3CON
The company adopted Dassault Systèmes’ 3DEXPERIENCE platform for virtual design, collaborative innovation and workflow management.
Delivering leading-edge technology for automotive interiors
While safety, fuel efficiency and reliability top automobile customers’ list of important buying criteria, interior design and ergonomics are not far behind. Today, car manufacturers and their suppliers offer a wide range of fabrics, accessories, and technologies that enhance the driver’s well-being and experience. Austria’s 3CON has built a solid reputation as a leading global manufacturer of automotive interior machinery since it was founded in 1998 by Hannes Auer.
“Our laminating machines are used to produce door panels, instrument panels and center consoles equipped with a variety of materials, fasteners, handles and lighting,” Hannes Auer, CEO at 3CON said. “Over the years, we have developed our processes beyond lamination to include joining, anti-squeak and edge folding technology, thereby enabling us to cover all techniques related to the manufacture of interior parts. Our clients are Tier 1 suppliers that include Yanfeng, Dräxlmaier, SMP and Grupo Antolin and car manufacturers that have their own production facilities,” Auer said. In addition to Austria, 3CON has production sites in China and North America to cater to the local requirements of customers in these countries.
“Our clients look for reliability in our machines and in their vendor,” Auer said. “Our after-sales service is characterized by our swift response, which reduces machine downtimes at the customer site to a minimum. This differentiates us from our competition.”
“Our clients also appreciate our innovative spirit,” Auer said. “Our Exact Shape Lamination (ESL) technology, for example, is one of 3CON’s innovations that allow companies to manufacture better quality parts while generating savings of up to 50% because they use fewer materials such as glue, leather or other textiles. We’ve integrated the edge-folding process in the ESL machine, eliminating the need to have separate machines for each process.”
“In a fast-moving automotive industry characterized by ever-shorter lead times, no compromises are acceptable. With the 3DEXPERIENCE platform, design engineers from our three sites can work with one another throughout product development to accelerate cycle times.”
Collaborative innovation
3CON needed to improve collaboration between its different sites and accelerate the process of transforming concepts into sturdy, efficient equipment. The company chose Dassault Systèmes’ 3DEXPERIENCE® platform because it wanted to allow globally dispersed project stakeholders to access a centralized data structure to improve collaboration and innovation. Another reason was 3CON’s desire to shorten lead times while maintaining the high quality of its products.
“They can rapidly try out new ideas because the system is fast and easy to use, enabling them to test more design iterations in any given amount of time,” he said. “Design teams can also exchange information with NC programmers while managers monitor project status, all in real-time,” Auer said.
“With the 3DEXPERIENCE platform, we also have a flexible and open environment that enables us to collaborate and exchange information with our clients,” Christian Mayr, CTO at 3CON added. “In this way, they can easily provide us with the data that forms the basis for the customized machine we will manufacture for them before design begins and throughout the development process.”
“In addition, the platform enables us to be more agile in the way we work since information can be accessed at any time and from anywhere,” Auer said. “This enables us to optimize the use of our available resources. For instance, if one site lacks the manpower to finish a job, another site can jump right in to fill in the gap,” he said.
TECHNIA and Dassault Systèmes provided 3CON with assistance during the integration of the 3DEXPERIENCE platform. “After implementing the hardware and software on the server and client-side, we provided 3CON with users and administrators training,”
Andreas Flottman, sales manager South Germany, TECHNIA explained. “We also taught them how to configure their bill of materials (BOM) with ENOVIA,” he said. “TECHNIA is a flexible, client-oriented partner in PLM consulting,” Auer said. “Its in-depth expertise with the 3DEXPERIENCE platform and its application ENOVIA was very valuable to the success of our installation. Along with Dassault Systèmes, both companies have been able to help us solve even the most complex challenges.” Mayr added: “Moreover, the environment is so well designed and structured we were up and running in only three weeks.”
Integrated Platform
“All the apps we need to design and build our machines are available on the 3DEXPERIENCE platform - CATIA for 3D design, DELMIA for 2.5 to 5-axis NC programming and simulation and ENOVIA for project management - and most importantly, they are all integrated,” Daniel Schöpf, COO at 3CON added. “This means we don’t have to deal with the inconvenience of performing costly and time-consuming data conversions that can delay the release of a new machine to market. We have a streamlined process from design to commissioning,” he said. “There is data associativity between the different applications. If we make a change to the design, it is automatically reflected in the NC program.”
With the 3DEXPERIENCE platform’s ENOVIA app, 3CON is more efficient at managing workflows because the system makes sure that design approvals are completed at the right time and by the right person. “We can assign roles in ENOVIA and define who is authorized to do what, like modifying certain standard parts,” Mayr said. “ENOVIA keeps track of any design changes made along the way, providing us with a clear change management scheme that we can refer back to whenever needed.”
End-to-end cost control
One of 3CON’s major challenges is cost control. “In the past, if projects were going over budget, very often we would realize this late in the process, at the production or purchasing stage,” Auer said. “This made it difficult to make adjustments and still stay on budget and on schedule.”
“With ENOVIA, we can assign non-geometric metadata such as material and production costs or material delivery times to our parts or assemblies in our BOM, which enables our engineers to monitor in real-time, if projects are on track budget-wise from the earliest design stages,” Schöpf added.
3CON uses the 3DEXPERIENCE platform’s design and visualization apps during the sales process to convince prospects that it has the best solution to their needs. “Machine concepts are modeled in a virtual environment providing prospects with a clear view of what we propose before they place their order,” Schöpf said. “They can make informed decisions and additional requests at this early stage, which are easier to implement than if we had to make the changes further down the line.”
“Once we have their approval, we begin the design process in which multiple disciplines from different continents work together on the same assembly, contributing their expertise and exchanging ideas,” Auer said. To cope with the increasing complexity of their machines, 3CON uses a modular approach to design. “Modularity accelerates the development cycle of a new machine,” Auer said. “We capitalize part geometry from previous projects in the 3DEXPERIENCE platform with ENOVIA, resulting in a catalog of standard parts that can be reused in the development of new machines. Because machines are tailored to customer specifications, if a standard part does not fit the bill, the flexibility of the 3DEXPERIENCE platform and its CATIA design application enables us to engineer new parts and use them as well.”
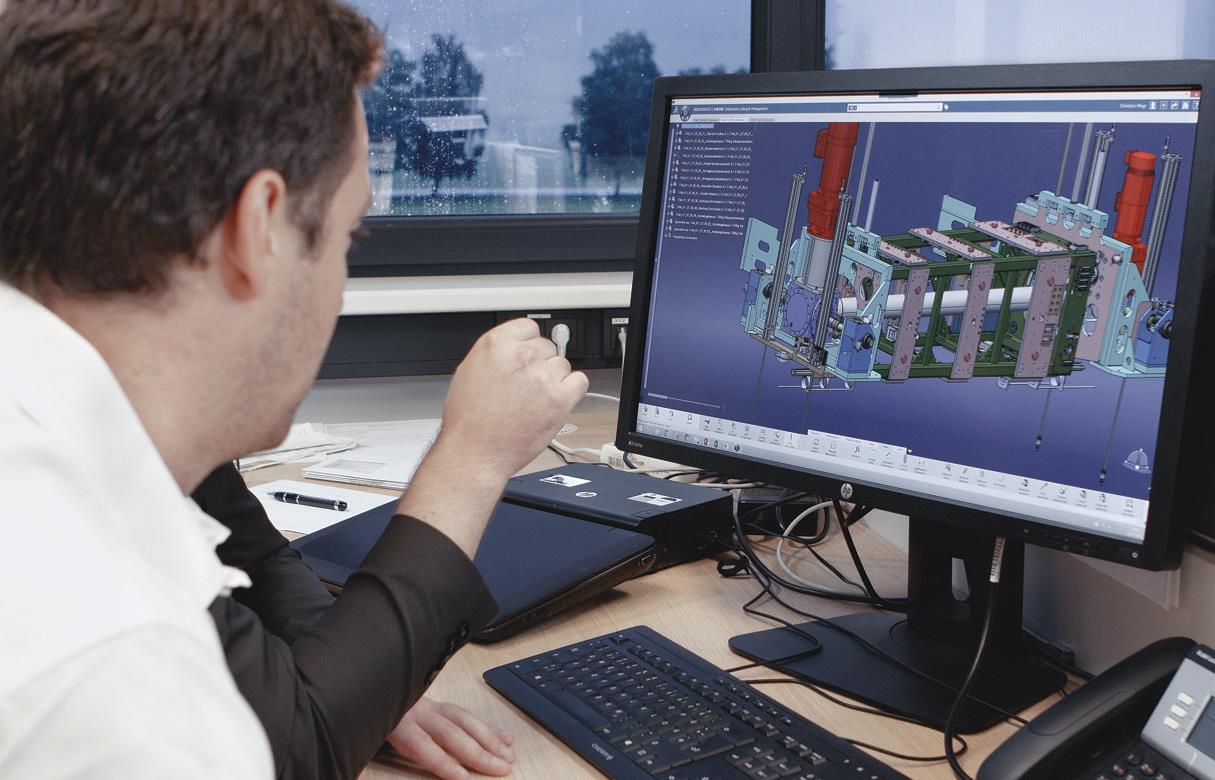
30% productivity increase
Engineers need to work on large assemblies that are often linked to other assemblies. This sometimes causes performance issues that can slow them down. “One of the benefits with the 3DEXPERIENCE platform is the ability to visualize and work on huge assemblies with a performance level never achieved before,” Mayr said. “One of our most recent experiences involved the development of a thermoforming vacuum lamination machine, which is comprised of many large subassemblies. Thanks to the system’s excellent performance, more than 20 people were able to simultaneously access and work on these assemblies, which improved overall productivity. We are now more effective and faster,” Mayr said. “Due to high user acceptance, the benefits of standardization and the enhanced release process, we’ve cut design time by 30% while simultaneously improving the quality of our designs,” Auer added.
Assembly workers have access to the 3D geometry from the shop floor, which improves their understanding of how a machine should be assembled. “If an issue is discovered at this stage, they can use redlining to indicate where the problem is and add comments if necessary,” Auer said. “This can be viewed by the designer in real-time, who can proceed with the necessary design adjustments.”
“The people on the shop floor can interactively document changes or lessons learned in the 3DEXPERIENCE platform and the different roles are immediately informed that these modifications were made. Everyone is always up to date,” Schöpf added.
Industry Solution Experiences
3CON uses the following Industry Solution Experiences from Dassault Systèmes to help them meet their development challenges: Bid to Win: Enables teams with industry-proven tools and processes to analyze opportunities, win optimal new business, then design, engineer, validate, manufacture, and deliver on target to customers’ satisfaction. Single Source for Speed: Enables companies to manage their entire product development process – from idea to design, production and servicing – across all geographic locations.
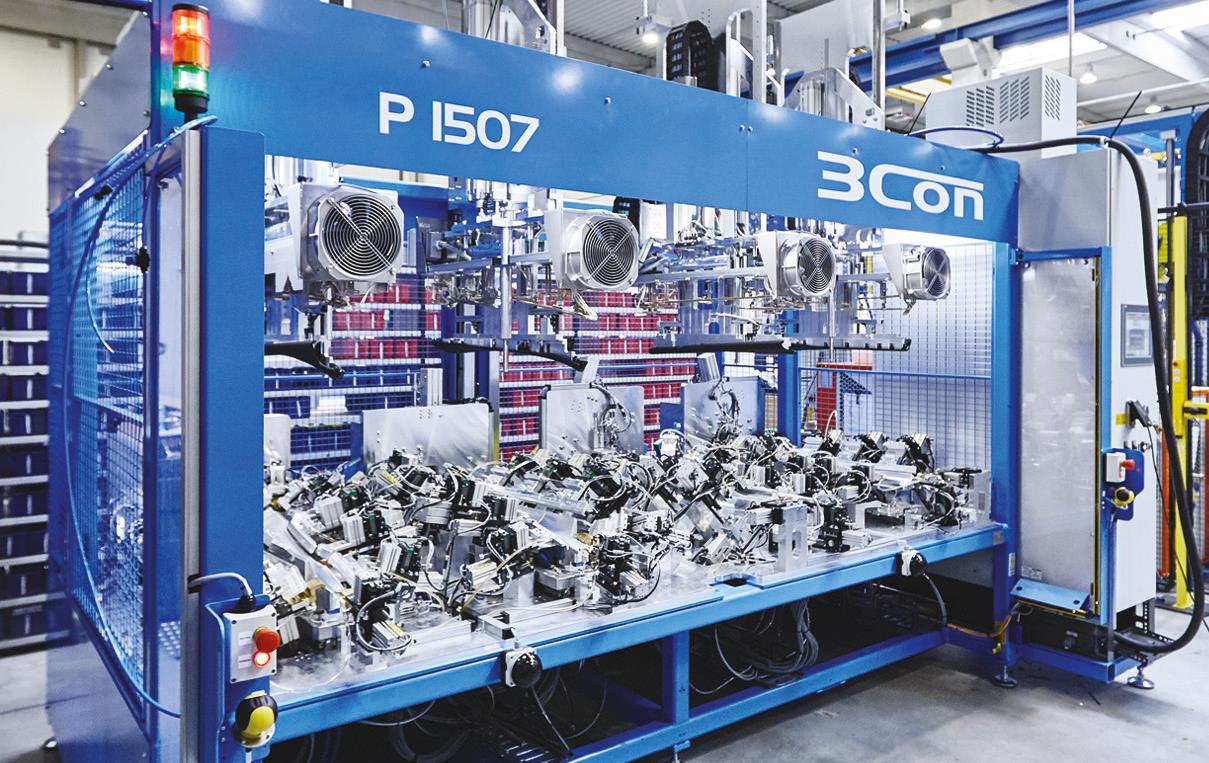
Start-up phase divided in half
Once a machine is assembled, it is tested by application engineers on the shop floor to see if it works correctly and meets customer requirements. When approved, it is disassembled and re-installed at the customer site during the start-up phase.
“Commissioning technicians have access to all knowledge databases on the 3DEXPERIENCE platform to check machine parameters like clearances or temperatures, which helps them during installation,” Auer said. ”Any issues encountered at this stage are documented on the 3DEXPERIENCE platform so that designers can correct their designs on subsequent machines. Because the issues were corrected upstream, new machines can be installed faster. As a result, we have been able to reduce the assembly start-up phase by up to 50%,” Auer said. “In general, enabling our technicians on the shop floor and application engineers to visualize a complex system in a virtual environment has put us on the road to paperless production,” Schöpf added.
Non-technical people can also visualize machine geometry with ENOVIA 3DLive, which provides a “virtual workspace” to view product data in an immersive 3D environment. “For our buyers to accurately assess machine costs, they need a visual representation of the components,” Auer said. “The 3DEXPERIENCE platform and its ENOVIA 3DLive app are ideally suited for this purpose.”
Future trends
In a hyperconnected world where the Internet of Things continues to expand, 3CON machines must include the latest innovations to maintain their competitive advantage. “The 3DEXPERIENCE platform can serve as the foundation to capitalize and analyze all the information generated by 3CON machines installed in the field, information that will not only improve maintenance but also future designs,” Auer said.
In the future, 3CON plans to use the 3DEXPERIENCE platform as the company’s central database for capacity management to help ensure that its IT resources are correctly sized to meet its business requirements. “We are also interested in pushing the virtual reality facet even further by delivering high-end 3D virtual experiences to our sales force and customers,” Auer said. “Dassault Systèmes’ 3DEXCITE app is ideal for this. Finally, we plan to use DELMIA to virtually simulate robots in action to make sure they’re optimally positioned before physically installing them on the assembly line.”

Focus on 3CON
World-leading reference for manufacturing equipment for the automotive interior industry.
Products: Door panels, instrument panels, consoles and pillars as well as after-sales services
Revenue: 40 million Euros (2015)
Headquarters: Ebbs, Austria
For more information: www.3con.com
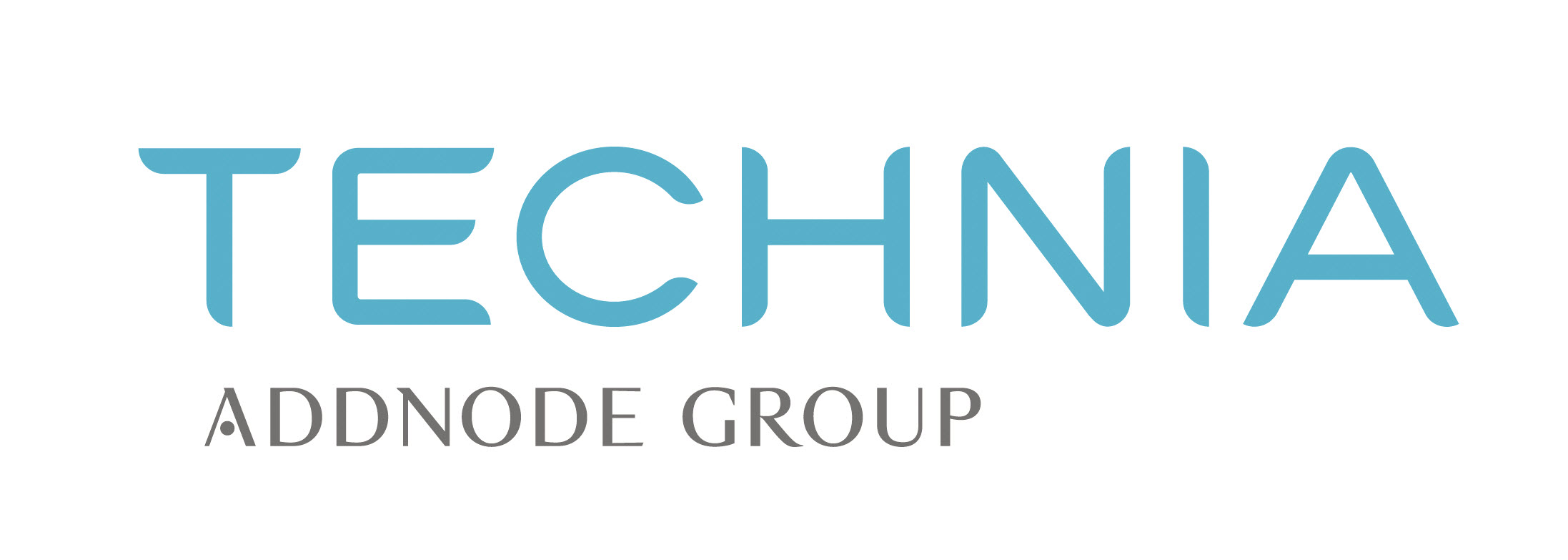
Focus on TECHNIA
At TECHNIA, we pave the way for your innovation, creativity and profitability. We combine industry-leading Product Lifecycle Management tools with specialist knowledge, so you can enjoy the journey from product concept to implementation. Our experience makes it possible to keep things simple, personal and accessible so that together we transform your vision into value. With over 30 years’ experience, more than 6000 Customers worldwide and world-class knowledge in PLM & Intelligent Engineering, we work together as true partner and extension of your team to create an exceptional PLM experience. Our 650 people strong teamwork from 27 locations around the world, across vertical industries, delivering a premium service with a global infrastructure and a local presence. We adopt the latest technology and agile methodologies so, even as technology changes, our relationships last a lifetime.