Less waste for the planet and its inhabitants
To help clients hit their sustainability targets, Dassault Systèmes has adopted an approach based on the 3 Ps of sustainability: people, planet and profit.
Amcor has more than 35,000 employees across 200 production sites worldwide. This 150-year-old company designs and manufactures a wide variety of packaging for the food and beverage industry, healthcare, homewares and personal care industries. As one of the leading manufacturers of plastic containers, Amcor is continually seeking ways to reduce the amount of material used in bottles, while keeping them strong and cost-effective to produce.
Throughout the process of designing a container, engineers use simulation to identify areas of strain, which indicate potential points of failure, helping them create lightweight, optimized designs. Reducing the amount of material by one gram or even half a gram in each of the billions of containers that Amcor and its customers produce annually represents considerable cumulative savings. Amcor’s customers enjoy lower production and transportation costs and reduced risk of product failure, while the planet and its inhabitants benefit from less waste in landfills. When designing its products, Amcor Rigid Plastic’s R&D teams use advanced digital engineering techniques enabled with CATIA, SIMULIA Abaqus and other Dassault Systèmes solutions, allowing them to move from concept to production in the space of just a few months.
Reducing weight from 44 grams to 36 grams
Billion (€14.7 billion): the potential contribution of AI by 2030, according to PwC
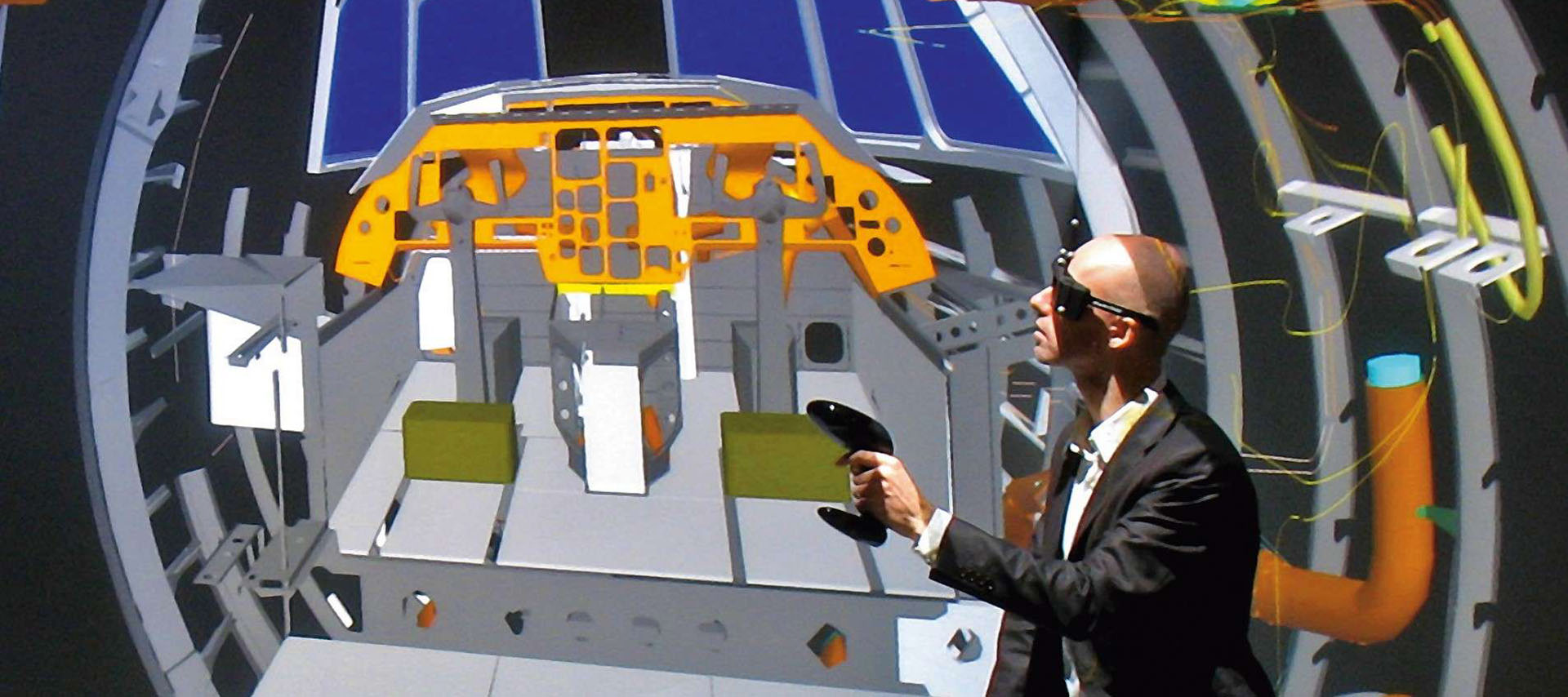
To help clients hit their sustainability targets by using AI to transform their manufacturing activities, Dassault Systèmes has adopted an approach based on the “three Ps” of sustainability: people, planet and profit. Concerning people, to train future generations, we need to transfer knowledge and expertise from today’s employees and devise technology to create experiences that foster innovation, to build a more sustainable future.
Companies need to adapt to digital technology and make their employees more autonomous. This goal can be achieved using multidisciplinary lifelong learning approaches, combining classroom study and practical work. With AI, augmented reality, and virtual reality, knowledge can be imparted more quickly and at the right time, making learning more intuitive.
Greater overall operational efficiency is good for the planet, the second P. By implementing lean practices throughout a product’s lifecycle, companies can minimize their environmental footprint. The aim is to assess, streamline and improve all operations: product design, engineering, the production process and the supply chain. Eliminating waste, unnecessary product movements, overstocking, errors and quality problems requires AI that is capable of learning. This technology is also proving its worth by reducing energy consumption: for example, smart grids that connect producers with consumers and predict consumption peaks help to optimize operations in real time.
The third P – profit – involves replacing supply chains with global value networks in which industrial partners join forces, redefining the way they contribute to attaining common goals. AI-based collaborative digital platforms allow companies to deliver sustainable, unique and outstanding experiences. AI systems can process data at lightning speed, assessing millions of potential scenarios. They allow companies to coordinate all of their stakeholders in a more efficient and agile way. Thus, companies can capture, standardize and analyze data to assess the environmental and social impacts of a given commercial activity, and define the key issues to ensure informed decision-making.
Morgan Zimmermann, CEO of NETVIBES-EXALEAD, a brand of Dassault Systèmes