Bosch Car Multimedia
Bosch Car Multimedia tested the model-based systems engineering approach based on the 3DEXPERIENCE platform to efficiently connect each discipline in the product development.
Connected services for an inspiring driving experience
Connectivity opens up new horizons to develop smart vehicles and mobility services that make cars safer, more efficient, more convenient and more fun. Intelligent mobility solutions lead to a whole new way to experience driving, for example through Vehicle-to-Vehicle (V2V) or Vehicle-To-Infrastructure (V2I) communications. Bosch Car Multimedia, a division within Bosch Mobility Solutions, connects the inside and outside of a car by combining vehicle technology, the data cloud, and digital services to offer complete mobility solutions to drivers and passengers.
“Connectivity offers a huge potential,” Martin Gaedtke, director development instrumentation systems, Bosch Car Multimedia, said. “However it generates increasing complexity in our products and processes.”
Bosch Car Multimedia believes that the evolution of digital technology and the nearly endless possibilities connectivity has to offer that facilitate driving and entertain occupants throughout their journey create a third living space alongside that of the home and office. “We call this third living space ‘the travel space’. With the autonomous vehicle, for example, people can drive to work in the morning while conducting meetings along the way. Our job is to provide infotainment systems and networking solutions that can make this happen,” said Gaedtke.
Eliminating silos to increase productivity
The mechanics division of Bosch Car Multimedia is responsible for developing the components and overall design concept of display instruments of the vehicle’s interior. “Connectivity challenges us to design systems that are very sophisticated, hence, their complexity,” Bernd Hirt, group manager core function mechanics at Bosch Car Multimedia, said.
However, the various disciplines in this business unit, while sharing the same goals—e.g. to develop a new product for a car manufacturer—basically used different software solutions. By working in silos possible mutual influences on the whole system were discovered sometimes very late leading to higher costs. “In the development process you have different stakeholders who contribute to projects, working with their own tools and exchanging designs through interfaces,” Christian Simonis, project coordinator proof of concept for model-based systems engineering, at Bosch Car Multimedia said. “The concern with this is that a lot of information is lost. It’s not an effective way of working.”
“In an age of rising connectivity in our lives, as developers of networking solutions we must manage to work together to create a holistic digital model with all the attributes of each domain. This will invariably shorten time to market because we can work faster and more efficiently,” Bernd Hirt said.
Model-based systems engineering on the 3DEXPERIENCE platform enables the development of holistic mobility solutions and strengthens our future and competitiveness in this business.
Systems Engineering - a holistic approach
To tackle the complexity of modern connectivity systems, the company had to reengineer its engineering processes by bringing disciplines together and having them work in a more collaborative way. As longtime users of Dassault Systèmes’ CATIA, Bosch Car Multimedia used the 3DEXPERIENCE® platform in a proof of concept (PoC) for the development of a combined head-up display (CHUD) to acquire a better system understanding of kinematics.
A CHUD uses a small plastic screen positioned between the steering wheel and the windshield to project a virtual image of, for example, navigational information or traffic regulations, into the driver’s field of vision. “We wanted to analyze the potential of model-based systems engineering methodology on a collaborative platform. Due to the many years of cooperation with Dassault Systèmes, the 3DEXPERIENCE platform was the logical choice. It was important to be able to bring distributed teams together and integrate existing systems of each individual discipline into the platform, and this is what we set out to demonstrate with this proof of concept,” Bernd Hirt said.
Bosch Car Multimedia used among other Dassault Systèmes’ Companion eLearning courses to bring designers and engineers up to speed on the 3DEXPERIENCE platform. “We also use the companion training tutorials to train new employees. Training can be assigned depending on the role or area of responsibility and can be planned according to requirements and time schedules,” Marc Ölschläger, systems validation engineer at Bosch Car Multimedia said.
“We use model-based systems development to incorporate the requirements of mechanics, software, hardware, and kinematics across domains, to derive logical elements from them, and then to physically model our designs in the 3DEXPERIENCE platform,” Simonis said. “I emphasize this cross-domain aspect because being able to evaluate how a software parameter, for instance, affects a mechanical component will make our overall development process more effective.
“As project coordinator, using a model-based systems engineering approach makes it easier for me to combine individual disciplines and to evaluate them holistically,” Simonis added. “This front-loading is a must, if we want to evaluate product performance at an early stage, rather than after physical integration and testing. Another advantage of model-based systems engineering is that you can work with the latest and most current data. There are no delays due to model exports or imports; it’s always possible for any model developer, no matter which domain they come from, to access the latest version of designs from their colleagues.”
Because all applications are integrated in the platform, there is seamless data continuity. “For example, a finite element method (FEM) engineer develops his simulation model on the 3DEXPERIENCE platform, checks the model in SIMULIA, creates the FEM result, which by being on the platform, allows multiple disciplines including mechanical engineers to directly gain insights and access the result,” Bernd Hirt said.
According to Jürgen Hirt, project manager combiner headup display, Bosch Car Multimedia, model-based systems engineering also helps the company to reduce recursions in product development due to the acquired holistic understanding of the system, significantly shortening development time and lowering costs.
“In terms of validating our designs, a model-based systems engineering approach allows me to answer questions like ‘does my product really do what my customer expects?’ or ‘can I validate subsystems even though the full environment is not yet fully specified?’ in other words, can I perform software or hardware in the loop simulations?’,” Ölschläger said. “The answer to all these questions is yes because all relevant information is stored in one common digital model. This knowledge base allows subsystems to be validated at very early stages, meaning costly changes late in the development process can be avoided while significantly reducing the number of physical prototypes.”
A holistic digital model comprising all the attributes of each discipline invariably shortens time to market because we can work faster and more efficiently.
Virtual simulation provides early verification
“When designing the system’s architecture, it is important to consider the system requirements to determine how its components physically work together,” Micha Schönwiesner, systems behavior engineer at Bosch Car Multimedia, said. “In the past it was only possible to correctly detect design errors such as collisions or something not working properly using physical prototypes”, he added. “Now I can digitally see after my modeling if everything works as it should early on and show in 3D how adjusting certain parameters will influence the way the entire product functions.”
“With a model-based approach, we can analyze concepts and their weaknesses quicker, taking into account all tolerances in the early development phases, so that the system can be correctly interpreted,” Martin Schmidt, director customer program at Bosch Car Multimedia said. “For example, through kinematic simulation and behavior modeling we were able to adapt the design of a blockage detection algorithm, which practically eliminates injury to a person’s fingers. The kinematics of the head-up display are complex; virtual simulation is like a digital x-ray that allows us to visualize what happens during different use cases. This visual demonstration was of great value when discussing the kinematics of the CHUD with our customer and we received very positive feedback with respect to the model-based systems approach we followed here.
Schmidt also said the company sees benefits from a sales viewpoint. “Requests for quotations are processed faster because we can submit our proposals in less time thanks to insights gained with previous projects and the ability to reuse information capitalized in the system,” he said.
Miguel Filipe Santos, software engineer at Bosch Car Multimedia said a model-based systems engineering approach promotes discussion and collaboration, which enhances the way software, mechanical and hardware engineers work together. “We completely understand the specific requirements of the customers, which is an important part of software development. And we’re able to virtually test the way our programs interact with other systems. This is key to developing good software,” he said. “Moreover, we can implement, with the right level of quality and almost immediately, what the client wants, saving us considerable time in debugging sessions.”
“As engineers,” added Patrick Uebele, mechanical engineer, Bosch Car Multimedia, “we are also the interface between the OEMs and the suppliers, meaning that we need to know the requirements that the OEM places on our products and, in turn, translate these requirements into individual components for our suppliers. Working with the 3DEXPERIENCE platform helps us clearly know and describe these requirements from the very beginning of a project and to continuously compare them against our designs to make sure there is full compliance. In addition, we no longer have to process data separately for different steps, such as kinematics or thermal simulation, which saves us significant working time.”
Initiatives like A-SPICE1 are driving the automotive industry. “Using the platform we can ensure digital continuity from requirements to validation. For us, it was important to be able to integrate existing systems from each individual discipline; it was what we successfully confirmed with our proof-of-concept,” Gaedtke said. “In general, platforms such as Dassault Systèmes’ 3DEXPERIENCE enable the holistic approach of the MBSE methodology. As a result, we are achieving competitive advantages that are strengthening our future.“
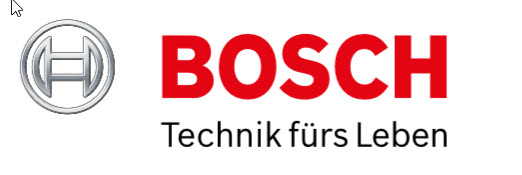
Focus on Bosch Car Multimedia
Bosch Car Multimedia (CM) is part of the business sector Bosch Mobility Solutions of Robert Bosch GmbH. With its intelligent solutions, CM contributes to making the integration of in-car entertainment, navigation, telematics and driver-assistance systems more flexible and efficient, while keeping it as easy as possible to operate. CM develops dedicated hardware and software solutions used in the latest products and actively helps to shape the future of connected mobility. The portfolio comprises driver information and infotainment systems as well as freely programmable instrumentation systems used on a global scale.
Products: infotainment, display, connectivity and HMI solutions with a focus on a fascinating user experience and highest ease of use
Associates: 8,250 (as per 12/2017)
Sales: 2.6 billion euros (as per 12/2018)
Headquarter: Hildesheim, Germany
For more information www.bosch-mobility-solutions.de/de/ www.bosch.de/unser-unternehmen/bosch-in-deutschland/hildesheim/