Industrial methods for construction
Dassault Systèmes joined forces with Bouygues Construction, a global leader in construction and services, to accelerate the digital transformation of the construction industry. This involved leveraging a virtual twin to open new horizons with cloud-based, mobile-enabled approaches for the construction industry and its ecosystem.
UNTIL NOW
Craftsmanship was the main focus in the construction industry
FROM NOW ON
The industry is delivering tailor-made projects using industrial methods, including virtual twins
Using technology to address industry challenges
Construction is one of the oldest industries, and also one of the last to become digitalized. The working process has remained largely unchanged, and productivity has stagnated. Bouygues Construction believes embracing digital technology is the way to address existing challenges and support customization at scale.
Bouygues Construction tested this idea with a renovation project for an Art Deco swimming pool in Pantin, a Paris suburb. The company used the 3DEXPERIENCE platform to manage every element of the extensive transformation into a modern, dual-purpose facility for art and sports. This involved restoring the original swimming pool and constructing a new conservatory overlooking a landscaped garden.
Combining technical prowess, bold architecture and high environmental standards, the Pantin project offered an opportunity for Bouygues Construction to test new working methods and to improve collaboration among all stakeholders across the value chain using construction virtual twins.
Connecting the dots on the cloud
By bringing all data and information together in one place on the Pantin project, the 3DEXPERIENCE platform helped to break down communication barriers, identify potential construction issues and delays, and address them before they became bigger issues on site.
“The objective of the virtual twin is to deliver on the promise of construction before construction. It means we can adjust all the irregularities that we imagine, have a model that is really constructible, and avoid mistakes when we are on site. Once the design is finished and executed, questions are no longer raised about its integrity.”
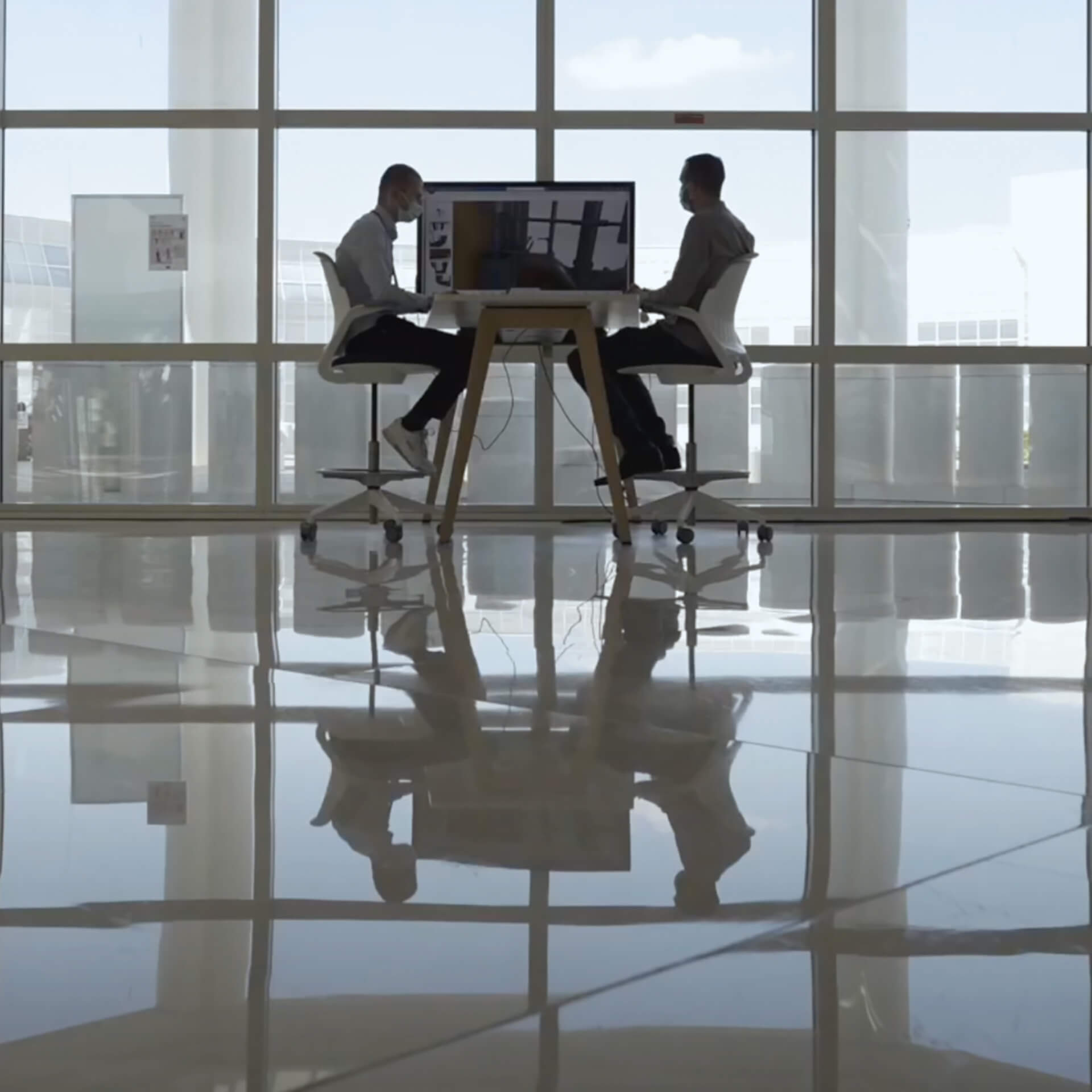
Supporting people and sustainability goals
Since all data related to the project is stored on the 3DEXPERIENCE platform, stakeholders across the value chain – from design to execution, operation and maintenance – were connected. This facilitated collaboration among remote workers, connected people across the organization and brought multidisciplinary teams together within a single environment.
Team members everywhere could connect remotely to the platform, benefiting from constant updates and knowing they were working with the most up-to-date version of the project.
Sustainability also benefited. Bouygues Construction has committed to reduce its carbon emissions by 40% by 2030. The 3DEXPERIENCE platform is helping the company meet this objective by making it easier to calculate greenhouse gas emissions. The platform also allows Bouygues Construction to improve traceability, optimize materials and enhance the layouts of different elements to reduce waste.
“Pantin was a great adventure; together we are opening up an extraordinary field of possibilities. We expect this collaboration to help revolutionize the construction industry.”
Tailor-made construction with industrial methods
The two companies have formed a strategic partnership to encourage the construction industry to simplify and streamline project organization and interactions across the value chain, using cloud-based and mobile-enabled solutions. But the collaboration goes further, embracing in particular a more systemic and modular approach with the ambition of transforming the industry at large. This involves the creation and modeling of building-system product lines using modular and parametric components embedded with the teams' knowledge and know-how. Each project becomes an assembly of these smart components, constituting a virtual twin that is fully created in the 3DEXPERIENCE platform. Interactions among developers, architects, subcontractors and suppliers can then take place on the platform.
This approach makes it possible to achieve the most optimized and sustainable design for each project. Fabrication, supply, assembly and construction processes can then be streamlined, anticipating the various phases of a project at the earliest possible stage and planning their on-site implementation in the finest detail. The result: time savings and optimized allocation of resources, from materials to people.
Applying the virtual twin approach to the entire Infrastructure & Cities ecosystem
Dassault Systèmes’ manufacturing legacy will transform more than just building projects; it is helping to usher in a new level of productivity and improvement in the materials used in construction processes, the energy that powers the infrastructure and supply chain, and even the communities in which they are built.
- Materials: AES
- Energy: ISC
- Infrastructure: CRDC
- Region: Grand Est
1. Materials: AES
The world is trying reduce reliance on fossil fuels and generate less waste, and AES Autonome Energiesysteme has an innovative approach to this problem: recycle waste where it is generated and use it for that site’s energy supply. The German startup’s small-scale recycling plants can improve material reuse by decomposing organic structures into gas, oil and ashes, and using that for on-site heat/electricity generation and energy consumption.
As a member of our 3DEXPERIENCE Lab, AES has access to the 3DEXPERIENCE platform for project planning, part design, fluid simulation and more, helping its customers reduce CO2 footprint and costs.
2. Energy: ISC
ISC Consulting Engineering needed to centrally store its extensive project portfolio and design catalog for offshore substations.
“Creating a virtual twin is something we’ve always been hoping for. We’ll need everyone in the supply chain to understand that it makes good sense to spend more time and money on the design upfront so it’s complete and leaves no decisions to be made during fabrication. As the industry moves towards a turnkey construction contracts (EPC) approach, I can see the need for this more precise digital representation to carry out operations more efficiently.”
Christian Barlach,
R&D Manager, ISC
3. Infrastructure: CRDC
China Railway Design Corporation (CRDC) needed to improve its win rate of large-scale railway projects in China and abroad by adopting a novel approach to improve design efficiency and quality. CRDC is using virtual twins on the 3DEXPERIENCE platform to model projects based on design and engineering templates, to test more design alternatives, and to validate their possibility.
“We believe that the integrated 3DEXPERIENCE platform and its unified data source will improve efficiency and design consistency through better communication between our design, engineering and construction teams. It’s a more seamless way of working.”
Changjin Wang
Deputy Chief Engineer, CRDC
4. Region: Grand Est
The 3DEXPERIENCE platform has helped Grand Est, a major region in France with 5.5 million inhabitants, monitor and anticipate the impact of the COVID pandemic. By collecting and analyzing anonymized health data, Dassault Systèmes information intelligence solutions helped political and administrative authorities make better-informed decisions. This cockpit also included a predictive algorithm capable of projecting the number of patients in Intensive Care Units (ICU) three months ahead, thus providing hospitals with very powerful insights to anticipate future waves and adapt their resources accordingly.