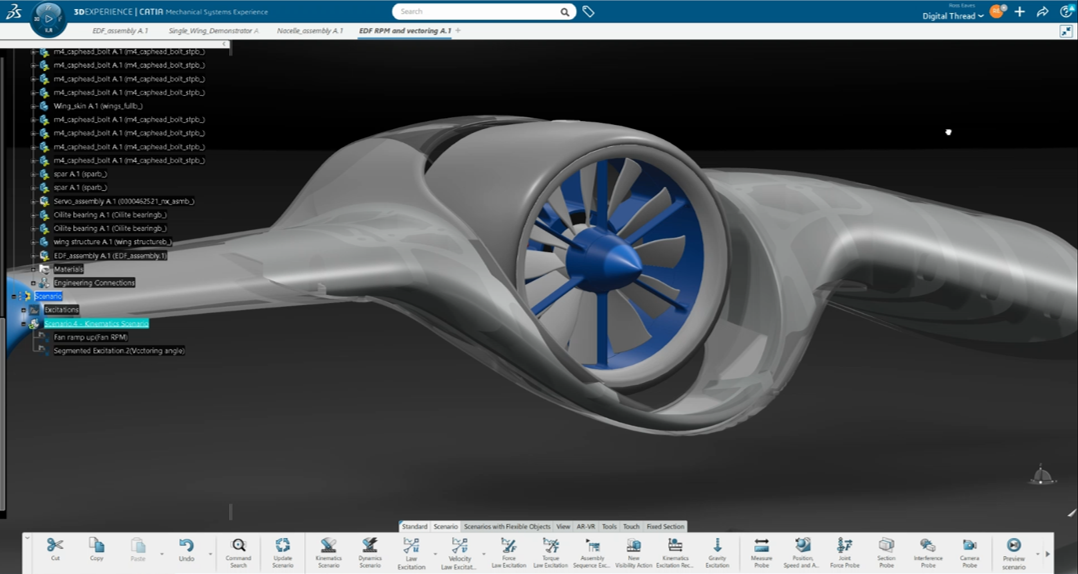
A digital thread from design to production
Dassault Systèmes’ technology will allow the AMRC to capture data from all stages of the manufacturing process – from initial design to production and beyond – building an end to end digital thread. The research center will then use this data to create virtual twins – advanced, fully functioning models of entire manufacturing processes and systems – enabling it to evaluate new approaches that may prove transformational for the aircraft manufacturing industry and its suppliers. For example, stakeholders will be able to improve the operation and maintenance of assets and extend their lifespan, understand potential disruptions from the supply chain and ensure compliance with new regulations.
To develop and refine its digital thread expertise, the AMRC is using an uncrewed aerial vehicle (UAV) demonstrator as a testbed. It capitalizes on the 3DEXPERIENCE platform using CATIA for modeling, kinematics and model-based systems engineering (MBSE - CATIA Magic) structuring with connected electrical schematic design, and SIMULIA for simulation modeling (PowerFLOW) and to explore the use of executed process composer studies.
“Our Design and Prototyping group have collaboratively designed and developed a fixed tandem wing concept UAV concept using Dassault Systèmes solutions,” said Ross Eaves, design engineer at AMRC. “The digital thread provides a single source of truth throughout the development workflow, including requirements capture with parameter-driven design changes for automated revisional structures.”
Exploring the concept of the digital thread and becoming more data driven, the AMRC accelerates its collaborative development process and drives product innovation efficiently.
“It’s all well and good capturing data, but the important part is what you do with it – you must be able to understand it and make good use of it,” Beecher said. “Because all Dassault Systèmes’ solutions speak the same language, we can optimize how we work with data. We can flag issues or nonconformities at the earliest stage of production and improve consistent levels of quality as a result. Moreover, by leveraging digital twins, we can make changes to the process and see how that influences downstream and upstream processes. Having a digital thread across all operations allows us to see the bigger picture.”
Virtual twin technology is transforming the aerospace manufacturing sector by changing the way products are developed at every stage of the production process and by fostering collaborative innovation among stakeholders to create new, ecosystem-driven business models. Driving efficiency and intelligence, the AMRC will also use it to train a new generation of engineers.
“The future workforce needs a broader range of skills,” Beecher said. “In the past, a mechanical engineer had a specific skill set and worked independently. We are now seeing multidisciplinary teams collaborate and work together to design, test and operate aircraft. Our AMRC Training Centre provides over 300 apprentices with a broad spectrum of skills focused on metals, machining, computer-aided design (CAD) and leadership development. Having Dassault Systèmes technologies as the overarching solution to support this is a game changer. It provides industrial relevance to our training and will equip the workforce of tomorrow with the capabilities that the industry really needs.”
Discover more about the Ready for Rate industry solution experience.

Focus on the University of Sheffield / AMRC
Every day, researchers and engineers at the University of Sheffield Advanced Manufacturing Research Centre (AMRC) work with companies of all sizes — including SMEs, start-ups and large-scale manufacturers — to help them improve their productivity and save time, money and energy. The center uses its research to develop bespoke improvements for each company, based on their budget and requirements. This might mean incremental changes to processes or a complete overhaul, making the most of the latest technologies.