Parallel vs. Sequential
Founded in 1924, Metabo has produced electronic power equipment for more than 80 years. Building on its long tradition, Metabo has become a world brand present today in more than 120 countries.
Metabo power tools are distinguished by their design, ergonomics, technical innovation and robustness. Traditionally, Metabo’s new development projects began with an external designer drawing up sketches of a new product on paper and preparing a styrofoam model. Then, a technical designer created a 2D-model, while a surface modeller constructed the exterior surface.
This approach is time-consuming and requires many alterations, therefore Metabo is redesigning its development process with a strong focus on parallel development of parts.
Today, the development of new products at Metabo is initiated internally. The various disciplines work together from the design stage on the product’s form and technical production. The product designers, surface modellers, assembly designers and product marketing team all collaborate to create the product draft.
Every participant possesses the same level of knowledge. Assembly takes place using parallel construction, interdependent on CATIA models. By these methods changes can be propagated quickly to any model starting with the master model.
Using CATIA with ENOVIA SmarTeam, we gain controlled data access and consistency as well as the availability of development data and development documents.
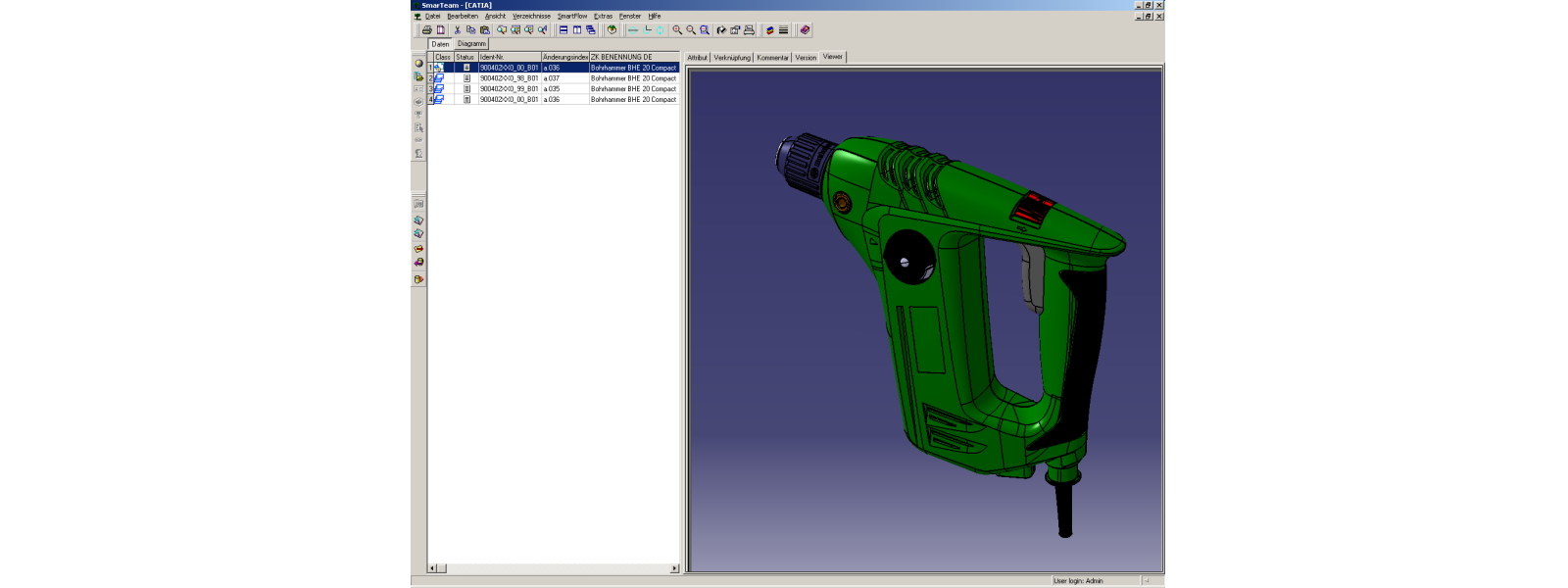
From 3D design sketch to surface model
Today at Metabo’s Nürtingen facility, a combination of external and internal designers work together. Starting with externally created design analysis, internal designers transfer the chosen design concept to a 3D geometric model in the CATIA Imagine & Shape module (IMA), taking into consideration the installation space available and providing alternatives if necessary. Design development takes place in parallel to the actual product construction.
Then the form construction of the support curve design is defined and the first CATIA model of the form is created. With CATIA, changes in the form model’s support curves can be made quickly, at minimum expense and with ease by the technical designer.
Within six weeks, using CATIA, a new product can be brought to a virtual prototype stage where it is 80% complete in design and form. With the consistent application of CATIA in all construction areas, updates can be produced rapidly by referencing the different models based on design, product and form, significantly reducing development time.
As proven in a pilot project, application of the CATIA Functional Molded Part module in form construction results in a drastic reduction in necessary design elements and in construction time in contrast to conventional construction. Its extensive functions for geometric production and rapid propagation of changes are key advantages.
In addition, marketing and distribution benefit at an early stage in development since Metabo can present a realistic image of the product. As a rule, after approximately ten days, a physical prototype designed using synthetic material is made available. If changes are necessary, new physical design models can be completed within one week.
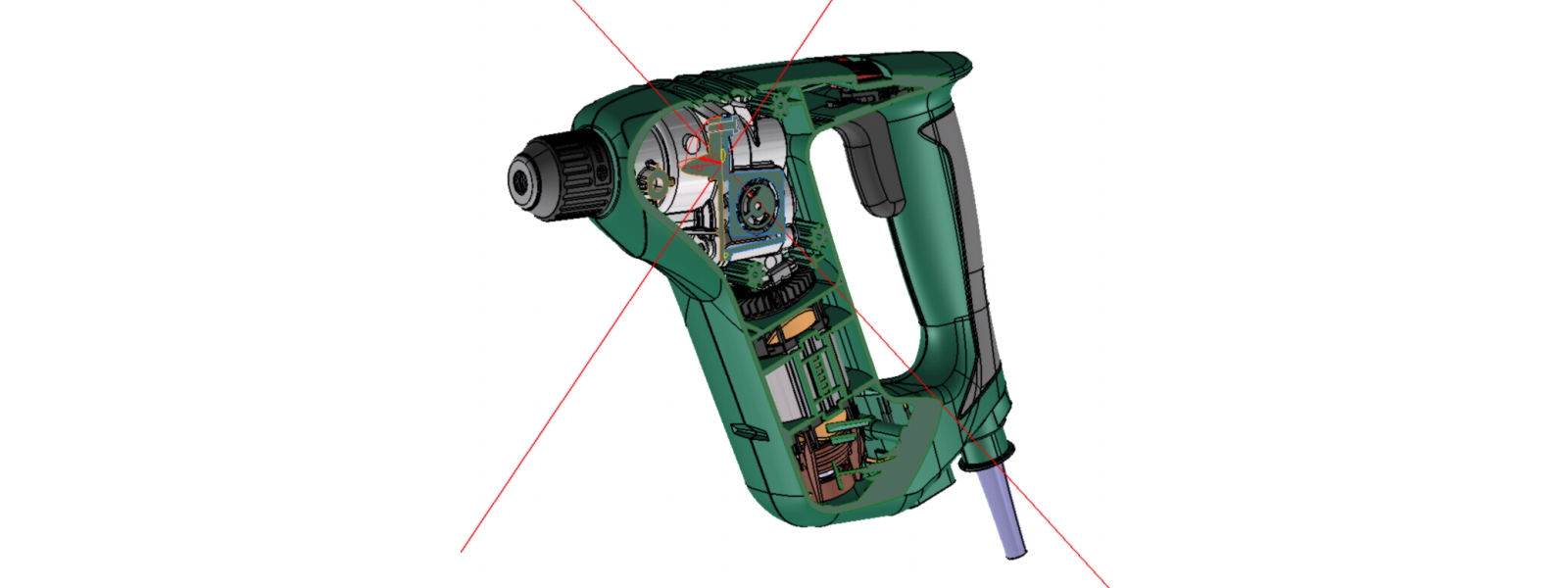
Effective profit and cost savings
Today, the market demands that companies not only offer fast response times, but an intelligent business approach to increasing productivity and the efficient use of development resources. Effective gains are achieved by using consistent data models and the rapid synchronization of interfaces to disciplines such as product construction and assembly.
Today in Nürtingen, a high percentage of the components and housing features of a new product come from collections catalogued entirely on templates. This is planned to be further expanded so that the engineer can focus more on customer requirements realization and innovation.
Coordination and decisions can be managed at a qualitative high level, thereby pushing the boundaries of parallel processes and reducing administrative work and alternative constructions. By implementing this concept into the multifunctional, combined teams with CATIA and ENOVIA SmarTeam, the time to market of a product can be shortened by several months.
With “Type3” from Vision Numeric,even seemingly simple elements, like elevated and recessed 3-D lettering on a tool’s housing, can be created quickly and easily, adding key value to the design.
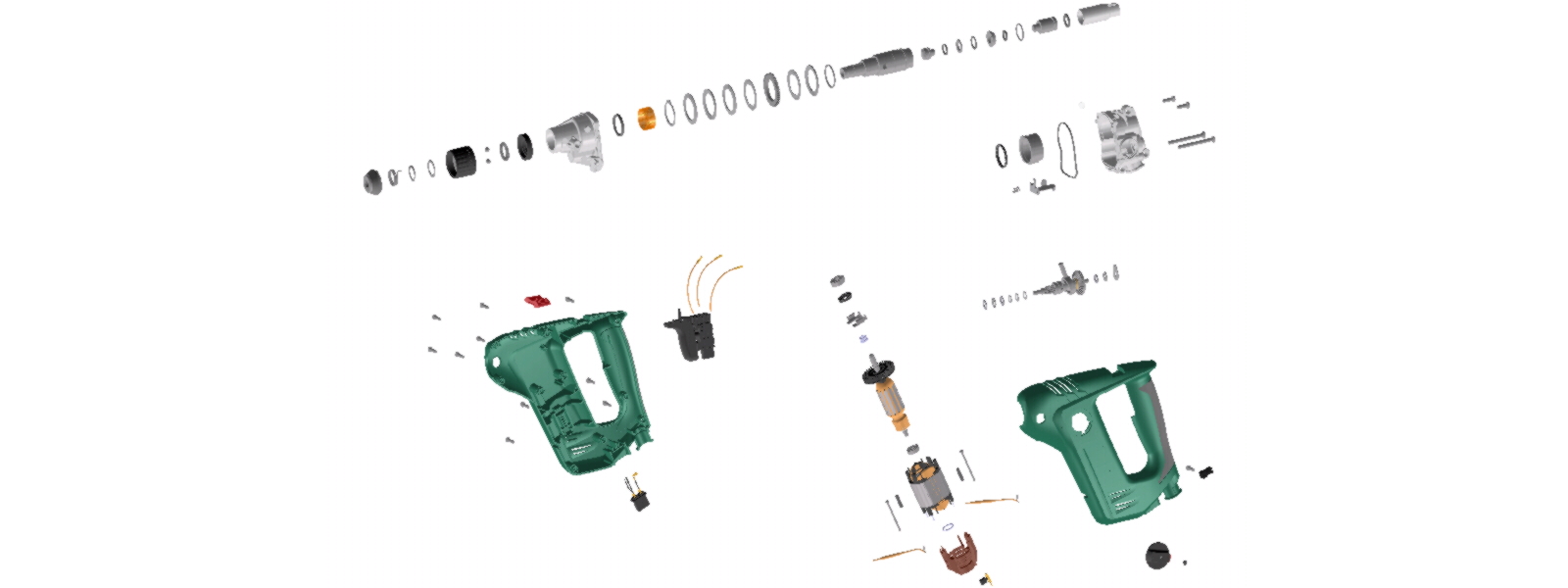