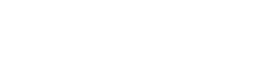
CATIA INDUSTRIAL INFRASTRUCTURES VIRTUAL TWIN
THE INFRASTRUCTURE DEVELOPMENT PROCESS DIGITALIZED TO ENSURE SUSTAINABILITY
INTRODUCTION
This interactive e-book is designed to show how 3DEXPERIENCE CATIA Virtual Twin can be used to design complex assets like plants and facilities, and to secure their sustainability in the context of transition from fossil fuels to green energy economy.
Building the Full Virtual Plant Model
- System engineering approach to master complexity
- Multi-discipline coordination
- Full design data consistency
- End-to-end traceability
- Efficient development process
- Including virtual system simulations and safety analysis
- Generative design from schematics to 3D
- Improve global execution and monitoring
- In link with operations - increase reliability and availability of assets
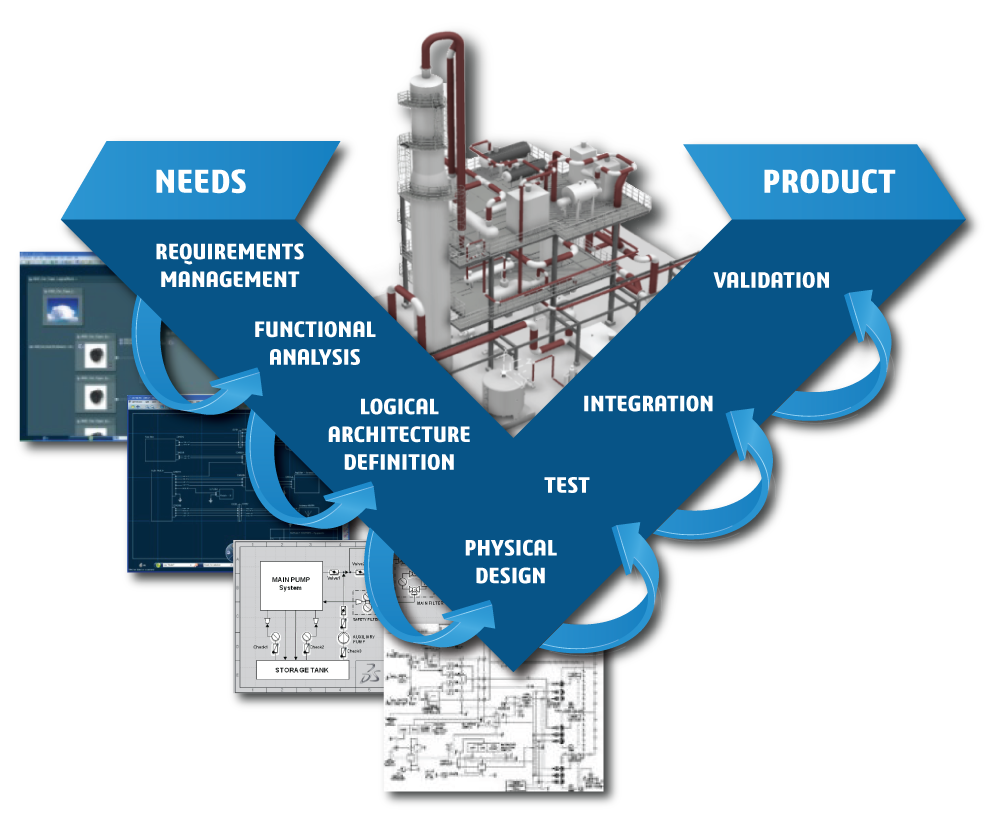
Manager & Users Involved
Head of Engineering
Head of Plant Operations
Head of
Design Office
Head of Project Management
Head of Construction Management
Design
Engineers
Safety
Engineers
Process
Engineers
Systems
Engineers
Civil
Engineers
Head of Engineering
The Head of Engineering leads the engineering team in the delivery of plant and facility functionality using 3DEXPERIENCE CATIA and helps the team in achieving and surpassing departmental goals. He provides technical guidance and direction, as well as hands-on resource and project management, for all site development activities.
Head of Plant Operations
The Head of Plant and Operations oversees the activities of production personnel to ensure efficient and safe work operations.
Head of Design Office
The Head of Design Office, manages design teams, and develop and supervise design projects.
Head of Project Management
Project managers are responsible for planning and overseeing projects to ensure they are completed in a timely fashion and within budget. Project managers plan and designate project resources, prepare budgets, monitor progress, and keep stakeholders informed the entire way.
Head of Construction Management
Project managers oversee the planning and delivery of construction projects. They ensure that work is completed on time and within budget. They organize logistics, delegate work and keep track of spending.
Design Engineers
Design engineers are responsible for the research and design of a company's new products and systems. They perform various tasks in an engineering department including drafting blueprints, creating test prototypes, and overseeing the manufacturing process. Also known as mechanical engineers.
Safety Engineers
Safety engineers look for ways to prevent accidents in the workplace. They inspect buildings and machines for hazards and safety violations, investigate accidents, determine what caused them, and educate workers on how to use safety equipment.
Process Engineers
Oversees and assesses existing processes and workflows. Optimizes productivity by designing, implementing and testing new procedures. Assembles reports to document process status and changes. Tracks metrics to discover areas for improvement and monitor upgrades.
Systems Engineers
Oversee complex energy conversion and distribution systems, work to improve energy storage systems, and manage the efficient use of energy in building, manufacturing, and processing systems. ESE professionals also study the secondary effects of energy usage from a local environmental impact, regional and national economic impact, and global climate change perspective.
Civil Engineers
Civil engineers create, improve and protect the environment in which we live. They plan, design and oversee construction and maintenance of building structures and infrastructure, such as roads, railways, airports, bridges, harbours, dams, irrigation projects, power plants, and water and sewerage systems.
Process Overview
The 3DExperience Platform has incredible collaboration, management and organization capabilities. It has the capability to manage any kind of requirements in a dedicated Requirements Breakdown Structure. Different layers contain: management of Business needs, Supply Chain technical specifications, Equipment Specification, Standards, etc.
From the PBS, asset visualization in 3D, you can see Light visualization of an entire site, access all the information related to this asset (in the Relational Explorer), such as technical specification, requirements, P&ID and which one it is used in. A single source of truth in a single environment. Traceability management allows all stakeholders to efficiently manage the impact of a change.
Within the RFLP approach, requirements can be detailed down to the equipment level parameters, allowing you to follow the attributes down to the lowest detail. Logical definition, schematics, can follow the project from the concept design stage as the BFD's or PFD's and finally evolve into detailed P&ID's that will update the 3D model during the basic and detail design.
As far as the 3D is concerned, you can trace the schematics and connect them to the objects during any stage of the project, taking into account geology, geo-location of the facility, zones and detailed 3D design that will finally represent the plant digital twin.
Based on the system approach, you have the capability to manage a logical site decomposition by zones and to reuse zones in any kind of schematics. This engineering environment allows you to reuse the PFD and/or P&ID to simulate the process by validating its behavior, simulating heat & mass balance, and to manage the output as requirements.
Based on the Process definition, a plant layout engineer will be able to pre-position the main equipment because of the synchronization between the schematics & 3D design. During conceptual design phase, all stakeholders will collaborate based on the same data to secure the quality and maturity, but also to respect compliance with Safety & Operations.
Since the RFLP approach is ensuring the data flow between different disciplines, project stages and objects, you are also able to evolve the 2D schematics into the the 3D objects. By simply picking the objects/symbols from the schematics, the system automatically transforms them into the 3D objects and places them within the previously schematic-defined zones.
A high level of automation allows you to easily navigate though complex diagrams and properly connect the equipment within the 3D.
Approaching the final stage of the project, you are able to automatically extract any information that is stored within the platform. Certain deliverables, such as drawings, reports, BOM’s etc are based on the templates, that can be re-used and reduce the creation time. ISO drawings are one of the deliverables that can be created throughout the templates.
Within the templates, you can define the specific zones for reports, both graphical and textual, extracting any attribute from the 3D models. Important to mention is that any change done on the 3D side, will reflect the change on the deliverables, ensured by the “3D master” approach.