Prioritizing sustainability in manufacturing
Virtual twin technology is transforming manufacturing by changing the way products and services are developed in three significant ways: making sustainability and carbon footprint reduction an imperative; making the experience of a product or service the primary focus; and reinventing the way stakeholders work together to create new business models that include the entire ecosystem.
UNTIL NOW
Manufacturing was all about the product
FROM NOW ON
Manufacturers will put sustainability first
Making sustainability an imperative
Manufacturers are actively seeking new ways to manage products and services over the entire lifecycle. There are two main reasons for this: bring consumers new experiences and new solutions to climate change. This means rethinking every stage of the process, from design to usage and end-of-life management. Virtual twins have a critical role to play in accelerating sustainability. They help companies reduce costs, resources and carbon footprint, and can support disruptive innovation and agile, customer-centric, more circular business models. Virtual twins help shorten product development times and improve manufacturing quality, as well as support more efficient use and recovery of resources.
Reducing time-to-market and risk in complex projects are key reasons why virtual twins have been used in developing 85% of the world’s electric vehicles, more than 75% of global wind power projects, and breakthrough sustainability pilots such as the world’s first solar airplane.
This transformation impacts nearly every business across all sectors; a battery startup like Olenergies and a paperboard producer like Metsä Board share the same imperatives in terms of sustainability and can benefit from virtual twins to address their needs.
Olenergies
The 3DEXPERIENCE Cloud platform enables cobalt-free lithium battery manufacturer Olenergies to manage everything from customer collaboration to design, manufacturing and supplier integration. The French startup can accelerate engineering and validate new solutions, while reducing resources and project execution costs. Virtual twins created in the platform reduce the need for people and physical prototypes to be shipped around the world, since all employees, partners and suppliers can seamlessly and securely collaborate in real-time, no matter where they are located.
Metsä Board
Facing customer demand for more sustainable packaging, Finnish company Metsä Board, one of the top paperboard producers in Europe, needed an alternative to physical prototypes. To remove time-consuming testing procedures, Metsä Board used the advanced simulation technologies of the 3DEXPERIENCE platform to create virtual twins of its packaging solutions and rapidly compare their performance in simulated conditions against customers’ existing solutions.
Making experience the primary focus
As they become conscious of the environmental impact of their choices, companies must also take into account not just what a product is but how it will be personalized to meet customer demand. They must also consider how it will be used over its entire lifecycle, including product second life or end of life.
Viscon
Netherlands-based Viscon develops innovative machinery and complete production lines for the food and agro industries. To better serve their existing customers, as well as adapt their solutions to new markets, the company decided to digitally map their processes, from ideation to manufacturing to virtual commissioning to services. Using virtual twins created on the cloud-based 3DEXPERIENCE platform allows Viscon to improve their selling experience by showing 3D layouts of the configured modules and machines; this helps improves overall quality and decreases commissioning time.
Vertical Aerospace
UK aerospace and technology company Vertical Aerospace is aiming for its piloted, four-passenger electric aircraft – the VX4 – to achieve full certification and commercial flights by the middle of the decade. The company’s exacting standards require every component of the aircraft to be carefully and flawlessly manufactured and the 3DEXPERIENCE platform is helping their engineers and supply chain alike to design, test and validate each structure through virtual twins.
“The vehicle we’re developing is an all-electric battery powered aircraft. We’re seeing a massive transformation in the technologies that we’re starting to use. We started with an aircraft that is fairly heavily automated, so much of the pilot workload is done automatically, but the pilot is ultimately in the vehicle and able to take control.”
Michael Cervenka,
President, Vertical Aerospace
Reinventing the way we work together
The manufacturing sector is under pressure, reinforced by the COVID-19 crisis, to meet the expectations of a digitally advanced workforce. This requires adopting the new technology, tools and machinery that will define jobs in the years to come. It extends to the entire ecosystem of stakeholders, whose needs and demands must be taken into account at every stage of the production process. Thanks to virtual twins, companies can mirror their physical manufacturing value streams virtually, to quickly and cost-effectively create and test new concepts and ideas, and ultimately create a more customer-centric, agile and sustainable business model.
Meyer Werft
Leading cruise ship builder Meyer Werft used the 3DEXPERIENCE platform to build one of the first LNG-fueled cruise ships. Creating a virtual twin of a highly complex ship lets hundreds of different teams collaborate on design, production, operations and maintenance. The integrated, open 3DEXPERIENCE platform even enables Meyer Werft to automate selected design processes, and to integrate project data generated by legacy digital design tools used by its suppliers. This supports a smooth and gradual transition to a unified and integrated business experience.
Extending our use of the 3DEXPERIENCE platform is part of our ambition to more efficiently design and build innovative cruise ships. We aim to unify tools and processes across our sites. As we are in the construction phase for our first ship designed with the 3DEXPERIENCE platform, our partnership with Dassault Systèmes continues to strengthen to achieve this.
Geberit
To drive collaboration further by taking a data-based approach across all disciplines, Geberit, a Swiss manufacturer of sanitary products, adopted the 3DEXPERIENCE platform to standardize its ceramics development approach. The company created a virtual twin of its manufacturing equipment and buildings in order to simulate the trajectories of its machines when installing and moving them to ensure they work. In some areas, it also simulated the machinery, including robot pathways, to avoid any errors in the production process.
Having a single platform helps Geberit launch new products more quickly, as their mold designers can explore a variety of ideas with the 3D data model. This allows them to come up with the best result early in the product development phase, avoiding the need for costly and labor-intensive physical prototypes. External product developers and ceramic experts across Europe can also use these 3D models to produce the molds. Geberit can now identify potential problems early on and avoid production reruns that can increase waste and drive up costs.
Our partnership with Renault
Indeed, virtual twins on the 3DEXPERIENCE platform are enabling the transformation of the manufacturing industry. In 2021, RENAULT announced their “Renaulution” approach to develop programs for new vehicles and mobility services. The 3DEXPERIENCE platform supports these initiatives through real-time sharing of all product-related data throughout the product life cycle, as well as managing the virtual twins of its diverse product configurations.
In the race to decarbonize, automakers are under pressure to accelerate time-to-market of electric vehicles. Virtual twins are helping Renault make a strategic shift from a product to a technology, services, and energy enterprise platform.
Renault will deploy the 3DEXPERIENCE platform on the cloud to more than 20,000 employees in vehicle development functions such as design, product engineering, industrial process engineering, parts, and materials purchasing, costing and quality. The platform will provide real-time access to the same systems and software, 3D modeling and simulations across the world. The large-scale collaboration leveraging virtual twins promises to improve data sharing between different functions and increase agility within the company, while reducing costs and vehicle development time by approximately one year. Further, because the solutions are deployed on the cloud, Renault Group will benefit from continuous technological evolutions and functional enrichments, without having to wait for updates.
The 3DEXPERIENCE platform connects engineering to all disciplines in one digital company. We will gain agility, speed and effectiveness to develop new mobility faster than ever.
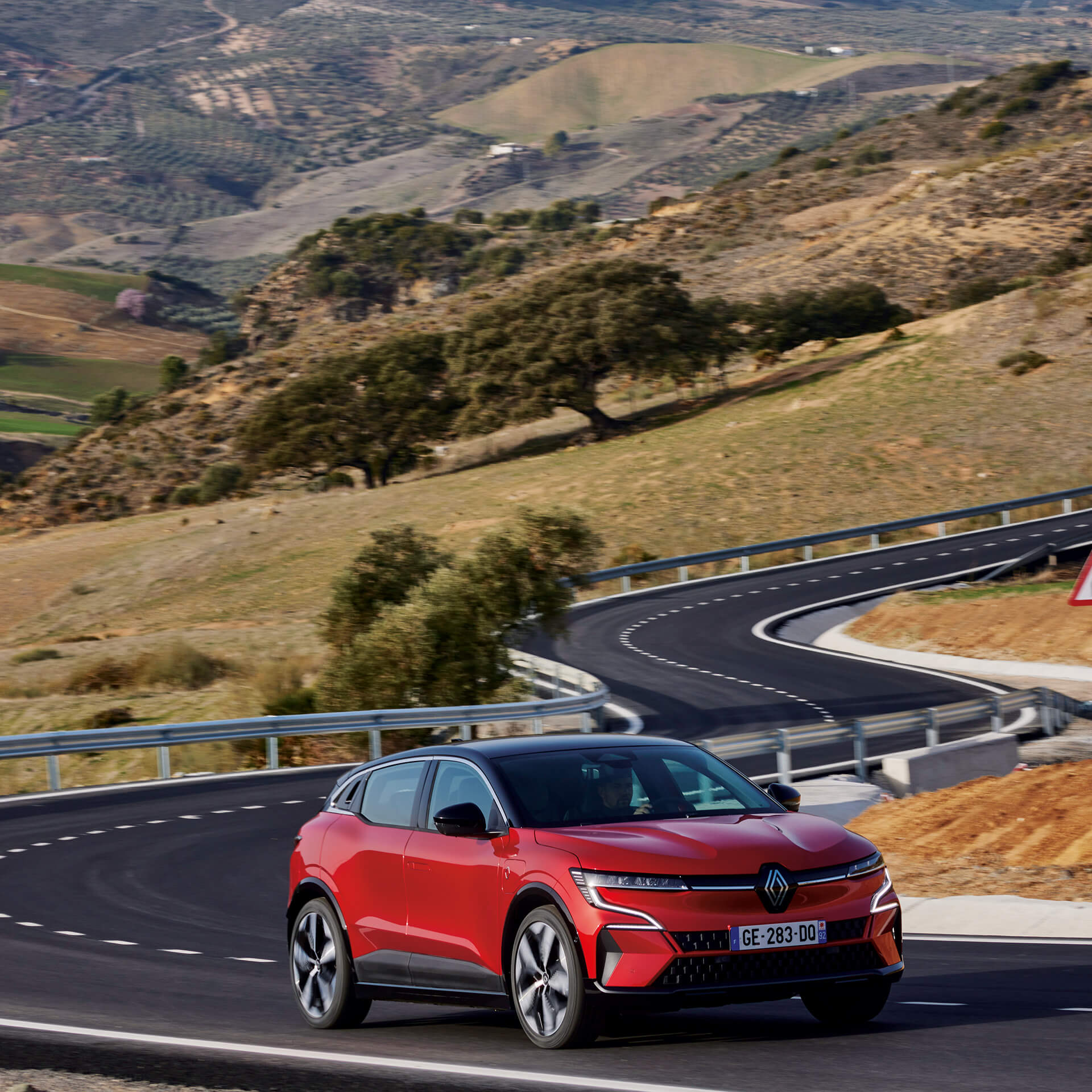