Airbus
Airbus utilise les applications de Dassault Systèmes pour concevoir, simuler et fabriquer sur une plateforme unique, où les employés et les fournisseurs collaborent en temps réel sur une maquette numérique commune.
Une prouesse technologique
Dans le cadre de son programme « Future by Airbus », Airbus a demandé à 20 000 personnes, en ligne et lors de salons aéronautiques et d’événements, ce qu’ils attendaient des voyages aériens en 2050. Les réponses ne sont pas surprenantes : des voyages moins chers, plus écologiques, plus durables, moins stressants, plus silencieux et plus ludiques. Par le passé, amener les passagers où ils voulaient se rendre, en toute sécurité et en respectant les horaires, était suffisant. C’est encore vrai de nos jours, mais les compagnies aériennes doivent maintenant se concentrer sur l’expérience des passagers en vol. Avec l'A350 XWB (Xtra-Wide Body) – dernier né de la famille des long-courriers Airbus – l'avionneur mise sur la qualité de l'expérience passager. Fort de 750 commandes, il semble que les clients partagent cet avis.
De l'ergonomie de la cabine au divertissement en vol, l'A350 XWB a été conçu avec l'expérience passager à l'esprit. L'A350 XWB combine les derniers progrès en matière d'aérodynamisme des ailes et une cellule intelligente. Le fuselage et les structures d'ailes sont en fibre de carbone – soit plus de 50 % de l'appareil entier. « L'A350 XWB est le premier appareil qui utilise aussi intensivement ce matériau léger qui contribue énormément à son économie de carburant », explique Didier Evrard, vice-président exécutif et directeur du programme A350 XWB chez Airbus. « Sa conception d'aile avancée fait du A350 XWB un avion plus silencieux et plus aérodynamique. Le vol sera une expérience inédite. »
Pour atteindre cet objectif, Airbus a déployé les applications de Dassault Systèmes pour piloter une solution collaborative globale tout au long de la chaîne de valeur entre l'ingénierie et la fabrication, intégrant des améliorations nouvelles par rapport aux programmes précédents.
Innovation collaborative
Atteignant un niveau sans précédent, la collaboration est à la proue de la stratégie d'innovation d'Airbus. « Lorsque nous avons démarré le programme », précise D. Evrard, « il nous a fallu développer des méthodes et des outils radicalement différents de ceux de l'A380, non seulement pour veiller à ce que tous les ingénieurs impliqués dans le développement travaillent sur la même plate-forme de conception, mais aussi pour qu'ils puissent communiquer au sein d'un même environnement. » Sur le programme de l'A350 XWB, jusqu'à 4 000 personnes étaient connectées quotidiennement à la plate-forme, 85 % d'entre eux provenant de la chaîne d'approvisionnement.
« Pour les programmes précédents, chaque site possédait sa propre maquette numérique et chacun travaillait dans son coin », explique Antoine Scotto, directeur du programme de gestion du cycle de vie des produits pour l'A350 XWB chez Airbus de 2007 à 2011. Le manque de communication rallongeait le temps de conception et fut un facteur d'erreurs qui se sont révélées coûteuses. « Cette fois-ci, nous avons fédéré nos plates-formes de développement dans ENOVIA et fournit aux employés d'Airbus et au-delà l'accès à cette référence de données unique. Avec ENOVIA, la synchronisation ne prend que quelques minutes, contre plusieurs jours auparavant », ajoute-t-il.
En repensant ses processus de développement, Airbus a facilité la collaboration des phases de conception et de développement jusqu'à la production. « Les solutions de Dassault Systèmes ont contribué à libérer un échange collectif d'idées parmi les personnes impliquées dans le programme, et en fin de compte à améliorer l'efficacité de chacun », affirme A. Scotto.
Nous avons harmonisé nos processus, nos méthodes et nos outils et gagné ainsi un temps précieux qui a pu être consacré à l’innovation.
Simplifier les processus, améliorer la qualité
« Nous avions de nombreux défis à relever y compris un calendrier de développement très serré et la nécessité d'accélérer rapidement les rythmes de production pour honorer nos engagements en termes de livraison », rappelle D. Evrard. « Les solutions de Dassault Systèmes nous ont permis d'améliorer significativement notre qualité et notre efficacité de conception. » « Nous avons utilisé CATIA pour concevoir entièrement en 3D la structure de l'avion, les systèmes d'installation, la tuyauterie, les pièces composites et les systèmes électriques », explique A. Scotto.
Par exemple, Airbus a réinventé sa façon de dimensionner et d’installer les systèmes hydrauliques et électriques. « Avec CATIA, nous avons mis en œuvre une approche en 3D Master intégral pour mettre au point l'installation des faisceaux électriques de l'A350 XWB. Le nouveau design simplifie le processus et améliore la qualité générale de la conception », ajoute A. Scotto. L’harmonisation du processus d’installation des câbles de bout en bout a permis de diminuer les coûts et les délais de production, et d’accélérer la montée en cadence industrielle de l’A350 XWB. « Les ingénieurs ont réduit de 50 % le temps nécessaire à la mise à jour d’un plan d’installation et de 25 % le nombre de demandes de modifications conceptuelles par rapport à la création manuelle de dessins en 2D. Tout a été installé, adapté et vérifié numériquement. Ainsi, les erreurs éventuelles ont pu être corrigées avant l’installation physique », ajoute-t-il.
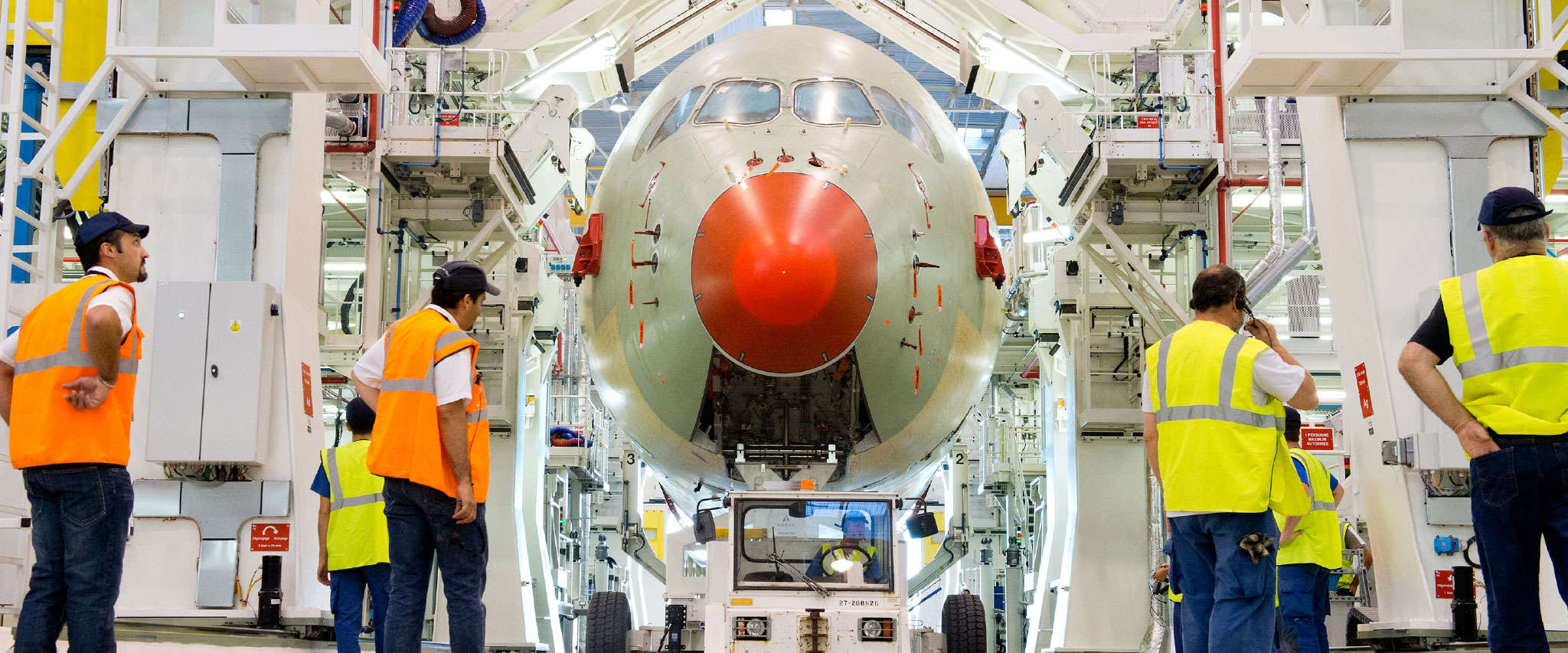
Augmentation spectaculaire de l'efficacité
La maquette numérique servait de lien entre la fabrication et le bureau de conception chez Airbus. « Toute modification apportée par le bureau de conception était communiquée à la fabrication en temps réel. Cela nous a permis de réduire significativement le temps de production » explique A. Scotto. « La qualité de la conception était si exceptionnelle que la fabrication ne nous a presque jamais demandé de revoir notre copie », ajoute D. Evrard.
Les ingénieurs ont effectué des analyses non linéaires réalistes avec SIMULIA pour prédire, dès les premières étapes du processus de conception, la robustesse et le comportement de la structure de l'avion. « Nous avons créé des modèles de simulation de grande ampleur sur la base des informations de conception de CATIA et réalisé des simulations structurelles non linéaires à grande échelle », déclare A. Scotto. « Avec SIMULIA, nous sommes passés d'une approche d'analyse linéaire approximative à une analyse non linéaire plus précise qui nous offre une meilleure compréhension du comportement de la structure dans chaque situation donnée. »
De l'ingénierie de fabrication à l'exploitation des usines, DELMIA a permis de sécuriser les délais de mise en œuvre du programme et la fabricabilité de l'avion. De plus, DELMIA a amélioré notre capacité à concevoir et à optimiser l'industrialisation du poste d'assemblage aux opérations d'assemblage élémentaires, et à prendre en charge l'automatisation. Pour l'airbus A330, le cycle de chaîne d'assemblage final prenait environ quatre mois. En commençant l'installation de la cabine très en amont, le processus d'assemblage de l'A350 XWB a pu être réduit d'environ 30 %.
L'assistance de 3DS Industry Services fut décisive dans la mise en œuvre et le déploiement de l'environnement complet de l'A350 XWB. « La collaboration entre les équipes Airbus et Dassault Systèmes a été très forte », affirme D. Evrard.
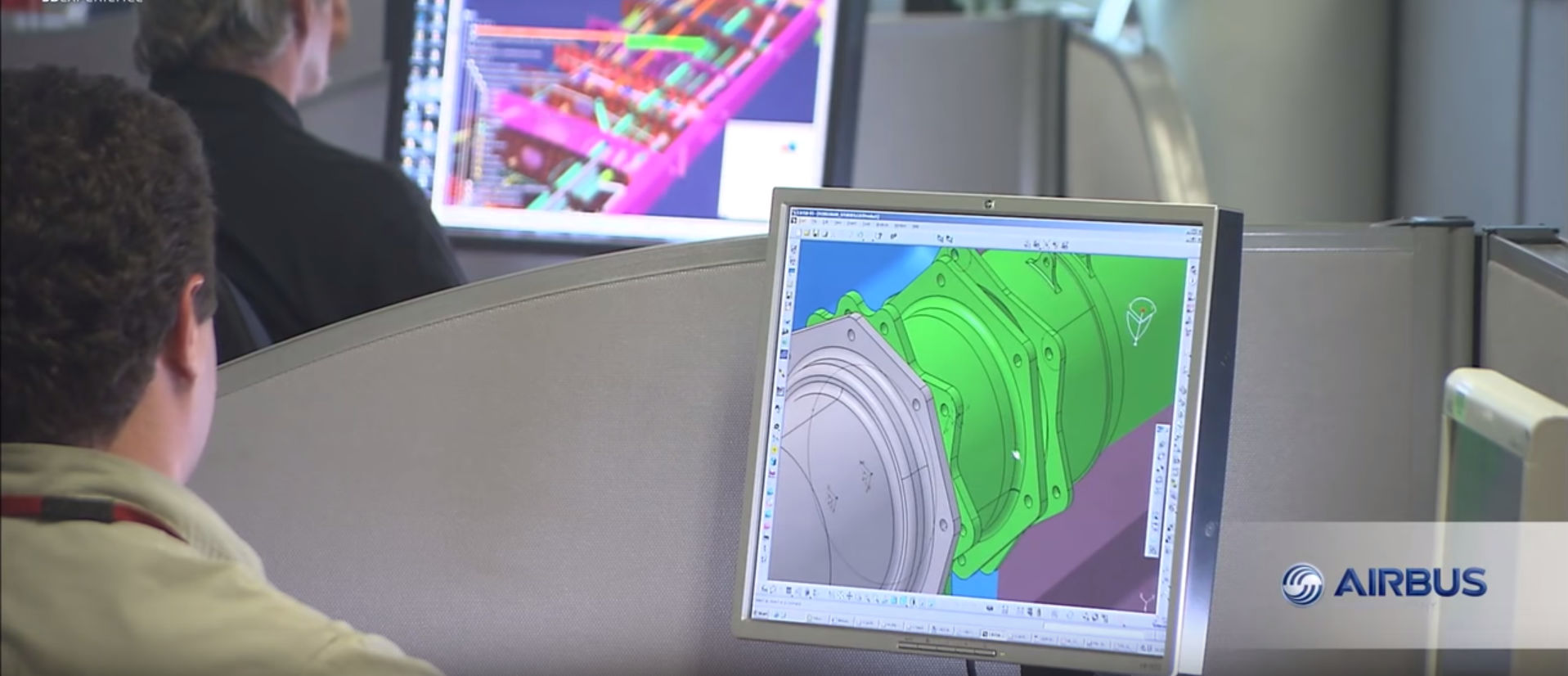
Continuité numérique pour les services client
Les avantages de l'utilisation d'une maquette numérique unique pour l'A350 XWB ne s'arrêtent pas à l'ingénierie et à la fabrication. Ils s'étendent aux processus utilisés en aval dans les services client. Si, dans les anciens programmes, les services client se basaient sur des illustrations dessinées à la main en 2D, la continuité numérique offerte par les solutions de Dassault Systèmes a permis à Airbus de mettre en œuvre des processus de service client qui réutilisaient directement la maquette numérique.
Par exemple, grâce à 3DVIA, Airbus a mis en œuvre un système de réparation et de maintenance structurelle (SRM) permettant d'accéder, d'interroger et de naviguer dans la maquette numérique, afin d'identifier les pièces structurelles devant être réparées ou pouvant encore patienter. 3DVIA permet notamment une identification beaucoup plus aisée des pièces ainsi que l'élimination du travail manuel requis pour créer les illustrations 2D et les légendes.
Vol inaugural et futur
Les applications de Dassault Systèmes sont désormais au cœur stratégique du programme A350 XWB. Le véritable moment de vérité fut le premier vol de l'A350 XWB le 14 juin 2013. « Toutes les attentes convergeaient vers cette date », rappelle D. Evrard. « De tous les défis que nous avons eu à affronter, c'était celui que tout le monde redoutait depuis les premières esquisses. Ce premier vol fut un succès. » Le nouveau défi de l'équipe A350 XWB consiste à accélérer le rythme de production, en collaboration avec sa chaîne logistique, afin de respecter le calendrier de livraison. « Avec toutes les personnes requises en mesure d'accéder à une maquette numérique commune, la communication est simple, les décisions se prennent à la volée et les problèmes se résolvent plus vite », affirme A. Scotto.
« Le projet A350 XWB présentait d'immenses difficultés techniques, technologiques et organisationnelles au regard de la complexité du programme et du nombre d'intervenants extérieurs », explique D. Evrard. « Les solutions de Dassault Systèmes nous ont permis d'harmoniser nos processus, nos méthodes et nos outils et de gagner ainsi un temps précieux qui a pu être consacré à l’innovation. Pour mon dernier programme au poste de directeur, je n'aurais pas pu rêver d'un challenge plus excitant. »
Airbus
Basé à Toulouse, Airbus appartient à Airbus Group, leader mondial dans le secteur de l'aéronautique, de la défense et des services associés. L'attention accordée aux clients, le savoir-faire commercial, la maîtrise technologique et l'efficacité de la fabrication ont propulsé Airbus au premier rang de l'industrie et en ont fait l'avionneur numéro un dans le monde. La gamme moderne et complète d'Airbus comprend des familles d'appareils de 107 à 525 sièges couronnés de succès.
Pour plus d'informations, www.a350xwb.com