AMF
Italian fashion accessories supplier AMF needed a technology platform to deliver transparency across the product lifecycle and streamline the creative process to make its own processes more efficient and environmentally friendly. The 3DEXPERIENCE platform on cloud and its Perfect Consumer Product solution help AMF to improve internal collaboration and work more effectively with its high-fashion clients to bring new ideas to life.
Sustainable accessories in fashion
AMF, Italian maker of metal and non-metal accessories for garments, shoes and leather goods, works with the most famous global fashion brands. The company’s mission is to develop and make any fashion accessories using sustainable methods and deliver them worldwide within three weeks. The company manages the entire product development lifecycle and is committed to creating the finest, most innovative finishes in the industry, led by its four pillars: quality, creativity, service and sustainability.
“We work with the world’s most iconic fashion brands and our success is built on and driven by our four pillars,” said Andrea Vittadini, COO of AMF. “Not only do we produce the highest quality garment and leather good accessories, but we have very strong internal design capabilities. Our clients come to us for ideas. They know that we have the widest product portfolio and that we can deliver everything they need to put the finishing touches on any particular item in the shortest timeframe. We also pride ourselves on our forward-thinking production methods. We’ve invested substantially in being more sustainable across our business.”
In the same way that an AMF accessory enriches a product, the company wants to make a positive impact on our planet, too. It’s doing that by replacing the most polluting steps in its production processes with eco-friendly alternatives and inventing ways to make better use of natural resources. AMF’s cutting-edge galvanic plant in Bassano del Grappa, Italy reuses more than 97% of water in its closed-circuit system and purifies the air leaving its pipes so it’s cleaner than the air coming in. The production line is completely automated to keep people safe from potential hazards. And the company’s lab tests product performance and proactively detects and eliminates harmful chemicals.
“Our products should last a lifetime, so we’re making big efforts to make all the surface treatment we do as sustainable as possible while achieving the same level of quality,” Vittadini said.
ISO9001 certified since 2004, AMF is now working on an environmental certification, pursuing traceability across every aspect of the product lifecycle. As part of this, the company takes advantage of the latest technologies, including the 3DEXPERIENCE© platform on cloud, to achieve even greater efficiencies across its product development processes, enhance collaboration and continue to distinguish itself in the market.
“Our pillars are a moving target and we must continue to develop,” Vittadini said. “We adopted the 3DEXPERIENCE platform to modernize the way we store and organize our data, empowering us to retain and reuse our knowledge and designs so that we can effectively modify products to make new ones. We also wanted to foster collaboration inside and outside of the company, adopting new ways to get closer to our clients and facilitate the creative process.”
Designers can meet up, collaborate and sketch in 3D with the 3DEXPERIENCE platform on cloud. We’re breaking down the barriers that limit creativity.
One system, one provider
AMF already used CATIA to manage its design processes, so the 3DEXPERIENCE platform was a natural step in the company’s digitalization strategy. Enhanced collaboration was a key objective, and the company also wanted to store all its data in a central environment and have a single platform that delivered all the functionality it needs, both now and in the future.
“We previously used two or three solutions to manage the processes in our technical office and we wanted to move everything to a single solution from a single supplier,” said Paolo Gallio, Senior Engineer of AMF. “Our aim was to interact with only one company in terms of data and software management and we found the answer in Dassault Systèmes and the 3DEXPERIENCE platform.”
The company opted for a cloud implementation to suit its immediate and longer-term business needs.
“We wanted to slim down the data flow in our internal data server and reduce overall costs,” Gallio said. “We chose 3DEXPERIENCE on cloud to achieve this and ensure the increasing amount of data we produce is protected. Now, we can work on and save our products in the cloud and foster true collaboration inside and outside of the company.”
AMF worked with its long-term technology partner and Dassault Systèmes solutions specialist Nuovamacut to handle the implementation.
“We have worked with Nuovamacut for many years based on their professional approach,” Gallio said. “They deliver a combination of values, qualities and ethics that align with our business goals. Their role was essential in the success of the implementation. They guided us in our choices and were very helpful in answering our questions and helping us to get the most from the platform.”
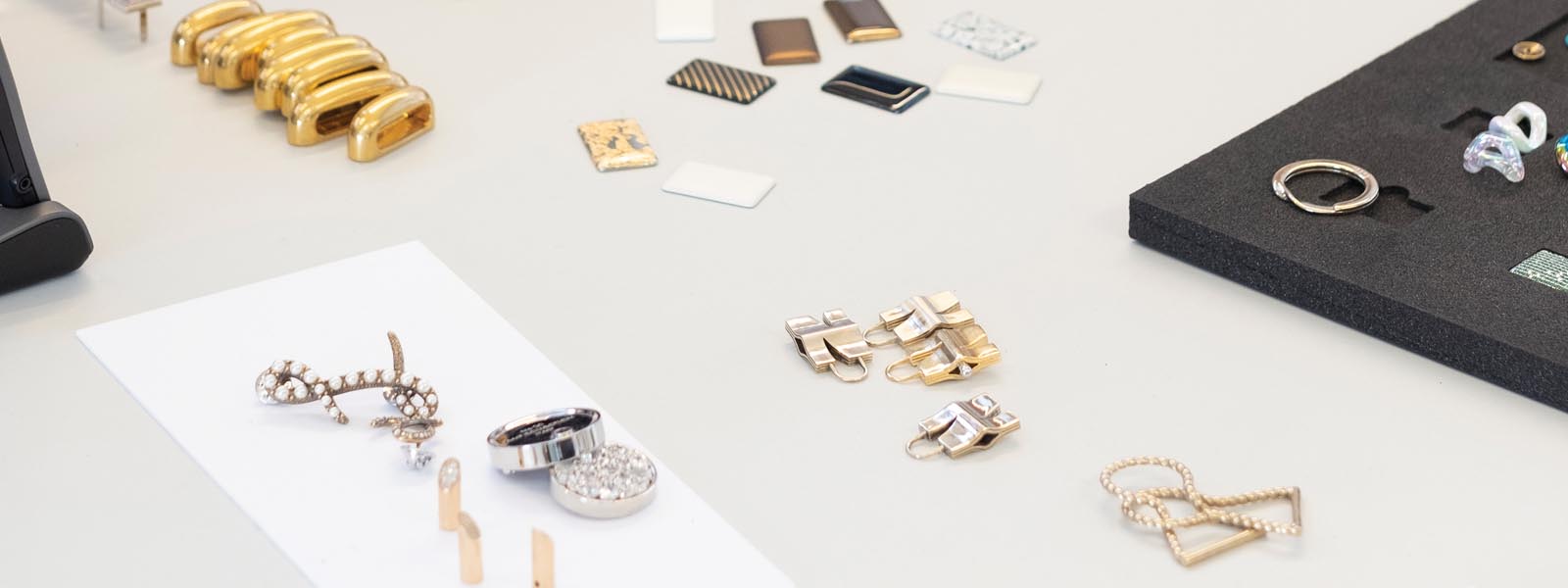
Bringing together creative minds
Designers use the 3DEXPERIENCE platform to do live sketches and renderings on a tablet and work on new ideas in close partnership with clients.
“When we’re discussing a new project with a client, it’s so valuable to be able to do quick sketches with the same freedom as if we were drawing by hand to visualize new ideas,” Gallio said. “It’s really easy to collaborate on one screen and for multiple stakeholders to interact with the design.”
“Collaboration has undoubtedly been the biggest business impact of the 3DEXPERIENCE platform to date,” Vittadini added. “Our new setup allows us to have more engineers and designers collaborating on projects across our offices and come up with better designs faster.”
With all design and engineering data now managed in a single environment, AMF can also retrieve design information from previous projects to speed up development.
“Compared to our previous file-based system, it’s also now much easier for us to search for, open up drawings and explore our work,” Gallio said. “We can access and reuse information from thousands of previous designs and our knowledge becomes a real asset.”
Using ENOVIA, multiple users can work at the same time on a single collection, taking advantage of secure collaborative spaces, which give role-based access to collate, view and edit all documents and models related to each specific customer project. Designers also appreciate the ability to see all related documents within a product context so they can see the full picture when working on and referring back to projects.
“We can open products in exploration/preview mode and see all the documents that they’re linked to,” Gallio explained. “It provides a very good overview and keeps everything together.”
We can work on and save our products in the cloud and foster true collaboration inside and outside of the company.
Tradition meets innovation
When AMF opened a new design office in Paris, its aim was to be at the heart of the action with its high-fashion clients.
“In many ways we’re an extension of these brands, so the goal of the Paris office was to bring the brand style teams closer to our designers and engineers, and draft their ideas in real time,” Vittadini said. “Many creative houses stick to their heritage and work in traditional ways, sketching drawings on paper. Having the office near them means we no longer have to scan in drawings and keep going back and forth. Designers can meet up, collaborate and sketch in 3D with the 3DEXPERIENCE platform on cloud. We’re breaking down the barriers that limit creativity and helping to influence and shape each other’s futures. The fashion houses are changing their approach to work better with us. Our innovations have a real impact.”
Even when restrictions related to the COVID-19 pandemic put limits on in-person meetings and visits, the 3DEXPERIENCE platform on cloud helped AMF to stay connected with its clients and deliver the same, high-quality, collaborative service they have come to expect.
“The reaction from customers is positive, especially now they can’t travel to us as readily,” Gallio said. “We do far more digitally and have remote virtual meetings in place of physical ones. The 3DEXPERIENCE platform has really transformed our approach. Even when we need to keep our distance, we can still interact closely.”
Designing for fast production
Whether it’s a rivet, button, clasp or buckle, AMF’s typical design cycles take anything from a few hours to several days, depending on the complexity of the product being created. All final products are then delivered within three weeks. AMF uses CATIA’s sophisticated design capabilities on the 3DEXPERIENCE platform to get designs right first time. Designers have a rich set of tools to develop designs from initial sketches to final 3D models, all with extreme precision. AMF then uses ENOVIA to manage the entire product development lifecycle upfront and keep on top of tight project schedules. ENOVIA also helps AMF’s technical office ensure the materials they use comply with the business’s environmental and sustainability objectives and streamline inventory management to use materials as efficiently as possible.
“Compared to the past, we now work in a single environment starting with the initial sketch on the platform, which we then transform into 3D models,” Gallio said. “We can then work on colors, materials and finishes with real-time visualization and photo-realistic rendering. The platform combines the best of styling with the rules of engineering. It supports us to create products that can be produced efficiently and sustainably and launch them to market faster than ever, some in a matter of only hours or days.”
This approach helps AMF improve product quality and better manage customer expectations with accurate updates throughout the product development process.
“When we develop the 3D models, we’re also taking into account the bill of materials and everything related to the manufacturing process,” Gallio said. “It means that we can generate accurate quotations quickly as we’re already near to a final solution by that point and know exactly what’s going to be involved.”
In future, the company plans to expand its use of DELMIA and take advantage of the virtual twin experience to manage and further optimize its operations from design through to manufacturing, including molds, dies and tool creation to final production.
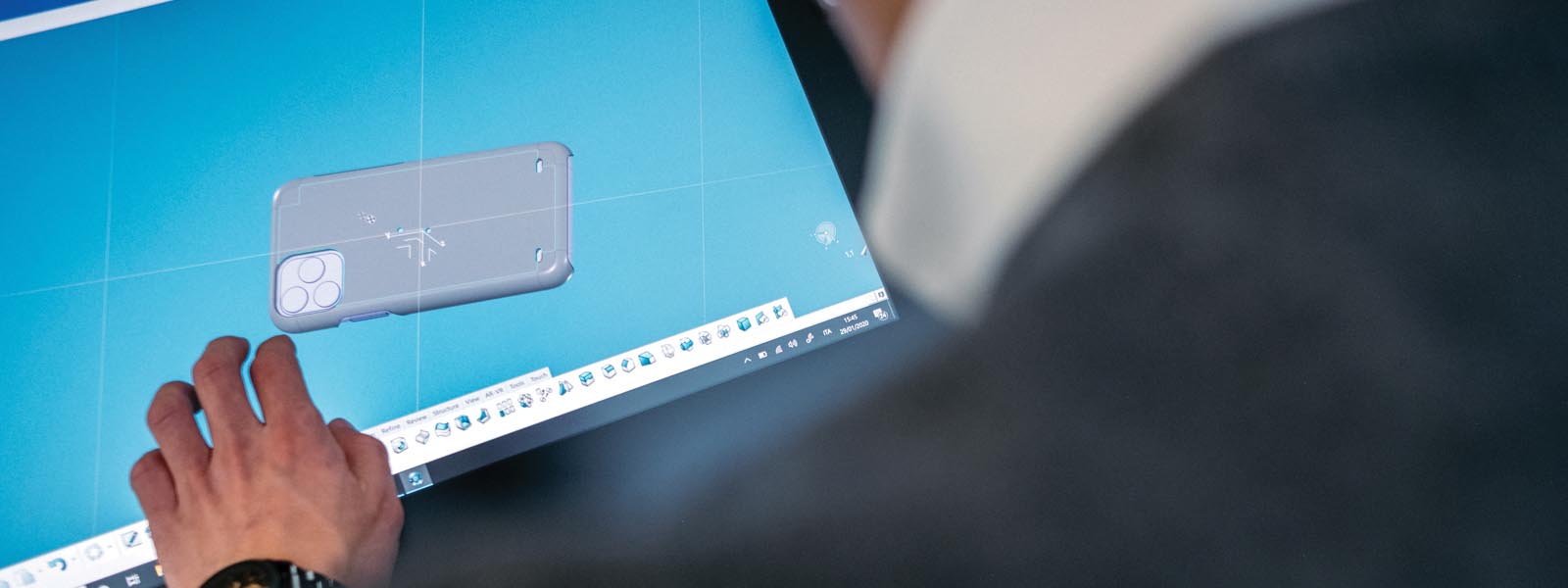
Pursuing transparency
Beyond the glass walls in its galvanic plant, which allow visitors to clearly see the inner workings of the factory for themselves, AMF is also using the 3DEXPERIENCE platform to become even more transparent across its product development processes.
“We don’t have lots of standardization in our industry,” Vittadini said. “We grew in a culture of making new products all the time, constantly. In our case, the goal was not to standardize but to be creative and fast. One thing we’re doing with the platform is some form of standardization with key components. That fits in with our sustainability goal too. Instead of testing physical products after manufacturing, we are using the platform to move towards virtual testing.”
AMF hopes that by showing the industry how it is continuing to innovate and transform its production processes, it will inspire others to follow suit.
“We’re constantly evaluating our contribution to our planet and pushing ourselves to create a better future,” Vittadini said. “Technology is evolving at such a rapid pace, shaping our workforce and reimagining our interactions with customers and suppliers. We must keep in step with the times. One of the keywords that defines AMF is innovation and, with the 3DEXPERIENCE platform on cloud, we can stay true to our goals and support brands to move to sustainable production at the highest level.”

Focus on AMF
AMF produces sustainable metal and non-metal accessories for the fashion and luxury industry, which adorn the products of the most famous international brands. The company is renowned for the quality of its products and customer service, from its exceptional, creative product development to its precise production and efficient worldwide after-sales technical support.
For more information: www.amfsnaps.com
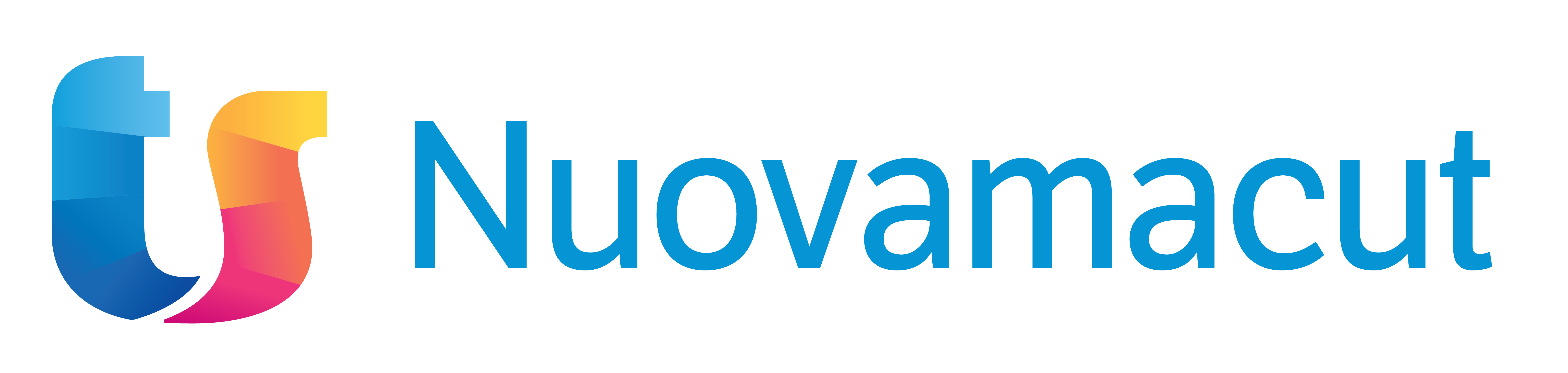
Focus on Nuovamacut
Nuovamacut is an Italian company and Dassault Systèmes partner with strong expertise in CAD, CAM, CAE and PLM. The company is active across Italy, supporting customers of all sizes and complexities, operating in different sectors ranging from the mechanical industry, design, and construction of molds, consumer goods, and technological equipment to aerospace, transport, planning, and design services.