Redonner la priorité à une production durable
Les jumeaux virtuels révolutionnent les industries manufacturières. Ils ouvrent la voie à de nouvelles façons de créer des produits et services : priorité au développement durable et à la diminution des émissions de carbone; priorité à l’expérience; développement au sein des écosystèmes de modes de collaboration faisant émerger des modèles économiques inclusifs.
JUSQU’ICI
Le produit était l’alpha et l’oméga de l’industrie
DÉSORMAIS
Les industriels font du développement durable leur priorité
Faire du développement durable un impératif
Les industriels sont à la recherche de nouvelles manières de maîtriser le cycle de vie de leurs produits pour deux raisons : apporter de nouvelles expériences à leurs utilisateurs et de nouvelles solutions au changement climatique. Pour cela, il faut repenser chaque étape du processus, de la conception à la fin de cycle de vie du produit, en passant par son utilisation. Ici, les jumeaux virtuels jouent un rôle clé pour accélérer la transition vers un monde durable. Ils aident les entreprises à faire des économies et à réduire leur consommation de ressources comme leur empreinte carbone, mais ils peuvent aussi faire émerger des innovations de rupture et des modèles économiques agiles, circulaires et centrés sur le client. Les jumeaux virtuels permettent de raccourcir le temps de développement d’un produit, d’améliorer la qualité de fabrication, d’utiliser plus efficacement les ressources et de mieux les valoriser.
Partout dans le monde, cette technologie accélère la mise sur le marché et réduit les risques des projets complexes. Des atouts qui expliquent son utilisation dans la conception de 85% des véhicules électriques et plus de 75% des éoliennes, ainsi que dans des projets pionners du développement durable comme le premier avion à propulsion solaire.
Cette transformation touche presque toutes les entreprises, tous secteurs d’activité confondus. Une start-up de batteries au lithium comme Olenergies et un producteur de papier comme Metsä Board partagent le même impératif de développement durable et peuvent compter sur les jumeaux virtuels pour trouver des solutions.
Olenergies
La 3DEXPERIENCE sur le cloud a permis au fabricant de batterie au lithium sans cobalt, Olenergies d’assurer l’ensemble du processus de fabrication de la conception, à la fabrication en passant par l’intégration de ses fournisseurs. La start-up française peut ainsi trouver des solutions et valider de nouvelles solutions en réduisant les coûts des matières premières et de gestion de projet. Les jumeaux virtuels développés sur la plateforme évitent en effet les déplacements des personnes et l’envoi des prototypes physiques à travers le monde, puisque tous les employés, partenaires et fournisseurs peuvent collaborer en temps réel, de manière sécurisée, où qu’ils soient.
Metsä Board
Pour répondre à la demande d’emballages plus durables, le finlandais Metsä Board, l’un des premiers producteurs de carton en Europe, cherchait une alternative aux prototypes physiques. Il s’est appuyé sur les outils de pointe de la plateforme 3DEXPERIENCE pour créer des jumeaux virtuels de ses solutions d’emballage et conduire des simulations permettant de comparer rapidement leurs performances à celles des emballages couramment utilisés par l’entreprise.
Priorité à l’expérience
Conscientes des conséquences de leurs décisions, les entreprises doivent aussi satisfaire les besoins de personnalisation de leurs clients. Sans oublier de réfléchir à l’usage qui sera fait de leurs produits tout au long de leur cycle de vie, voire lors de leur seconde vie.
Viscon
Entreprise hollandaise, Viscon fabrique des machines et des lignes de production innovantes pour l’industrie agroalimentaire. Pour mieux servir ses clients et conquérir les nouveaux marchés, Viscon a entrepris de cartographier ses processus de A à Z : conception, fabrication, et services virtuels. Grâce aux jumeaux virtuels créés sur la plateforme cloud 3DEXPERIENCE, l’entreprise améliore l’expérience de vente en montrant des maquettes 3D des modules et machines déjà configurés. Le temps de mise en service est réduit, et toute la qualité de la prestation s’en trouve améliorée.
Vertical Aerospace
Vertical Aerospace, l’un des leaders britanniques de l’aéronautique et des technologies, développe un aéronef électrique à quatre places, le VX4, en vue de décrocher toutes les certifications nécessaires à des vols commerciaux d’ici à 2025. Pour répondre au degré de précision exigé par l’entreprise, le plus grand soin doit être accordé à chaque composant de l’appareil. Les ingénieurs comme les équipes de supply chain s’appuient sur la plateforme 3DEXPERIENCE pour concevoir, tester et valider chaque élément via les jumeaux virtuels.
« L’appareil que nous développons est un véhicule 100% électrique, qui fonctionne sur batterie. Les technologies que nous utilisons évoluent profondement. Le modèle sur lequel nous travaillons est doté de nombreuses fonctions automatiques, en particulier une grande partie des tâches de pilotage sont automatisées. Le pilote reste néanmoins aux commandes et peut reprendre le contrôle à tout moment. »
Michael Cervenka,
Directeur général de Vertical Aerospace
Réinventer la manière de travailler ensemble
Le secteur manufacturier est enfin sous pression pour répondre aux attentes de collaborateurs particulièrement connectés, d’autant plus avec la crise sanitaire. Cela suppose d’adopter les technologies et les équipements qui façonnent les métiers dans les années qui viennent. Plus globalement, les besoins et les demandes de l’ensemble des parties prenantes doivent être pris en compte à chaque étape du cycle de production. Grâce aux jumeaux virtuels, les entreprises peuvent simuler la chaîne de valeur industrielle. Cela leur permet d’imaginer et de tester des nouveaux concepts rapidement et à moindre coût, et de construire un modèle économique plus agile, plus durable et centré sur le client.
Meyer Werft
Leader de la construction navale, Meyer Werft s’est appuyé sur la plateforme 3DEXPERIENCE pour dessiner le Disney Wish, l’un des premiers paquebots de croisière propulsés au GNL (gaz naturel liquéfié). La création du jumeau virtuel de ce navire extrêmement complexe mobilise des centaines d’équipes différentes qui travaillent ensemble sur la conception, la production, l’exploitation et la maintenance. La plateforme 3DEXPERIENCE, ouverte et intégrée, permet à Meyer Werft d’automatiser certains processus de conception et d’intégrer des données projet générées par les outils numériques de ses fournisseurs. Ainsi, la transition vers une expérience intégrée et unifiée se fait progressivement.
Nous prévoyons de recourir davantage à la plateforme 3DEXPERIENCE pour gagner en efficacité dans la conception et la construction de nos paquebots de croisière. Nous voulons harmoniser nos outils et processus sur l’ensemble de nos sites. Notre premier navire est en phase de construction, et notre partenariat avec Dassault Systèmes se poursuit plus étroitement que jamais.
Geberit
Pour renforcer la collaboration et adopter une approche multidisciplinaire basée sur les données, le fabricant suisse de produits sanitaires Geberit a choisi la plateforme 3DEXPERIENCE pour standardiser la fabrication de ses produits en céramique. L’entreprise a créé un jumeau virtuel de ses infrastructures et de ses équipements afin de simuler les trajectoires de ses machines lors de leur installation ou de leur déplacement. Sur certains projets, le jumeau virtuel a même simulé les systèmes mécaniques et les chaînes robotisées pour éviter des erreurs dans le processus de production.
Grace à sa plateforme unique, les concepteurs de moules sont libres d’explorer toutes sortes d’idées et de trouver la meilleure solution dès la phase de conception, sans passer par des prototypes physiques coûteux et longs à produire. Les partenaires externes en charge de développer les produits et les céramistes à travers l’Europe peuvent eux aussi utiliser la 3D pour fabriquer leurs moules. Geberit est désormais capable de détecter précocement les problèmes et d’éviter les reprises de production, génératrices de déchets et de surcoûts.
Notre partenariat avec Renault
Les jumeaux virtuels sur la plateforme 3DEXPERIENCE sont incontestablement des catalyseurs de la transformation de l’industrie manufacturière. En 2021, RENAULT a dévoilé sa stratégie « Renaulution », axée sur le développement de nouveaux véhicules , et de services de mobilité. La plateforme 3DEXPERIENCE accompagne l’entreprise avec ses solutions de partage des données produits en temps réel, tout au long du cycle de vie ainsi que les simulation des multiples configurations rendues possibles grâce aux jumeaux virtuels.
Dans la course à la décarbonation, les constructeurs automobiles accélèrent la mise sur le marché de véhicules électriques. Les jumeaux virtuels les aident à passer d’une logique produit à une approche basée sur l’expérience sous-tendue par la technologie, les services et la maîtrise des énergies.
Renault mettra la plateforme 3DEXPERIENCE à disposition de plus de 20000 collaborateurs travaillant dans la conception, l’ingénierie produit, l’ingénierie des procédés industriels, l’achat de pièces et de matériaux, l’étude des coûts et la qualité. Dans le monde entier, ils auront accès en temps réel aux mêmes systèmes et logiciels, modélisations et simulations 3D. La collaboration à grande échelle facilitera le partage d’informations entre les différentes fonctions et améliorera l’agilité au sein de l’entreprise tout en générant des économies et en réduisant d’environ un an le temps de développement d’un véhicule. De plus, toujours grâce au cloud, Renault bénéficiera en permanence des évolutions technologiques et des nouvelles fonctionnalités, sans attendre les mises à jour.
La plateforme 3DEXPERIENCE relie l’ingénierie à tous les autres métiers de l’entreprise. Dans cette grande organisation digitale, nous gagnerons en agilité, en rapidité et en efficacité pour accélérer l’avènement de la mobilité du futur.
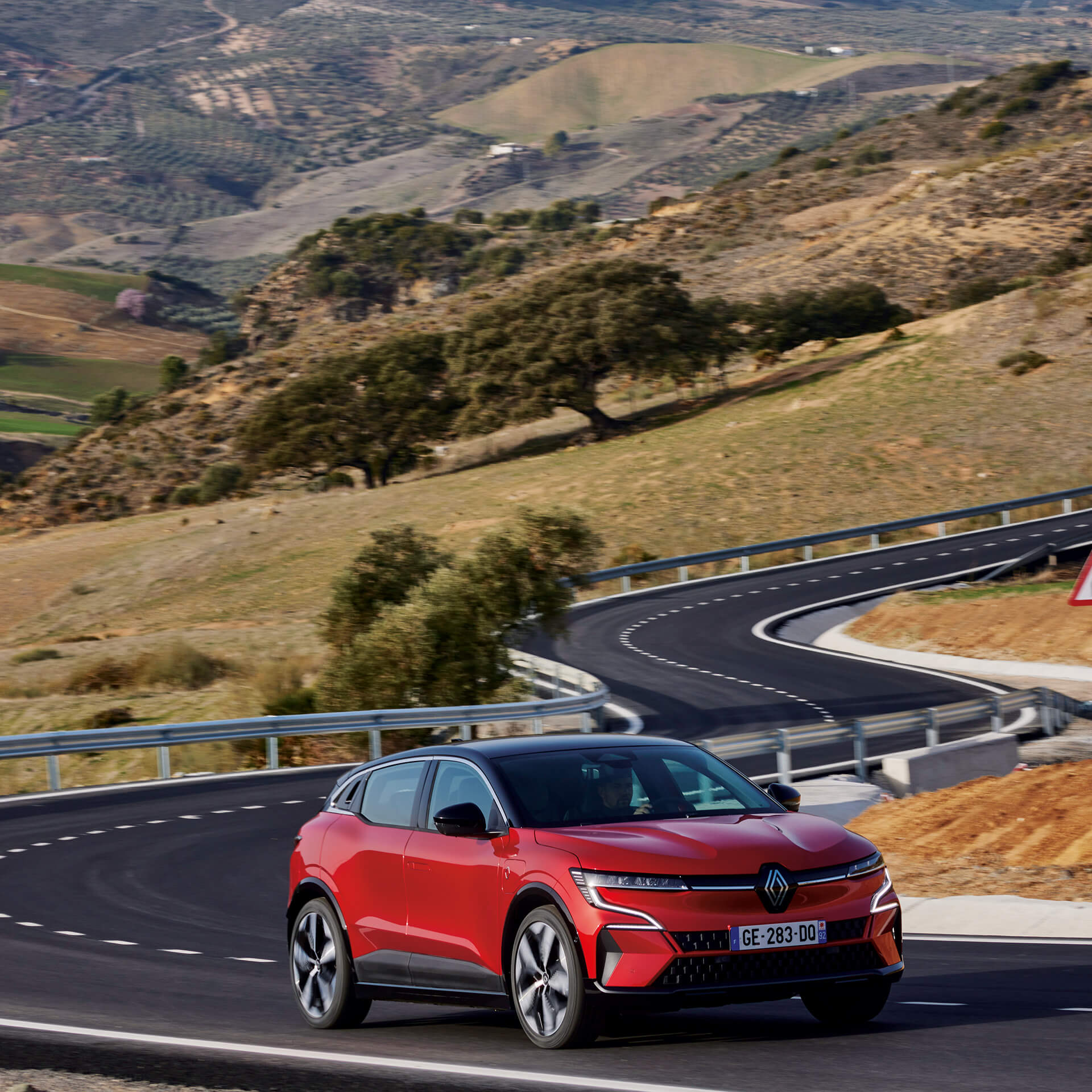