Soaring to great heights
Milan Bristela, CEO of BRM AERO based in the Czech Republic, is driven by a clear vision: to build the world’s best light and ultra-light sport aircraft. His planes are characterized by their navigational simplicity that also meet specific weight and performance regulations as defined by the national aviation authorities. “When my son Martin and I founded BRM AERO in 2009, we built our first plane in a rented hangar,” said Milan Bristela. “After five years, we had our own production facilities. We are passionate about designing, developing and flying airplanes. What drives us is doing something different than what other aircraft builders are doing. Our Bristell aircraft combine safety, ergonomics, and elegant curves that have seduced both beginner and experienced pilots over the years. They are also easy and inexpensive to maintain and repair because each part is interchangeable. In our short existence, we have sold over 300 planes in 26 countries.”
In today’s experience economy, even plane manufacturers are impacted by growing demands from customers who will not hesitate to shop around before making a purchase decision. “Our customers expect a great flying experience in an aesthetic, sophisticated, safe and easy-to-fly plane. They also expect their plane to be of the highest quality yet reasonably priced. This is why we are attentive to every detail,” Bristela said. “Our business primarily focuses on tailoring each plane to customers’ specifications. This way, they get a unique aircraft that best suits their needs. We try to stay ahead of our competition by proposing innovative solutions and continuously improving our design and manufacturing techniques.”
To maintain their competitive edge, BRM AERO adopted the 3DEXPERIENCE® platform and the Engineered to Flyindustry solution experience on the cloud for design as well as data management. “To make the highest quality planes we needed the best 3D solution on the market,” Bristela said. “Thanks to Engineered to Fly, we can design sophisticated parts down to the tiniest detail while accelerating design and manufacturing time. Setup on the cloud was fast and simple and we didn’t have to invest in additional hardware or skills and IT resources to manage a typical software installation.Moreover, because margins are low in the ultralight plane business, the ability to pay a monthly fee instead of investing in a full license is an advantage. We can, instead, dedicate our resources to developing the airplane and training designers on our methods and tools.”
High return on investment
In the past, finding the right design software was not an easy task. “Over the years, we’ve used other software solutions for 3D design that were not up to par with our expectations. But returning them to the vendor and recovering our investment was out of the question,” Bristela said. Another challenge for BRM AERO is finding qualified and experienced engineers. “Buying an expensive CAD solution and putting it in the hands of inexperienced people is risky because of the low rate of return,” he said. “However, with the 3DEXPERIENCE platform on the cloud things are different. The system was up and running immediately without the need to invest in new hardware or spend a lot of time on implementation. We were able to test the design applications on the cloud for three months before making a more permanent commitment. What’s important is that Engineered to Fly is tailored to the aviation industry and, therefore, responds to the way we work.”
Another reason why BRM AERO decided to use Engineered to Fly on the cloud was “because it is a cost-effective way to benefit from superior design technologies without the administrative hassles and costs,” Bristela said. “Dassault Systèmes takes care of software updates and backups, so we always work with the latest version and can be sure we have all available functions at hand. Our resources are, hence, free to focus on aircraft development and not IT management,” he said.
Technodat, a Dassault Systèmes business partner, presented the 3DEXPERIENCE platform to us and helped us get started by teaching us how to use the design applications on selected parts of the plane,” Bristela continued. “Their expertise was instrumental and after working with the solution for a few months our engineers gained sufficient knowledge to be proficient on their own. In a short time, they were able to import the 3D geometry of the fuselage, originally created with our previous solutions, into the 3DEXPERIENCE platform and to successfully create new production-ready sheet metal parts. Throughout this trial period, Technodat demonstrated a keen interest in our long-term development. They supported, and continue to support our designers when required. Moreover, even though they created an application to facilitate the exchange of part attributes between 3DEXPERIENCE and our ERP system, there was no need for any major tailoring. The out-of-the-box version of Engineered to Fly covered most of our needs.” Finally, data security and knowledge capitalization are other characteristics that convinced BRM AERO and the 3DEXPERIENCE platform offers both. “Our data is safe on the cloud and there is continuity because knowledge remains in our company rather than disappearing with a departing employee.”
3DEXPERIENCE on the cloud is a cost-effective way to benefit from superior design technologies without the administrative hassles and costs. Our resources are, hence, free to focus on aircraft development and not IT management.
Sheet metal design is a big plus
BRM AERO particularly values the sheet metal capabilities of Engineered to Fly. Engineers can digitally model and simulate the folding and unfolding of complex curved sheet metal part surfaces and verify for manufacturing feasibility, all within the same unified environment. “We can concurrently work on the 3D and flat pattern of a part using the solution’s Sheet Metal Engineering feature,” Bristela said. “Our previous solution only accepted 2D data. Now, we can produce the 3D shapes, bend and form them and match the holes with the skins and other parts that have to be assembled together. In effect, the aircraft’s frame is composed of sheet metal parts comprising 4,700 rivets. We can design the part in 3D and position the rivet holes in the digital model so that when we actually assemble them together, they come together right the first time. We also create multi-layered assemblies and perform interference checking on screen in 3D to make sure there are no collisions. Another advantage is Engineered to Fly’s hydroforming capabilities, which create structurally sturdy components with minimum material waste.”
Digital continuity and automated processes from engineering to construction enable those in production to receive the right information at the right time. “Automation reduces downstream construction errors because our shop floor is sure they work with the latest, most up-to-date geometry,” Bristela said. “If any design changes are made, they are visible to manufacturing, which helps to ensure the integrity of our product information.”
In addition to small two-seater airplanes, Milan Bristela plans on using the 3DEXPERIENCE platform for bigger projects in the near future. He also mentioned a secret project they are working on but declined to give away too much except that “we are working on a prototype that once we build and test its ergonomics and performance with our partners and friends, will be announced to the world. So stay tuned...”
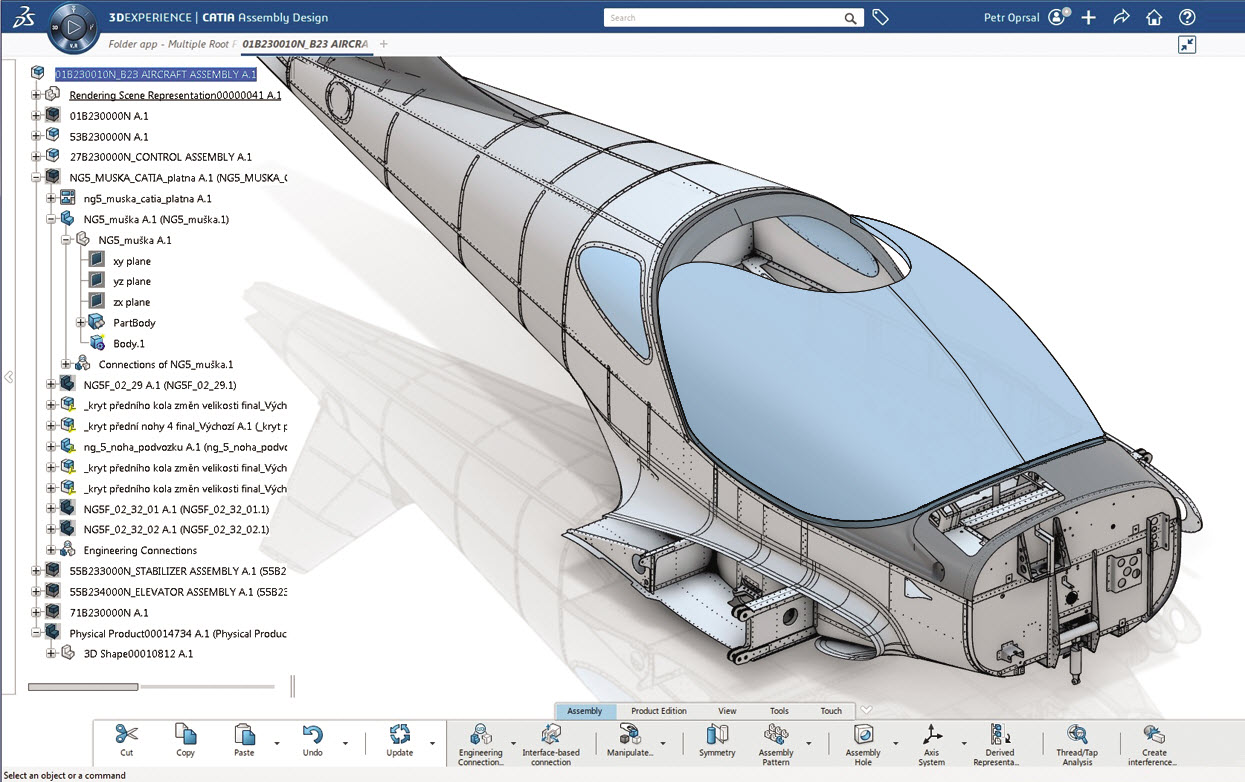
Product lifecycle part management
Aircraft parts need to be traced and maintained throughout their lifecycle. “With Engineered to Fly, we can manage the entire lifecycle of every component, from conception to servicing,” Bristela said. “We can track each part through versioning, transfer information such as part numbers, materials, costs or suppliers between the 3DEXPERIENCE platform and our ERP system, while making sure our documentation is correctly managed and linked to each part. Although I am convinced that the best tools to create a beautiful design are still paper and pen, I do appreciate the value of the 3D virtual product because it helps solve the technical and manufacturing details of our plane. Variables such as weight and material density are associated to each part so we can immediately have the weight of each subassembly. All the variables can be defined, analyzed, and modified on line in 3D, which helps optimize our designs and reduce the weight of the aircraft.”
The 3DEXPERIENCE platform is also open and flexible. “Our customers can submit new ideas or wishes for their aircraft and if it doesn’t interfere with the plane’s safety, we do our best to satisfy them. Because of its flexibility, the 3DEXPERIENCE platform makes it easier to adapt our designs in real time and to show our customers, in a digital environment, what their plane will look like,” Bristela said.
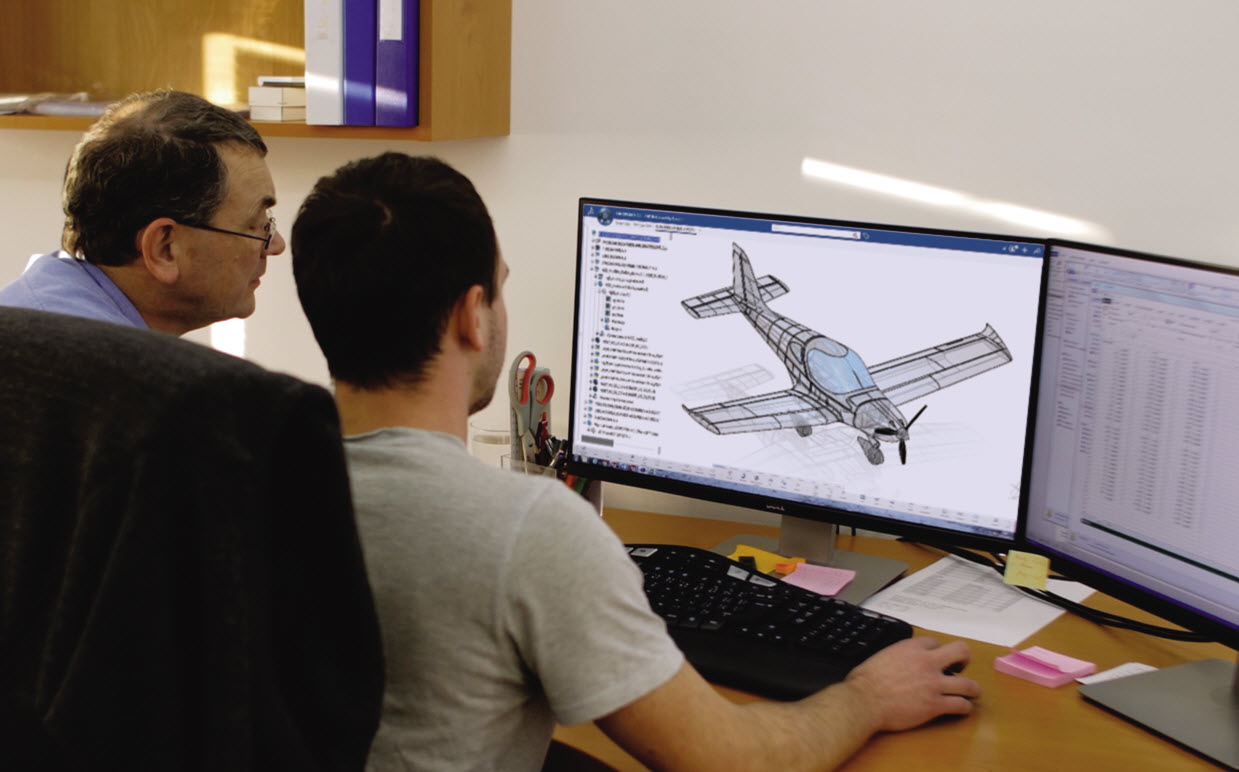
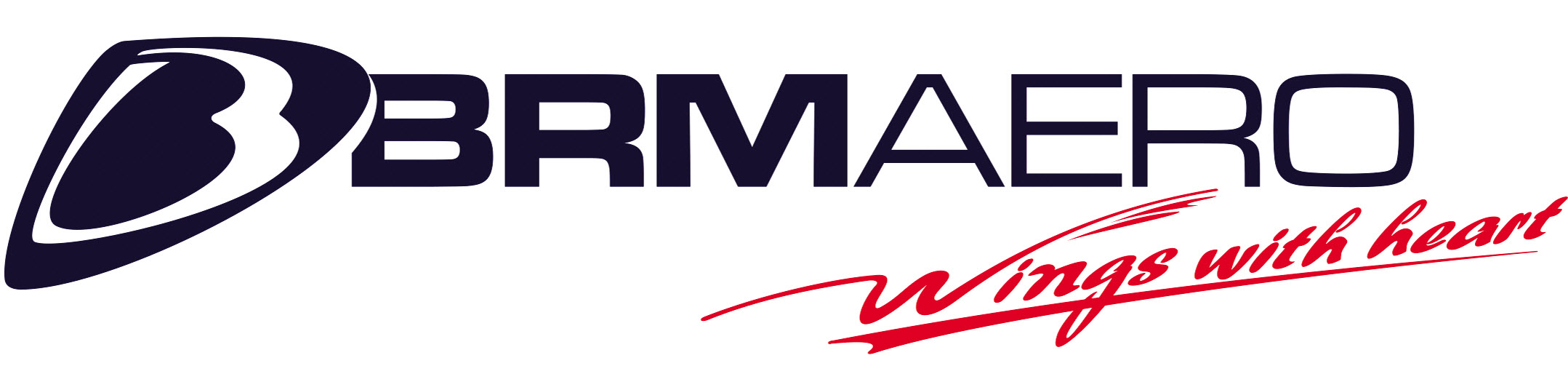
Focus on BRM AERO
Founded in 2009, BRM AERO develops, manufactures and sells ultra-light and light sport planes in its own production facilities with more than 6000 m2. The family business based in Czech Republic focuses on tailor made airplanes and distributes its products to more than 26 countries worldwide.
Products: BRISTELL Classic, BRISTELL RG and BRISTELL TDO
Employees: 70Headquarters: Kunovice, Czech Republic
For more information: www.brmaero.com
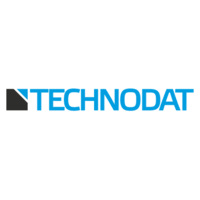
Focus on Technodat
For more than 30 years, TECHNODAT has been a preferred PLM and 3D solutions partner to customers of all sizes and in all industries, helping them develop and manufacture better products and innovative services faster. TECHNODAT provides value-added business consulting services, PLM project implementation and integration, training and support to its 250 customers in the Czech Republic and Slovakia. It is also a leading integrator and distributor of Dassault Systèmes solutions in these regions. TECHNODAT is a founding member of 3DX Alliance, a group of Dassault Systèmes partners with the mission to empower digital transformation for local and global customers across industries with the 3DEXPERIENCE platform.
For more information: https://www.technodat.cz